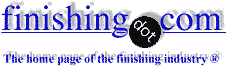
-----
Solutions to Problems in mechanical plating
Q. I am in a mechanical zinc plating plant. Zinc is plated over iron. We use a green liquid for creating a copper flash while plating zinc. But, most often the components (iron), become black in colour as soon as the addition is done. Also, sometimes the copper coating never occurs an the components remain black, why?
We use one white chemical and the label says it contains stannous chloride, why is a tin flash and copper flash needed?
Sometimes if plating does not occur I used to add a little more tin flash in between the zinc powder additions and if it is done immediately the plating occurs, is it because of tin or might be any other additive that is present in the chemical?
What other problems do occur while plating mechanically and what are all the causes and the ways to overcome?
brakes - Chennai, Tamil Nadu, India
2004
A. Don't these "green liquid" and "white chemical", etc., come with technical data sheets that explain what they are, how much is needed, and how to analyze the solutions and troubleshoot the problems, Shanmugam? It is very difficult from this distance to hazard a guess as to whether you've added too much "green liquid" or too little. You seem to be describing a whole host of uncontrolled process variables. Good luck.
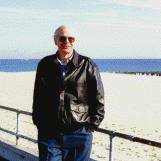
Ted Mooney, P.E.
Striving to live Aloha
finishing.com - Pine Beach, New Jersey
2004
A. What is happening is that your media is contaminated with unplated zinc. When you attempt the immersion coppering process, what should happen is that the copper in the acidic medium displaces the iron or steel. What IS happening is that unplated zinc is plating on the part prematurely; when you add the coppering compound, the copper is reduced to fine metallic form (black) and, typically, adhesion suffers. If you strip your media from unplated metal with sulfuric acid or hydrochloric (muriatic) acid, the problem will go away. The immersion copper deposit and the (electroless) tin deposit are necessary for adhesion.
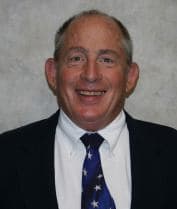
Tom Rochester
CTO - Jackson, Michigan, USA
Plating Systems & Technologies, Inc.

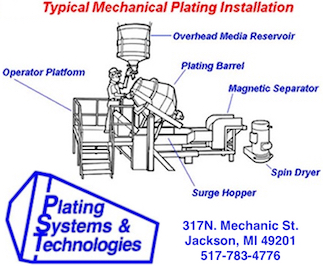
2004
Mechanical plating: rough edges on parts
Q. We plate small self piercing rivets and the problem we are having is rough edges. I've tried just about everything I could think of (changing speed, pitch, glass ratio ect.). Anyone have any tips they can pass on?
Joe adams- Wixom, Michigan
August 24, 2016
A. If you had an article like a self-piercing rivet but with no deep recess, a problem like this would probably be resolved by using larger beads or a higher media : parts ratio or both.
But the blind recess in self-piercing rivets creates some difficulties.
But I think that improvements can be made.
"High throw' chemistry (chemistry that throws more metal into the blind hole) would be better for SPR's than a generic promoter.
Media and the careful selection thereof and the media handling protocols can be useful in obtaining improved results.
I've been involved in mechanical plating since 1978, so you are listening to the 'voice of experience.'
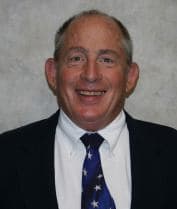
Tom Rochester
CTO - Jackson, Michigan, USA
Plating Systems & Technologies, Inc.

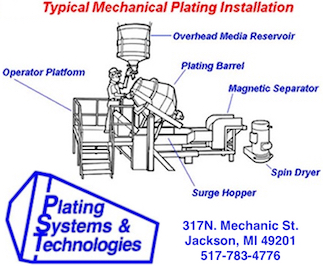
August 29, 2016

Q, A, or Comment on THIS thread -or- Start a NEW Thread