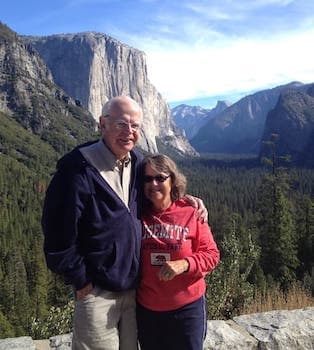
Curated with aloha by
Ted Mooney, P.E. RET
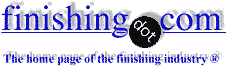
The authoritative public forum
for Metal Finishing 1989-2025
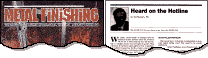
-----
Stainless steel corrosion by chloride ions ?
Q. Hello,
We are a small company in France, producing encapsulated raw material for cosmetic industry. We use a stainless steel machine (316SS), and we have had recent problem of green coloration in our products. We think it could be due to a previous preparation where we used 10% sodium chloride solution which could have done some corrosion to the stainless steel. Do you think this is possible (corrosion of stainless steel by NaCl solution at room temperature)?
How can we demonstrate that ? We have looked for Ni and Cr ions in the product, and we did not find them. Should we look for iron ions ? What could be the remedy ? Will passivation with nitric/fluorhydric acids solve the problem ?
Thank you very much for your answer. Sincerely
- PESSAC, FRANCE
1999
A. 316 SS has excellent corrosion resistance, but it is not impervious to rust. Chloride is an excellent rust cause with a little damp air moisture. After your NaCl step, increase your rinsing via sprays (mist) or added tanks. A final warm water tank and blow dry step will significantly reduce the corrosion. The probable thing that allowed the corrosion to form was trace smearing of ferric iron in the manufacturing step. Nitric acid or nitric acid/chromate will reduce this problem. Hydrofluoric acid is NOT a recommended step. There are some quite good citric acid proprietary products available now that are a lot safer to use.
James Watts- Navarre, Florida
1999
A. Rene - I have often seen stainless steel have corrosion because of high chlorine content of the water. Generally, this causes a "white rust" and is very damaging. It happens frequently in cooling applications where biofouling has occurred and the operator throws in a bunch of bleach to kill bacteria and algae in the recirculating tank. I hope this provides a starting point for your investigation. Good luck
Dan Brewerchemical process supplier - Gurnee, Illinois
1999
A. You may or may not have corrosion of the stainless steel from the chloride exposure, but I doubt that the green color that you are observing is the result of such corrosion. Green corrosion will occur on stainless steel only under very specific conditions, and the green is due to segregation of chromium. If you are not finding Cr or Ni in the green material, this is further evidence that the color is not from the SS. Do you have any copper in the system?
Pitting corrosion of stainless steel due to chlorides would certainly produce a rust-colored product. Passivation can be used to maintain a good corrosion resistant surface of stainless steel process vessel. There are many commercial products for this purpose. In the pharmaceutical industry, this process is often called "derouging", that is to remove the buildup of iron oxides on the stainless steel process surfaces. I would recommend a commercial product with technical support from the supplier, rather than a home-brew passivation treatment.
Inspection of the stainless steel process vessels for pitting corrosion can be very tricky. The pits are often undercut with only a microscopic opening at the surface. Look for small spots of red-brown stain on the surface, then probe these spots for a deeper pit under the surface.
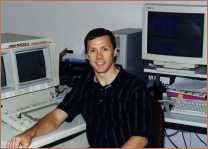
Larry Hanke
Minneapolis, Minnesota
1999
A. First of all, let me confirm that the green products you found are probably not issued from the stainless steel grade 316. At Tocopilla combined cycle power station located in the north of Chile, we face a high corrosion rate of our seawater submerged stainless. The problem is in fact the mixing of to unfavorable conditions: seawater and chlorine injection against biological fouling.
After 3 months only crevice corrosion appeared on the main cooling water pumps impellers made of 1.4408 SS grade (a kind of 316). This was due to chloride attack of the SS passive layer leading to a pitting corrosion. The active base metal remained therefore unprotected and a standard galvanic corrosion occurred between the passive layer (nobler metal or cathode) and the active metal (less noble metal, anode). All this created crevices in the impeller casings. All corrosion products found were red or brown (rusty).
The conclusion is: if you use SS material in a chloride environment, be sure you use the adequate grade of SS. Maybe, under certain concentrations, SS316 is not the best grade to fit your requirements. Have a look SS316HMo or SS317 or other grades with high molybdenum content and even with nitrogen content.
