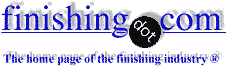
-----
Peeling / poor adhesion of Electroless Nickel Plating on Steel Parts

Q. Hello,
We are doing High-Phos electroless nickel on the parts.
The parts are plated about 60 µm in thickness and heat treated to achieve desired thickness based on customer drawings.
The issues are:
(1)We face high chip-off / peel-off (about 30% yield loss) on the edge of the parts (four corners : cylindrical shaped parts) after going through 2nd grinding process.
(2) We are also facing high pin holes on the parts during plating process as it took 8-10 hours in the plating bath.
(3) We unable to check the part thickness using X-RAY machine for the parts after completing heat treatment. However, we able to measure the part thickness before undergoing heat treatment process. Is it due to the magnetism or the surface of the parts (Hi-P) plated changed structure?
Thanks.
- Kuala Lumpur, Malaysia
May 15, 2022
A. Hi Afiq
It looks that you plate and grind electroless Nickel to adjust part's dimensions.
1. I have some problem to imagine 4 corners for cylindrically shaped part :-), but generally for adhesion improvement you have to look on your preparatory steps: cleaning and acid etch/pickle. Woods Nickel strike may improve adhesion significantly. You did not mention what is the base material of your part - it may be very critical for correct preparatory steps and final adhesion.
2. About pin holes, the best solution is - to contact your chemistry supplier. Pin holes may be related to solution circulation in the bath (to little and too much circulation are both not recommended), also plating rate may affect pit appearance
3. Spec ASTM B733 (electroless Nickel deposition) in Appendixes X3, X4, X5 explains what changes happen to Nickel properties after heat treatment. It is related to the change in micro-structure (Ni+Ni3P). Spec specifically states that changes affect testing by X-Ray and magnetic methods.
Good luck,
- Winnipeg, Canada
June 1, 2022
⇩ Related postings, oldest first ⇩
Q. WE ARE MACHINING SMALL VALVE PARTS 12L14 MATERIAL. THE PARTS ARE TO BE ELECTROLESS NICKEL PLATED.
WE SENT 300 PCS FOR TEST PLATING; THE SEATS SEEM TO BE CHIPPING OR SCRATCHED. THIS WAS DESCRIBED AS PEELING. WHAT CAN BE DONE TO PREVENT THIS AND IS THIS A NORMAL PROBLEM?
WE ARE IN JEOPARDY OF LOSING THE CONTRACT. COULD YOU RESPOND QUICKLY.
THANK YOU,
Robert Allenmachine parts - Linden, Michigan
2004
![]() |
A. Properly applied electroless nickel will not peel. There are several possible things the plater may have done wrong. A likely problem is that he is pickling prior to plating in hydrochloric or sulfuric acid. For leaded steels such as 12L14 he should be pickling in fluoboric acid. ![]() Jeffrey Holmes, CEF Spartanburg, South Carolina 2004 A. The alloy of steel is best prepared using a Wood's or low pH nickel strike. Peeling is the result of improper cleaning and preparation before electroless nickel plating. What thickness did you specify? Deposit thickness in excess of 3 mils may crack when heat treated, but still should not peel or chip if the preplating treatment is correct. ![]() Don Baudrand Consultant - Poulsbo, Washington (Don is co-author of "Plating on Plastics" [on Amazon or AbeBooks affil links] and "Plating ABS Plastics" [on Amazon or eBay or AbeBooks affil links]) 2004 Don: Forget the Wood's Nickel strike on 12L14 (aka leadloy). Exposure to acidic chloride will form an insoluble film of lead chloride, and you'll never get good adhesion. Pickling in fluoboric acid prior to EN is the correct pretreatment for leaded steels. ![]() Jeffrey Holmes, CEF Spartanburg, South Carolina 2004 A. What you have is an adhesion problem. Assuming the plater is doing everything else right, the cause might be the lead present in the alloy. It has to be removed from the surface before plating by a treatment in fluoboric acid. Ask your plater if he is doing it. Guillermo MarrufoMonterrey, NL, Mexico 2004 |
Multiple threads merged: please forgive chronology errors and repetition 🙂
Poor Adhesion of Electroless Nickel on SCM-440 Steel Gear
by G. G. Gawrilov
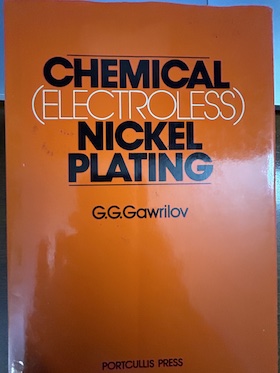
on AbeBooks
or eBay or
Amazon
(affil link)
Q. Dear all,
We manufacture bike/bicycle gear using SCM 440, and we are now trying to apply EN on these steel gears.
