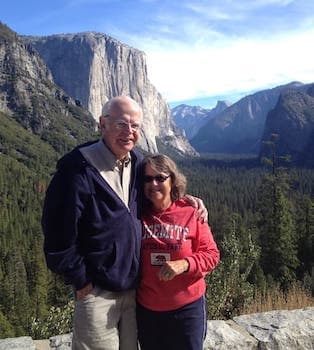
Curated with aloha by
Ted Mooney, P.E. RET
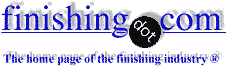
The authoritative public forum
for Metal Finishing 1989-2025
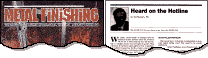
-----
Gold plating issues on beryllium copper
2004
I am currently using an electroless nickel finish on a spring contact (beryllium copper-BeCu) that is soldered onto a printed circuit board (PCB). I can't apply a high enough contact force to satisfy a good reliable electrical contact without sacrificing servicability. I am in the process of evaluating a gold plated finish on this spring contact to improve on contact resistance to the mating piece, without increasing the contact force.
Unfamiliar with gold plated finishes, I referred to a common specification for PCBs using a electroless-nickel/immersion gold process (IPC-4552). The spec seemed to offer everything I needed: high conductivity, high corrosion resistance, excellent solderability.
I received the sample pieces in-house and noticed that the plating peeled off the BeCu substrate if stressed enough. Also, after soldering the spring contact to the PCB, applying a high enough shearing force also peeled off the plating, leaving what looked like the nickel layer attached to the PCB solder pad.
With the original spring contacts plated with only electroless nickel, I haven't seen such a failure mode. But then again, the nickel on this original piece is specified very thick compared to the ENIG spec. Also, the spring contact manufacturer outsourced the ENIG process, whereas the EN process they were able to do in-house.
So with that background, here are my questions.
- Is the ENIG spec referred above proper to use on this spring contact, where a small amount of ductility is required?
- Is there another gold plating spec more appropriate with the requirements I need? (high corrosion resistance, excellent solderability, high conductivity)
- Are there standard practices for surface preparation/activation prior to plating on beryllium copper that I can inquire our manufacturer about?
Thanks!
Hung NguyenEmbedded Controls Engineer - Latham, New York
2004
Most all round general job shops do not know how to get adhesion to beryllium copper.
Be sure the organic soil is removed, dip in 2% Sulfuric Acid,-strike in a plain (non-brightened) cook book copper sulphate ⇦ this on eBay or Amazon [affil links] solution, then go to the electroless nickel and on to gold.
Beryllium forms insoluble salts with the typical cyanide copper strike that most job shops use. Beryllium copper must be electro-striked in a simple copper sulphate solution with no organic brighteners.
And by the way, immersion gold is one molecule thick, not enough for a contact. You need to electroplate at least 50 millionths (0.000 050 inches) up to 0.0001.
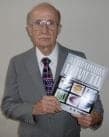
Robert H Probert
Robert H Probert Technical Services

Garner, North Carolina
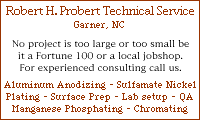
2005
We're currently looking at a similar contact arrangement, with one side being a BeCu spring contact soldered to a PCB, & the other side being a solid brass pin head.
I was told we could specify "low-stress nickel" on the spring to aid ductility. Is this a valid callout?
I was also told that instead of 50u", we should be asking for only
5u" of "hard gold". The same question here: is this a valid callout?
50u" seems to be a fairly standard thickness for electrical contacts, but I've never seen the "hard gold" annotation when the plating's this thick. I've seen FPC parts routinely call out a flash of 5u" of hard gold, but does that work on the type of contacts we're using?
Finally, how does either MIL-G-45204's or ASTM B488 hardness grades correlate to plating durability with regards to number of insertion cycles against the contacts?
Thanks!
E/M design - Boulder, Colorado, USA
Q, A, or Comment on THIS thread -or- Start a NEW Thread