- Brussels
2000
A. Definitely in 304 stainless steel corrosion takes place by pitting corrosion caused due to Chloride ions, But its color is reddish brown, It is not green. Green color is seen in corrosion of Copper metal. So you must look if there is copper.
Abhishek T [surname deleted for privacy by Editor]- Roorkee, India
April 25, 2008
A. René L,
I have replicated a green color solution with stainless steel by submerging a s/s bolt in hydrochloric acid (muriatic acid, HCl). Did you ever clean the stainless with hydrochloric acid containing cleaning products? If so the HCl may have reacted with the stainless and a resulting green color could have been the result.
electropolishing shop - North Vancouver, British Columbia, Canada
September 17, 2009
2000
Q. Hi everyone,
We were using an AISI 316 SS plate heat exchanger to cool 80° C bi-distilled water (product side) with tap water (service side). After only 5 months of use the heat exchanger evidences significant holes on the product side due to what the equipment supplier has determined to be pit corrosion caused by a combination of chloride, high temperatures and stagnant water with air mixtures.
bi-distilled water: chlorides <= 0,5 ppm
tap water: chlorides <= 53 ppm
saturated vapor: chlorides <= 0,5 ppm
The equipment is sterilized once a day with pure saturated steam on the product side and then used for approx. 1 hr and then drained.
Can low chloride concentrations in the 1 ppm range actually cause this type of corrosion? Could the use of Titanium plates solve this problem? How does the steam thermal and mechanical shock affect the corrosion process? Could there be some other mechanism causing corrosion (presence of ozone, etc.)? Any comment will be greatly appreciated. Thanks in advance.
- Spain
Q. Hello
We are about to purchase an RO water treatment system for the dairy. To do so we need to present the required water quality. As we use SS304L for our piping and tanks, what would be the maximum ppm of chlorides allowed ? Thanks
dairy - Israel
2000
A. To the individual asking about the maximum chlorine concentration for an RO Water System, the answer is essentially zero. The corrosion of the 304SS is not the issue, because all RO membranes cannot tolerate even low concentrations of chlorine. Activated carbon filters are used to remove any chlorine prior to the RO system. Even slight leakage of chlorine damages the membranes rapidly.
Rick L [surname deleted for privacy by Editor]- Perrysburg, Ohio
2003
Q. I would like to ask in which way stainless steel react with bleach, and after that what could happen on the surface if in contact with an organic substrate? the steel surface become "reactive"?
Mario Rossipharma - Italy
February 26, 2009
Q. I would like to ask why stainless steel reacts with bleach? Thank you!
Leung T [surname deleted for privacy by Editor]student - Hong Kong
2004
A. This to hopefully answer the question presented by the student from Hong Kong, Mr.Leung T. The question was why stainless steel reacts with bleach?
1. There are over 50 grades of S.S., some are more expensive than others. S.S. that has higher concentrations of molybdenum in it are considered marine grade and resist chlorides much better. These grades are expensive. 316 is approximately 20 to 30% more expensive that grade 304.
2. What concentration is the bleach? Bleach is sodium hypochlorite (NaOCL)In the U.S.A., it can range across various concentrations. Chlorox bleach is typically 12.5% available chlorine or 125,000 ppm chlorine.
3. The chloride ion penetrates the chrome oxide layer that protects the metal then destroys the rest of the metal components.
Hope this helps. Chlorine is a Halogen and there are other such chemicals the spread destruction. fluorine, bromine, iodine. Note: they all have an "...ine ending in their name.
Pete Churchill
- Randolph, Massachusetts
May 19, 2009
Q. Dear Sirs
Concerning chloride action on 316 stainless steel, we are selecting the material for water injection pumps; this water contains 2500 ppm chlorides; what would be the appropriate material for this service?
Oil - Bogota, Colombia
August 27, 2008
Q. Hello to all,
We have been experiencing premature failure of 304 S.S. bolts used in the construction of main line gate valves in our water distribution system. Other buried infrastructure made of mild steel are rendered worthless with a few years. The problem has been traced to winter road salts (calcium chloride and sodium chloride)that find their way to the valves thru valve extensions, a direct route to the surface and by roadside melt / runoff that leaches to the pipes below. We are considering changing our specifications to include the use of 316 S.S. in all buried infrastructure with the addition of a topical application (No-Ox-Id) on all bolts prior to installation. In addition, we are strongly in favor of "wrapping" all buried infrastructure. Lab samples (obtained through valve extensions) of groundwater in the immediate vicinity of some valves, have yielded chloride levels of 3,520 mg/L and a pH of 7.6 We are facing a public who demands safe driving conditions in the winter and are paying a hidden price for this with a reduced life of our infrastructure. We trust that we are taking the proper response to this problem that impacts all communities that treat their roads in the winter, for the safety of the driving public.