The whole process includes: stamping, heat treatment, tumbling deburring, #120 Aluminium Oxide blasting, EN plating (15 microns, 8% Phosphorous, no post-baking).
Finished gears are then assembled along with chains to perform shifter test so that we can know the durability of EN layer under strong friction.
However, EN layer peeled off from substrate so easily and so clean.
I learned that oxides of alloy elements on surface (because of heat treatment) can significantly reduce adhesion of coating layer. And my supplier suggested me to remove oxides and increase roughness by sandblasting.
I'm so confused because the chains are EN plated, yet they stayed the same in test.
I want to know if the sandblasting process can really improve adhesion of EN layer on SCM 440 steel substrate? If so, did I choose wrong blasting media?
Furthermore, is there any alternative process that can improve adhesion of EN layer on steel (such as nickel strike)?
Thanks for your precious comments in advance!
Cheers,
Cliff Chang
Finish Engineer - Taichung, Taiwan
A. I recommend you use a nickel strike. It is possible to achieve good adhesion without but I would not bother trying. I am unfamiliar with your steel but if the surface is difficult to plate because of oxide or uncooperative elements like carbon or chromium blasting with abrasive is probably safer than attempting a chemical etch. One of the reasons for blasting is to give a rough surface. The adhesion is increased because the area to bond to is increased and there is some help from mechanical keying. The surface finish will suffer though.
Nick Clatworthy- Whitstable, Kent, UK
2007
2007
A. Insufficient information. The problem could be residual oxide, contamination from quenching oil or polymer or self-passivation of the cleaned surface prior to plating (likely with a humid atmosphere). Examine the parts after each step to determine the correct treatment.
Longer tumbling or abrasive blasting times may be necessary for oxide removal.
Oil or polymer removal may require wet tumbling in an alkaline detergent solution.
If parts are adequately cleaned but passivation occurs prior to plating, either or both of the following treatments may be used to activate the surface:
1) Anodic cleaning in 25-35 vol% sulfuric acid,
2) Wood's nickel strike.
Afterwards, the parts must be quickly rinsed in DI water and transferred to the EN solution without drying. ASTM B242, 'Standard Guide for Preparation of High-Carbon Steel [> 0.35% C] for Electroplating' and ASTM B656 [withdrawn 2000], 'Standard Guide for Autocatalytic (Electroless) Nickel-Phosphorus Deposition on Metals for Engineering Use (Withdrawn 2000)' give further information on pretreatment.
After EN plating, heat treated SCM 440 (~AISI 4140) should be given a 2-4 hour bake at 180-200 °C for hydrogen embrittlement relief and improved adhesion (Class 3 per ASTM B733, 'Standard Specification for Autocatalytic (Electroless) Nickel-Phosphorus Coatings on Metal'). Baking should be performed within 1 hour (no more than 3 hours) of plating.
Letter 37638 also gives advice on pretreatment and hydrogen embrittlement bake-out.
- Goleta, California

Rest in peace, Ken. Thank you for your hard work which the finishing world, and we at finishing.com, continue to benefit from.
EN peels from plain carbon steel unless we use Fluoboric Acid
January 10, 2014Q. We have been plating with 5.0 µm electroless nickel 1010 Steel for many years. The part is crimped after plating and should not peel. Now for two months we have been experiencing peeling and we have checked everything: Cleaning cycle, activation, Bath pH, Temperature, bath chemistry and nothing helps.
