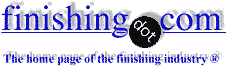
-----
Black zinc plating turns green
A. There is a study on this, based on Black chromate conversion coatings that contain a silver substance (Article mentions AgNO3)
I attach the link at the bottom.
The study shows that the physical reason a green colour begins to appear to the eye is of how the density or spacing of the silver particles are layered on the surface.
A conversion coating that gives off a black colour has the silver particles uniformly spaced apart.
A conversion coating that tends to give off a greenish colour doesn't have the silver particles spaced uniformly.
The study doesn't exactly say what causes this, yet states that certain impurities that remain on the surface may cause corrosion or disruption of the silver particle spacing thus giving off a greenish look.
It recommends experimenting with rinse and dry procedure, which perhaps could disrupt the adhesion of the silver particles. I am unsure if then exposure to sunlight as spoken about in this thread, can more easily accentuate this issue.
Interestingly, this study doesn't delve too much at all on exposure to light being the cause, but doesn't really state a solution other than to be careful with the rinse and dry procedure.
From a plater's perspective, I'd be careful on the entire process from the cleanliness of parts before chromating, to the Black chromate tank conditions (pH, Temperature), immersion procedure/movement and method of rinse and dry. Once I find a set of conditions that give off parts that don't discolour, I'll ensure to keep conditions as close as possible each time.
My Black chromate conversion coating contains silver nitrate. I can say that I have had parts come out of the same batch which eventually did develop a shade of green, and others which did not. Both were exposed to light to some degree.
TDS = technical data sheet
DI = de-ionized
The TDS for my product does stress to use DI water, and does mention that one cause of olive drab appearance is due to a contaminated solution. I may add that I was taught to immerse the parts in a Trivalent Blue chromate solution before going into the Black solution.
I may add, that in shop conditions even under good light, it wasn't as easy to see the green shades and I assumed they blackened perfectly. However, these were more noticeable once they were sent away, simply because more intense light was visible immediately at the other destination and it was easier to spot the slightly greened parts, yet if the same parts were bought back in a more shadowed environment still with mostly good visibility during the day, it was virtually impossible to spot any sign of green at all, and appeared black.
https://www.nmfrc.org/pdf/p1295j.pdf
Plater - Perth, Western Australia
July 13, 2022
A. Thanks Boris!
... and yet another reason plating shops should be brightly lit. In this age of LED lighting it costs very little.
Luck & Regards,
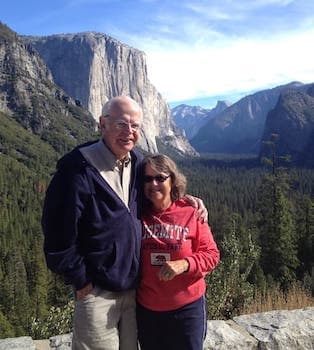
Ted Mooney, P.E. RET
Striving to live Aloha
finishing.com - Pine Beach, New Jersey
⇩ Related postings, oldest first ⇩
Q. Why do black chromated parts turn green? I am looking for opinions or ideas in regard to the greening of black chromate conversion coatings over zinc plating. Has there been any published studies on this problem?
Paul D. Peterson- Rock Hill, South Carolina
1996
1996
A. Hi Paul. I haven't seen any published studies on it, but I haven't been really looking. What I HAVE seen are black chromated parts which, over time, turned chocolate brown, mottled green, and every which color but black. I believe it happens because of the light sensitivity of the silver-based black chromate.
I'm not saying it's the only solution, but one thing I have seen work excellently for some platers is switching the alkaline zinc bath to an alkaline zinc-iron alloy bath and silver-free black chromate. I'm not heavy into the chemistry of it, but I believe it has to do with being able to draw the black color from the iron as opposed to needing silver. If your supplier proposes it, listen to him/her; my experience is that it works!
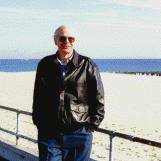
Ted Mooney, P.E.
