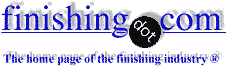
-----
What hardness/abrasion resistance from anodizing?
September 6, 2021
Q.
What is the nominal abrasion/wear resistance index for Type-II Anodizing?
Hi,
Recently I've been reading about the abrasion resistance of Type-III anodizing, in the 3.7.2.2 section of Mil-A-8625
https://quicksearch.dla.mil/qsDocDetails.aspx?ident_number=7074
The wear index for aluminum alloys in Type-III anodizing (depending of the alloy type) is clearly stated in the aforementioned section.
Some companies of great recognition worldwide even provide the surface hardness for type-III (which is commonly C60-C70 Rockwell), but nothing about the type-II.
By the other hand, the wear index for Type-II anodizing it is never specified in the standard, nor the corresponding surface hardness.
It is possible to find a standard surface hardness or wear resistance index for a Type-II Sulfuric-Acid anodizing? If not, what is the average measure you have got (obviously if, by chance, the client requested for it)?
Thanks in advance!
P.S.: My main goal is to get at least information about a measure for Type-II that clearly differentiates from Type-III. If we know the range for Type-III (C60-C70 Rockwell), then the Type-II should be noticeably lower than that, right?
- Dominican Republic
⇩ Related postings, oldest first ⇩
Q. Can someone familiar with anodizing process tell what type of Rockwell hardness can be achieved? How much can one increase the hardness of an aluminium workpiece surface?
Look forward to some response.
sait - Calgary, Alberta, Canada
2004
A. You can not get a true Rockwell hardness on anodize, You need a microhardness which you can only partially equate to a Rockwell. Reason, the anodize layer is a ceramic and the aluminum will give way enough, causing the ceramic coating to fracture and give you a low reading. If you would tell us what you intend to use this added hardness for, someone(S) might be able to give you an idea of what would work or options.
James Watts- Navarre, Florida
2004
A. Although Rockwell is not typically used in measuring hardness (normally, one would use a Taber abrader) on an anodized surface,you can expect 60-65 Rockwell on a decent hardcoat.
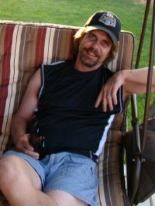
Marc Green
anodizer - Boise, Idaho
2004
A. To paraphrase from Wernick Pinner and Sheasby:
The usual methods for testing hardness, like Brinell or Vickers, isn't applicable because the give the hardness of the basis metal. They then go on to say that there are complications using Rockwell as well, and that the most appropriate methods are tests of abrasion resistance.
All that being said, the final abrasion resistance is affected by a bunch of different factors, most of which will be controlled by your anodizer, but alloy selection plays a part as well.
If everything is done correctly, and you choose an alloy that performs particularly well, the final abrasion resistance can exceed that of tool steel.
Mind you though - I'm a type II anodizer, not a hardcoater. My understanding may be a bit off, someone else on this site may be better able to answer.
Now, if you had a question about bulk anodizing of fasteners...
Compton, California, USA
2004
Q. What are some of the factors that would make the hardness change between parts? the base material, plating bath or amps? or all of above. What spec. calls out for hardness testing to be done to? I am getting all kinds of info from the net and each one is different as for as the hardness requirements. HELP!
Thanks Beth
- Dayton, Ohio, USA
2005
A. Pretty much all of the above plus the temperature of the acid bath as well. When anodizing in sulfuric acid there are two competing processes going on - the oxide coating is building due to the electricity being applied to the parts, and the oxide coating is being dissolved due to the action of the electrolyte. Factors that discourage the dissolution would favor hardness; this would include lower temperatures, lower acid concentrations, higher current densities...
Also, alloy selection is going to play a role as well, but I'm not certain which alloys end up harder than the others.
One last variable, sealing the part decreases hardness - but is necessary if you are going to dye the part.
With regard to specifications, the most often referenced anodizing spec is MIL-A-8625 / MIL-PRF-8625
[⇦ this spec on DLA] which specifies an abrasion resistance test as follows:
"4.5.5 Abrasion resistance. Test specimens, prepared In accordance with 4.3.3.2.4, shall be tested in accordance with Method 6192.1 of FED-STD-141 using CS-17 wheels with a 1000 gram load. The wheels shall revolve on the anodic coating at a speed of 70 revolutions per minute (RPM) for 10,000 cycles. The abrasion wheels shall be refaced at least once every 10,000 cycles. The wear index shall be determined after the 10,000 cycle period by dividing the weight loss by 10. The wear index shall meet the requirements of 3.7.2.2."
But it doesn't specify hardness test per se.
Good luck.
Compton, California, USA
2005
Wear index for aluminum without anodizing?
Q. If type III hard anodizing performance is measured by the wear index, where can we find wear index data for un-anodized aluminum like 6061?
Mark Woozley- gaithersburg, Maryland USA
May 16, 2014
A. Mark, a quick Google search led to this on 6063 Aluminum; if it's important to you, looks like the paper can be purchased.
http://utpedia.utp.edu.my/3822/
Matweb has a plethora of information, but nothing on the wear index. However it does have hardness values, which I'm sure can be compared with the hardness value of your typical hardcoat in order to get a feel for the improvement you'd see by hard anodizing.
https://www.matweb.com/search/datasheet.aspx?MatGUID=1b8c06d0ca7c456694c7777d9e10be5b
Obviously, by itself, aluminum is not the hardest of metals, with improvements being made by alloying it with Si, Zn, Cr, etc, etc. And of course, heat treating processes, and cryogenics processes can also be done to change the hardness values.
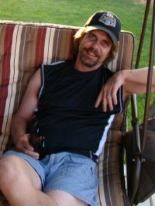
Marc Green
anodizer - Boise, Idaho
May 24, 2014
Q, A, or Comment on THIS thread -or- Start a NEW Thread