Water & Sewer Supt. - Randolph, Massachusetts
May 16, 2009
Q. We use syringe pumps in our facility with 316SS lapped and polished bores. DI water or a neutral mineral oil are most often used in the pumps. I turned to this site to understand if I can use 1-3% NaCl brine in the mirror finished pumps without damage. It seems risky. What do you think, can I live with 1 or 2% NaCl w/o causing pitting to the pump bore at relatively low temperature?
However, while reading responses there seems to be general confusion between chlorine, chlorite, and chlorides. Please understand that these are not the same!. Chlorides are part of dissolved salt or seawater and will not damage RO membranes used for water purification. On the other hand, hypo-chlorites release the very oxidative element chlorine which will destroy many polymers - maybe those found in RO membranes. Thank you
- Kuala Lumpur, Malaysia
November 21, 2010
Q. Hi everyone,
I had a problem with our Stainless steel hand washing sink table.
The environment where it is placed is closed and very smelly because of chlorine that they used in the area although it is not contact with the product. The stand of the sink table and other part of it corroded. My initial finding is that it is because of the fumes and chlorine atoms may build up on the surface of the stainless steel thus corroding the sink table. Is my finding correct? any answer please thanks
IS 202 MORE CORROSION RESISTANT THAN 304?
product specialist and researcher - Davao City, Philippines
October 6, 2011
A. Hi, Rechie.
Chlorine is a gas, not a liquid. The gas evolves from bleach solutions. Hydrochloric acid is a gas dissolved in a liquid. So, although no bleach or acid may have splashed on it, the chlorine is still there to attack the stainless steel.
Regards,
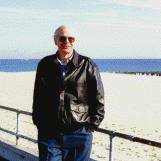
Ted Mooney, P.E.
Striving to live Aloha
finishing.com - Pine Beach, New Jersey
October 6, 2011
Q. Hi,
This is a follow up of my earlier question.The hand-washing sink we use is actually grade 304 stainless steel. The 304 SS stains due to the chlorinated water (calcium hypochlorite of 400 ppm) fumes that dominate the area.
What is the recommended chlorine present in water to not corrode the steel because of its fumes?
Thank you so much
Best regards,
Rechie
- Davo City, Philippines
October 27, 2011
Q. Hi every one
We had a problem in water piping. we have a lot of chloride in water and we use stainless steel 304 in a part of piping. after 5 years, we observe pitting. which type of steel we can use?
thank you
employee - Iran
October 10, 2011
Q. Can I use 304 stainless steel needle valves in chlorine gas? Will there be a corrosion problem or not?
Hessam Lohrasbi- Iran
December 22, 2011
Q. Hi all,
I would like to know procedures to retrieve sample (rust) from a stainless steel tank. The rust is in moist form.
Perhaps cotton bud or glass rod?
- Singapore
March 9, 2012
Q. Hello sirs,
I want to know which of the following materials: 316L SS, 1.4408 SS, and Alloy 20 should I use for storage of sulfuric acid.
Thank you
- Warri, Delta State, Nigeria
March 16, 2012
Q. We are a manufacturer of autopsy equipment. We recently provided sink stations in 316 stainless steel which are developing rust and pit marks. The facility is using a combination of bleach, hydrogen peroxide and Brillo pads ⇦ this on eBay or Amazon [affil links] to clean the units. Are any of these causing the problem? Thanks for the help.
Gino Joseph- Azusa, California, USA
June 5, 2012
A. Hi Gino. Perhaps brass wool could replace the Brillo, but bleach is still murder on 316 stainless.
Regards,
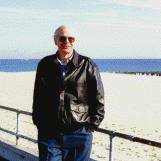
Ted Mooney, P.E.
Striving to live Aloha
finishing.com - Pine Beach, New Jersey
June 6, 2012
A. I recommend scrubbing with Barkeepers Friend
⇦ this on
eBay
or
Amazon [affil links] with water and dilute bleach, followed by dilute bleach rinse for sterilization, followed by a clean water rinse.