Striving to live Aloha
finishing.com - Pine Beach, New Jersey
A. Standard Black Chromates over zinc usually contain silver. Silver chromate is deposited onto the zinc as a gel like layer. Silver makes the black color. However it is photo-sensitive, thus turning green when exposed to light. There are some Black Chromates commercially available that are less sensitive. These should be Phosphoric-acid based. Acetic-acid based ones are said to be more sensitive.
When using Zinc-Iron Alloy instead of Zinc as the metal coating, the chromate formulations can be silver-free due to the darker color formed while chromating. Here you can obtain real black color without changing to green even after long exposure to light.
Regards,
Rudolf
- Hong Kong
1996
This general problem has been posted again & again over the years. To minimize search efforts and to offer multiple viewpoints, we combined those previously separate threads onto this page. Please forgive the resultant repetition, or what might look like readers disrespecting previous responses -- the other responses were probably not on the page at the time :-)
Q. Why can black chromate change to a green color?
tan yee heng1998
A. Typically, the Black Chromates that have better salt spray results are Olive Drabs with a silver additive. Without the silver, you get green. You may be using up the silver because of chloride drag-in from a chloride zinc, in which case add more silver or rinse more effectively. Also, tap water can have chlorides which would tie up silver ions.
Take a beaker [beakers on eBay or Amazon [affil links] of your "green" Chromate and add a big dose of the silver additive. Try chromating a part. This will tell you if what I've mentioned is indeed the problem.
Mike McDonald- Jefferson, Wisconsin
1998
A. Black chromates contain simple salts of silver, which are light sensitive. Many shops have switched from zinc plating to zinc-iron in order to be able to use a non light-sensitive black chromate.
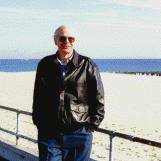
Ted Mooney, P.E.
Striving to live Aloha
finishing.com - Pine Beach, New Jersey
1998
1998
A. You can decrease the tendency of the black chromate to turn green by improving the post rinsing but remember that this coating is sensitive to UV.
As Ted mentioned, switch to zinc-iron. The black chromate of zinc-iron is silver free and not sensitive to light.


Sara Michaeli
Tel-Aviv-Yafo, Israel
Multiple threads merged: please forgive chronology errors and repetition 🙂
Variation in black zinc plating on steel cylinders
Q. I am having variation in black zinc plated steel cylinders. The color varies from black to brown to green. We have chose black zinc for its corrosion resistance and wear characteristics. Do you know what may be causing the variation or an alternative plating that meets our needs?
Joe Stanisha supplier to automotive industry - Hesperia, California, USA
2003
A. Black Zinc I take it is Zinc Plate Passivated in chromate for a black finish. If that is so please check that the chromating solution is made up correctly , the pH matches supplied specs, and the solution is run in when new with some scrap zinc plated parts to age it before use.
The variation in color is due to insufficient and untimely replenishment of the chromate additives. It will help to check the supplier's instructions.
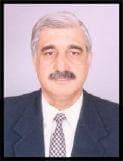
Asif Nurie [deceased]
- New Delhi, India
With deep regret we sadly advise that Asif passed away on Jan 24, 2016
A. I have to disagree with the previous response. Black Zinc Chromate can and usually is photosensitive. Exposure to UV lighting will turn it GREEN. I have experimented with this and have seen the results for myself. Notice how the variation YOU are experiencing relates to light exposure! Bill.
Bill Grayson- Santa Cruz, California
2003
A. The other area to investigate besides the chromate solution that Asif discussed is the Zinc Plate, it must be pure and thick enough. Some Zinc plate (especially from a cyanide bath) may have significant amounts of Iron, Copper, etc. that will interfere with black chromates more than they will with a clear or yellow finish. Black chromates tend to remove more zinc plate than other chromates, so more plating thickness is required initially - .0003" minimum is usually safe. Check the distribution of your color variations, if some areas of the parts are always good, then the solution is probably not to blame (it can't "know" that it should work here, but not there!).