We decided to treat these parts as if they were leaded, similar to 12L14 Steel, so we activated with Fluoboric Acid instead of Sulfuric Acid as done in the past and the problem went away!
The issue is that the Client sent us a chemical analysis of the alloy and the Steel is not Leaded.
What can be causing this adhesion problem?
Can this particular lot of parts (steel) be to blame? Maybe it has Lead or Silicate pockets?
I'm enclosing a picture, part to the right is a new part and part to the left is Electroless Nickel plated and crimped, with flaking. (difficult to see)
Please help so that we can understand the root cause and prevent this from happening again.
Thank you for your help.
Edgar
Plating shop employee - Mexico
A. Hello Edgar,
Is there a chance you can get some 1010 steel parts from another source and run a controlled test using your conventional sulfuric acid activator? If you don't see peeling from the test lot, then the steel you have been using for the past 2 months is suspect. There are other causes for peeling, but it sounds like you have addressed possible causes. One other thing ... Check heated tanks on the line for stray current. A few years ago I was pulling my hair out until I found we had stray current in our Pd activator bath, causing EN peel. Good Luck!
process engineer - Malone, New York
January 14, 2014
Q. Mark, thank you for your answer.
We thought about possible changes on the surface during the machining operations. As far as we know, our client doesn't control the surface temperature/heating of the steel during the machining operation.
So we sent one part to be checked for surface hardness, namely Vickers micro hardness, and the lab reported a hardness of 219.9 HVN -- that translates to Rockwell B hardness of 94.8 average of 10 measurements.
The material spec for the 1010 Alloy states that the raw material received by our client has an average Rockwell Hardness of 48.2
So we think this is the culprit. Any comments about our findings would be greatly appreciated.
- Mexico City, Mexico
January 30, 2014
Hello Edgar,
I'm happy to hear you have most likely pinpointed the cause of the problem. The excess hardness from machining will play a role in peeling after crimping. Nice work!
process engineer - Malone, New York
January 31, 2014
Thick electroless nickel plating peels off SAE1024 steel parts
Q. We are a manufacturing firm. As per our customer's requirement, EN plating to be done on the part. Thickness 25 microns minimum. We are facing a coating peel-off problem, non-uniform deposition, rusting, etc. Please help.
Thanks in advance for reply.
- Hyderabad, India
February 13, 2014
A. Hi cousin Kumar. People do stand ready to try to help, but when absolutely nothing is working (you have peel-off, you have non-uniform deposition, you have rusting, you have "etc."), while you seem to be doing reasonably simple commodity plating (EN on plain carbon steel), and you offer no clues about your substrate condition or your treatment cycle or your previous trouble-shooting efforts and successes, there really are only 3 three things we can suggest and you probably won't like any of them: 1). retain an EN consultant; or 2). try your best to get your supplier to send in a tech service person who will guide you; or 3). read a good book on electroless nickel plating.
I'm not trying to be a smart alec, but a firm basis of plating knowledge is required to bring such a plating process under control. Best of luck.
Regards,
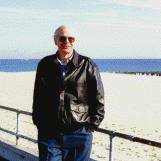
Ted Mooney, P.E.
Striving to live Aloha
finishing.com - Pine Beach, New Jersey
February 2014
Hello Ted,
Excellent answer!
process engineer - Malone, New York
February 13, 2014
February 15, 2014
Q. Dear Ted,
Thanks for your response. Please find below the process our supplier is following. Please let me know your views.
=>SOAK CLEANING in SURTEC 177 for 5-7 minutes, Bath temperature 60-70 °C
=>Acid Pickling in HCl acid for 1-2 Minutes
=>Water Rinsing in two different baths for 30 secs
=>Electroless Nickel Solution ( Atotech/ Growel brand)(pH:4.6-5.2) at 85-91 °C
=>Water Rinsing in two different baths for 30 secs
=>Chrome Passivation for 30 secs
=>Rinsing in Distilled water for 30 secs
=>Drying
- Hyderabad, India
A. Thanks. Okay, I understand the substrate is SAE1024. That is plain low-medium carbon hot rolled steel. Presumably it's been machined into a shape, rather than just being steel plate anymore. If so, please consider the issue raised in the dialog above by Edgar. But it has not been carburized or heat treated? --it's still just machined steel when you plate it?