Using brillo may transfer free iron to the surface that will cause rust spots, so it should be avoided.
The combination of bleach and peroxide is counter-productive, since the peroxide will react with the bleach with the disinfecting power of each will be partially or totally destroyed. Use one or the other, and bleach is preferable since it will disinfect at low concentrations, whereas peroxide will not be effective at low concentration. Even 10-25 mg/L of bleach can be remarkably effective.
consultant - Cleveland Heights, Ohio
June 11, 2012
A. Ted is right, steel-based scrubbing pads should be replaced with something that doesn't contain iron (Scotchbrite perhaps), and bleach is a horrible thing to put on stainless. I realize that it's hard to break a customer off of bleach since they are only thinking about the need for sterilization, so they should be regularly giving the stainless a passivation treatment to counteract the bleach damage. This can be done safely and easily with citric acid based products. Extra measures are likely needed in this case since pit corrosion has already set in. Let us know if we can help.
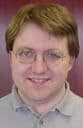
Ray Kremer
Stellar Solutions, Inc.

McHenry, Illinois
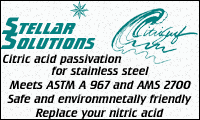
June 15, 2012
Q. Best shaft material for flow/speed measurement in pool, lake and ocean water. I'm developing an instrument for measuring open water speed using a small plastic propeller. I've used 316SS, 0.125 and .062 dia, as the shaft and noticed residue on the shaft after a week or so of use. This application requires low friction for accurate measurement. Considering going to ceramic but like the toughness of metal. The 316 shaft was actually a commercial dowel pin which is not passivated. Any recommendations for material? 317, 904 or ceramic?
Thanks
- Irvine, California, USA
June 19, 2012
A. Chloride ions in water will attack many stainless steels. in fact "stainless" is a misnomer - all stainless steels are only corrosion resistant and their resistance is dependent on their working environment and the alloy used. 316 stainless is a general purpose workhorse stainless steel, but it is unsuited to chloride containing liquors. If you seriously want a corrosion-proof shaft, you may want to consider a ceramic and start looking at sol-gel technology to coat a stainless shaft. You will have the strength of the stainless steel, but the corrosion resistance of a ceramic. Sol gel technology is relatively easy to implement and can give excellent performance standards
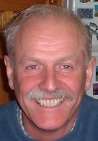
Trevor Crichton
R&D practical scientist
Chesham, Bucks, UK
August 29, 2012
Q. Hi...
I am using an evaporator made of SS 316. Recently several holes have been developed on its surface. after analysis of Evaporator feed we found Chlorides in the range of 10,000 ppm and sulphates in the range of 22,000 ppm. Can you please suggest a method to take care of this?? Is chlorides the only responsible factor in this case??
- Pune, Maharashtra, India
September 7, 2012
A. 316 Stainless steel is not a good choice for the high chlorides in your evaporator concentrate. The sulphates are not a concern. For resistance to chlorides in this concentration range, you will probably need to use a Hastelloy alloy.
Lyle Kirmanconsultant - Cleveland Heights, Ohio
September 10, 2012
A. If your heat source is thru the bottom or the walls, You will build up a scale layer that will act as an insulator and cause a faster degradation of the metal as well as wasted heat.
James Watts- Navarre, Florida
September 10, 2012
Hi...
Thanks for your answer. But as far as it is the question of SS 316 as MOC in evaporator, there are many companies here which have same MOC and their evaporators are working perfectly fine with it.
And about heating source I am not sure. I will get it confirmed and get back to you.
Thanks again.. :)
- Pune, Maharashtra, India
September 12, 2012
Q. Hi
I wish to use Butterfly valves in chlorine solution pipeline service (3500 ppm max.) Material of disc of the valve used is SS316.
I was reading about oitting of SS316.
What are long term and short term affects of chlorine on SS316 valves... and any graphical documentary evidence or photographs are available for the same?
Await for a reply.
Thanks in advance.
- Mumbai, India
December 26, 2012
A. Neil,
Chloride solutions are always rough on stainless. 316 is the best you can have for this short of duplex. Even so, keep an eye on it and repassivate them as needed. This can be done safely and easily with citric acid based products.
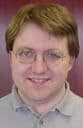
Ray Kremer
Stellar Solutions, Inc.