Craig Haseltine- St Charles, Illinois, USA
2003
Multiple threads merged: please forgive chronology errors and repetition 🙂
Q. Hi,
Zinc plating (10-15 micron thickness) with Silver based Black passivation appears black on the first day of production. The same component turns Dark olive green in three to four days time. What is the prime reason for failure? Is there any process improvement to be made to make the process consistent? We use only deionised water, Chrome concentration is also regularly analyzed. As of now we apply NC lacquer. Even then, the color fading remains the same, but the corrosion resistance improves to 400 hrs for NSS test.
M.Kanagavel RajanPlating-process Engineer - Coimbatore, Tamilnadu, India
2003
A. Hi, Rajan. This is a very common problem due to the light sensitivity of the silver salts used in black chromating. Please consider switching to zinc-iron plating which will permit a silver-free black chromate that is color stable. Good luck.
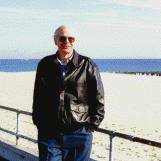
Ted Mooney, P.E.
Striving to live Aloha
finishing.com - Pine Beach, New Jersey
2003
Multiple threads merged: please forgive chronology errors and repetition 🙂
Q. We are manufacturing 7 GA CRS material, then having them plated Black Zinc. The black turns green in a relatively short time. Is the environment or plating process at fault?
Christopher Rousesheetmetal forming - Anaheim, California, USA
2004
A. Hi, Christopher. Black chromates are often silver based and tend toward this problem. Poor plating can accentuate the problem as can excessively bright light. My understanding is that the best answer is to switch the plating to nickel-iron^ZINC-IRON plating because the presence of the iron allows it to be chromated to a stable black color.
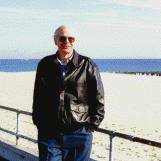
Ted Mooney, P.E.
Striving to live Aloha
finishing.com - Pine Beach, New Jersey
2004
P.S.: I was thinking of zinc-iron and meant to say zinc-iron but didn't recognize my slip until Mr. Nurie's reply below :-(
A. Christopher,
Another cost effective route is Zinc Iron Alloy plating. The iron runs best at 0.8 percent in the allot to produce really wonderful jet black long lasting deposits which accept both Silver and Non Silver black Chromates.
Regards
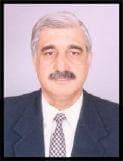
Asif Nurie [deceased]
- New Delhi, India
With deep regret we sadly advise that Asif passed away on Jan 24, 2016
A. I'm a big fan of using sealers for black zinc plating. We started this and have greatly reduced the fading and premature corrosion problems. Also, the pH is critical. I keep it under 2 and check it regularly, with frequent small additions of both components.
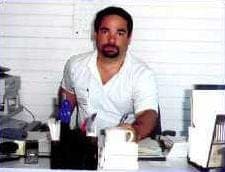
Jim Conner
Mabank, Texas USA
2004
2004
A. Hi,
There are post dips after black chromate which enhance the jet black colour and also the brightness (chromic base); and if you go for zinc iron with a silver and non-silver passivation, iron ratio to zinc is most important factor to obtain best results -- practically if you consider in production level and a sealant coating to minimise this greenish appearance.
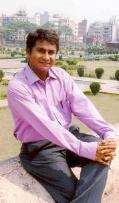
Praveen Kumar
plating process supplier
Mumbai, India
A. The black chromate on zinc-iron is NOT silver based so it does not tend to get greenish with light. These chromates are not even based on hex-chrome but on trivalent chromium. And yes, for a perfect appearance you need a sealer.


Sara Michaeli
Tel-Aviv-Yafo, Israel
2004
Q. Some time after 15 - 30 days later the colour of black passivation on Zinc plating is getting discoloured/changed to greenish yellow. Some greenish salt residue also remains on the surface. Finally the surface is applied by a rust preventative oil. Is it because reaction of Rust preventive oil with passivation? Any reaction of sun light (UV rays) on black passivation?
Nagendra JKPlating shop - Bangalore, Karnataka, India
2004
Black chromate turns khaki green (military green) after two weeks
Q. I am doing hexavalent black passivation on zinc cobalt plating on mild steel press component. The problem starts here: the black colour changes to greenish shade (military green) after fifteen days. Can you help me?