You mention rusting, but is this in peel-off areas where the steel is exposed, or does it rust right through your 25 micron thick coating? That would indicate extreme porosity. Can you quantify in any way what you mean by non-uniform deposition, so we have a better handle on your reported issues?
Starting with the adage that 90% of all plating problems are pretreatment problems, are you sure that the substrate is free of pitting and that you always have a waterbreak-free surface coming out of the rinses after the acid? That's where I'd start (your soak cleaning temperature strikes me as low for steel parts, and the tech data sheet for Surtec 177 says it's an electrolytic cleaner designed for 20-40 °C operation).
What does the Surtec/Atotech/Growel tech service person have to say?
Regards,
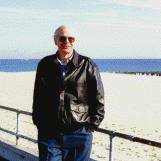
Ted Mooney, P.E.
Striving to live Aloha
finishing.com - Pine Beach, New Jersey
February 2014
April 26, 2014
A. Hi Nagendra ,
Nickel Phosphorous plating peel off from steel substrate :
May I know which phosphorous -- I mean low or medium or high ?
Peel off due to poor adhesion between substrate and plating has three reasons --
1. Improper Cleaning
2. High Nickel concentration in the bath
3. High pH
Water break test - after degreasing for better cleaning
Analyze solution - nickel concentration
pH - by pH paper or pH meter
Three parameters can control easily with in range by above technique.
I hope your problem will be solved.
Regards,
Process Engineer - Tumkur , Karnataka , INDIA
December 25, 2019
Q. Hi To All,
I am facing Electroless Nickel peel-off on CRCA Base Material.
The process we maintain is as Follows,
1)Alkaline Cleaning (60-70 g/l),
2)Hydrochloric Acid (50% V/V),
3)Sulfuric Acid Activation (5-10% V/V) and
4)Electroless Nickel(Mid Phosphorus)
a)Nickel metal= 5-6 g/l
b)pH of Solution= 4.8-5.0
But After Electroless plating We are faced with Nickel Peel Off issue. Please Suggest Any Action/Corrections to Avoid Peel off issue.
- Bangalore, KARNATAKA, INDIA
A. Skip the sulfuric acid step.
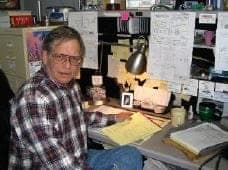
Jeffrey Holmes, CEF
Spartanburg, South Carolina
December 29, 2019
Q. We are having plating failures on a fairly complicated application. Parts are Machined steel basically a cylinder, 1215 (no Pb), OD grind, Plated, Adhesion Bake, OD Grind, Hardening bake, inspect. Plating is 60 microns of High Phos Nickel.
Flakes are occurring on one edge, always the same edge. They are occurring in a very low percentage <1%. We are also seeing edge pullback on the same edge, also <1%. Flakes are not exclusive to parts with the edge pullback.
Multiple studies with no root cause. My question, every discussion with plater on potential issues in the plating process is met with the response that plating is not selective. If it were a plating issue it should be affecting the whole bath. Have others seen flaking and edge pullback issues on a very low percentage of parts and found the root cause to be within the plating process?
Thanks
Automotive - Milwaukee, Wisconsin, USA
February 26, 2020
A. Since it is random on the parts and on specific area I would check the cleaning activation of the part. Also I would check the failed area substrate for any scale or structural difference.
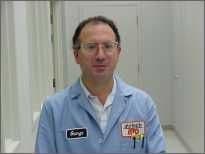
George Shahin
Atotech - Rock Hill, South Carolina
March 5, 2020
Q, A, or Comment on THIS thread -or- Start a NEW Thread