McHenry, Illinois
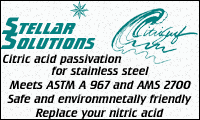
January 22, 2013
Q. We have Rinse tank made out of SS304 material on pre-treatment line. Tank was filled with water for conducting trials. After two months we found many holes on the bottom side of tank especially where Mild Steel stiffener is welded from out side of the tank. See finishing.com/33/54-1.pdf
We checked the water in the tank and found that chlorides as Cl 450 ppm in the water. Corroded area looks like rusty colour.
Can anybody suggest how to repair this tank? We are separately taking measures to reduce the chlorides in the water.
- Pune, Maharashtra, India
April 20, 2013
A. If you weld ordinary SS T304, you will get carbide precipitation in grain boundaries at the weld area, and corrosion resistance will be lost. Use type 304L (low carbon) for all welded parts. In the presence of chlorides, use T316L.
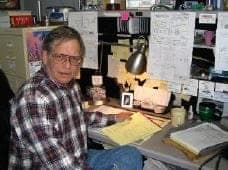
Jeffrey Holmes, CEF
Spartanburg, South Carolina
April 24, 2013
Q. I wish to store a Mild Solution (About 1%) of Sodium Hypochlorite in a S.S. 316 Q Tank.
Will it be safe ?
Is there any chances of corrosive of S.S. 316 Q Metal.
- Ahmedabad, Gujarat, India
May 29, 2013
A. Shirish,
I don't have any hard data that's applicable, but given 316 and the low concentration you plan to use, I think you will be okay for the the most part. However it would not surprise me if there was at least a little bit of corrosion within a year or so.
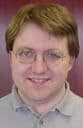
Ray Kremer
Stellar Solutions, Inc.

McHenry, Illinois
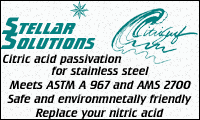
June 10, 2013
Q. Hi everyone,
At one of our projects of water systems, we are facing the problem of reddish spots on the outer surface of SS 316 tank. Whole outer surface is looking red. Next to the SS tank, HCl dosing system is present.
Can anybody suggest how we can clean the outer surface of tank to retain the original finish? Grinding, buffing,polishing is not possible in present condition -- we are looking for some kind of chemical cleaning of outer surface.
Waiting for reply
- Mumbai, Maharashatra, India
September 9, 2013
A. Gopal,
I would suggest that the HCl source in proximity to your stainless is the major contributor to your problem. Yes, there are safe citric acid based chemical treatments you can use to remove the rust and repassivate.
adv.
Let us know if we can help.
And I recommend you move the HCl system, or increase the ventilation around it.
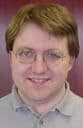
Ray Kremer
Stellar Solutions, Inc.

McHenry, Illinois
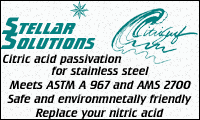
September 24, 2013
Q. Dear All,
We are finding pitting corrosion & crevice corrosion in SS 304 in tanks of solar water heaters against chloride ppm of 1200 at 80 °C.
Which material should be used ss 316L or SS 317L? Please respond.
Regards,
Rajesh Mehta- Ahmedabad,Gujarat, India
July 18, 2015
A. At 1200 ppm Cl and 80 °C, 316L will fail quickly and 317 will fail more slowly, but both will fail.
Use 2025.
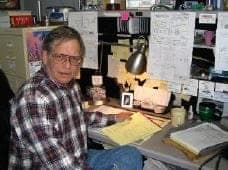
Jeffrey Holmes, CEF
Spartanburg, South Carolina
July 19, 2015
A. Usually, Stainless Steel will be a good corrosion-resistant choice to be used in FGD industry. But under the oxidation reaction, the chloride concentration will increase dramatically so that the passive performance on SS 2205 will be moved to negative side fatally.
Dick Zheng Yu Ao- Shanghai, China
April 20, 2016
Q. Hello all, I am a custodian and have green pitting on many of the "stainless" fixtures in my bathrooms and lockers. I understand this likely means these are copper with a stainless finish. If I am able to remove the corrosion present can I speed up the protective layer healing by applying hydrogen peroxide to encourage oxidating the chromium? Or would a strictly citric acid formula and drying regiment be best? I am in a pool setting and we are required to use a sanitizer with ammonium chloride. Thanks very much for any help.