Avinash VidhatePlating shop owner - Nasik, Maharashtra, INDIA
October 16, 2008
October 17, 2008
A. Hi, Avinash. The black chromate that you are using is apparently based on silver, and these are light sensitive. In my limited experience, the best resolution is to switch from zinc cobalt to zinc iron plating because there are chromates that can take advantage of its iron content to build a stable black color without silver.
Regards,
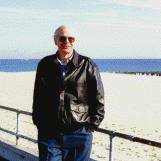
Ted Mooney, P.E.
Striving to live Aloha
finishing.com - Pine Beach, New Jersey
October 18, 2008
Q. Sir,
We are doing hexavalent black passivation on Zinc Cobalt Plating for automobile spare parts and exporting it Europe countries. Our black passivated jobs are changing in colour from black to military green. Customer is rejecting the parts, and we are not finding out the exact reason for it. The discolouration occurs within one month to three months period.
Our bath condition is as follows.
Zinc 42 gm/lit
Chloride 165 gm/lit
Boric 37 gm/lit
Cobalt 1.2 gm/lit
We work within pH 4.8 -5.2
can you please guide us?
employee - Nasik, Maharashtra, INDIA
December 4, 2008
A. Dear Avinash,
Your question was repeated. Please read the answer provided above. That is all you need to resolve your problem.
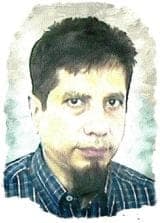
Khozem Vahaanwala
Saify Ind

Bengaluru, Karnataka, India
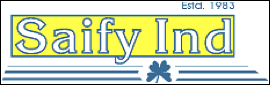
Multiple threads merged: please forgive chronology errors and repetition 🙂
Q. Haven't had this one in a while but like many finishing problems, they have a habit of rearing their ugly head at least once a decade! Customer called saying our black zinc plated parts are turning green in the field - not after they leave our plant, not at the sub-assembly house nor final assembly at the OEM but once out in the field well afterwards. We are using a hexavalent, silver-bearing chromate. Why does this happen and what can be done to eradicate it from recurring? We analyze the silver content regularly and keep the pH within the spec range. Despite all my years (decades!) in zinc plating, in this vane I'm still green!
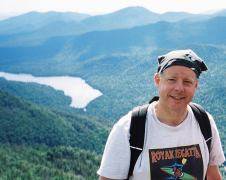
Milt Stevenson, Jr.
Syracuse, New York
February 9, 2010
A. Hi, Milt. It's probably nothing to do with your processing; it happens because silver is light sensitive. I think no matter how fastidious you are, you cannot completely prevent it from happening. If you need black, please consider zinc-iron plating with a black chromate. The iron content allows silver-free dye-free black chromating, and thus a more stable color.
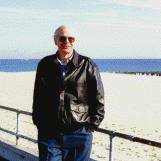
Ted Mooney, P.E.
Striving to live Aloha
finishing.com - Pine Beach, New Jersey
March 17, 2010
A. Following Ted's recommendation, you can use a hex chrome free black on zinc-iron to comply with RoHS


Sara Michaeli
Tel-Aviv-Yafo, Israel
February 21, 2010
Multiple threads merged: please forgive chronology errors and repetition 🙂
Q. We have some machine parts which are Zinc-iron plated and Black passivated, but after a few days these parts are becoming greenish in color. May I know the reason?
Ashish Barve,- PUNE, India
September 16, 2014
September 2014
A. Hi Ashish. It may be dangerous to extrapolate from little information, but as you can see from this thread, black chromate turning green is so strongly associated with the photosensitivity of silver-bearing black chromate that it would be my first suspicion. Can you find out from your supplier if your chromate contains silver and whether they have any suggestions about making the color more stable? Good luck.
Regards,
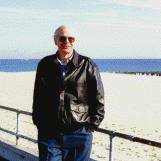
Ted Mooney, P.E.
Striving to live Aloha
finishing.com - Pine Beach, New Jersey

Q, A, or Comment on THIS thread -or- Start a NEW Thread