Tim ramos- Solon, Ohio, USA
February 2, 2017
A. Right, corroding stainless wouldn't normally be green. Though I'm not sure what "copper with a stainless finish" even means.
If it's stainless, citric acid based products should be fine for maintenance treatment to keep things clean and passivated. Accelerating the oxide layer formation with peroxide is hardly ever necessary, and won't make a difference given the constant cleaning with the chloride solution.
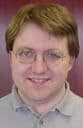
Ray Kremer
Stellar Solutions, Inc.

McHenry, Illinois
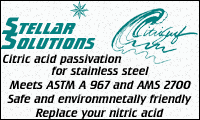
February 9, 2017
? Are you sure it is stainless? The description of green pitting sounds like chrome plated with the use of acid copper to level under a nickel plating.
That is also what I see on worn watercranes.
- Odense, Denmark
April 7, 2017
----
Ed. note: watercranes = plumbing fixtures/faucets?
A. It sounds like the fixtures may be nickel plated brass, which is common for plumbing fixtures. Brass contains copper and will corrode green.
Alex Peterson- Rochester NY
July 29, 2017
Q. Hello Everyone!
We are experiencing pitting corrosion on the Stainless steel 304 liner.
The corrosion environment includes negative ions of SO4, HCO3 and Cl. Working temperature range is 200-300 °C. Could anyone suggest suitable coating or some corrosion protection solution for the problem?
Regards,
Adnan
- Xian, China
October 14, 2017
A. Adnan,
With high chloride exposure, you will want to re-passivate that stainless often. 316 would have been better for you.
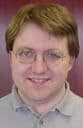
Ray Kremer
Stellar Solutions, Inc.

McHenry, Illinois
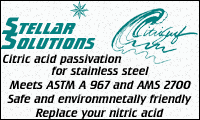
October 17, 2017
Q. Ray Kremer,
Thank you for your suggestion. Actually we are experiencing pitting corrosion in a Coal Gasifier. Is there any idea to prevent further corrosion and extend the life of gasifier. Like some kind of coating, which, may be applied to that large gasifier.
- Xian, China
October 18, 2017
Q. Pharma plant finding white evaporation deposits in clean steam pipework and in autoclave after a cycle. Re-passivated x3 over the last year and white residue returns immediately and doesn't decrease with time.. White residue Contains calcium, fluoride, organic acid material, silicates. Any ideas of a root cause?
Evin Allen- Waterford, Ireland
October 25, 2017
Will type 304 SS buttons rust in a washing machine
Q. Thank you guys for a great board.
My question. Could I use a 304 Stainless Steel for making buttons on clothes? Or will there be oxidation? We try to find a cheaper solution than 316SS and 304 is 20% cheaper. But will it rust when washed in the washing machine with washing powder?
Thanks.
None - Stockholm Sweden
November 30, 2017
A. Hello,
Washing machine powders generally have a 6.5 to 7 almost neutral pH. Whilst regular washing will not lead to an instant rust formation, but it will lead to a gradual dullness on the finish as time goes by.
It is possible that you see a few spots of rust In Indian hard water after a good many washes, but I would assume that it would be OK in Sweden.
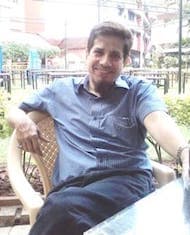
Khozem Vahaanwala
Saify Ind

Bengaluru, India
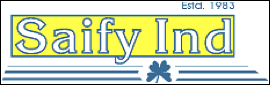
December 14, 2017
Q. How to avoid corrosion in SS316 material in presence of chlorine gas content?
Arun vikeyStudent - Dharmapuri, Tamil Nadu, India
March 16, 2018
A. Hi Arun. Keep the gas dry. Although wet chlorine gas is devastating to most stainless steels, dry chlorine gas is not particularly corrosive. In fact, plain steel can be used. Good luck.
Regards,
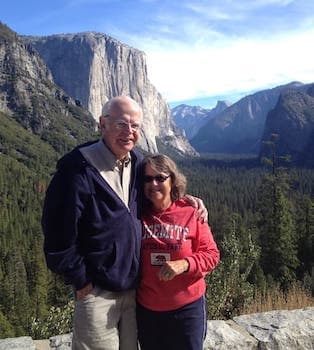
Ted Mooney, P.E. RET
Striving to live Aloha
finishing.com - Pine Beach, New Jersey
April 2018
Q, A, or Comment on THIS thread -or- Start a NEW Thread