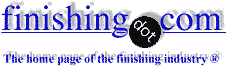
-----
Why can't I get tin plate on mild steel canisters consistently good?
2004
We manufacture chemical oxygen generators that are contained within a drawn mild steel tin plated canister. The tin needs to be 20-30 microns.
The canister manufacturers clean the canisters before sending them for plating and then I believe the tin plating process is pretty standard:
Clean in hot alkaline solution
Rinse in water
Pickled in HCl
Rinse in Water
Tin Plated
Rinse in water displacer.
We have varying results with the quality. The main problems so far have been:
1 Blistering occurring up to 10 days after plating
2 Inconsistent finish, areas that look milky and dull
3 Spangled effect on the surface.
4 Porosity in the tin and rusting when exposed to an adaptation of the salt spray corrosion test
I admit I am no expert in the field, but our platers do not seem to be able to come up with any answers so far. Any ideas? particularly with the blistering problem.
David Gillanchemical manufacturing - Thaxted, Essex, U.K
First of two simultaneous responses -- 2004
You do not say what type of tin plating you are doing. If it is alkaline, the tin will almost certainly be matte; if it is acid, you need to add brighteners to get a bright deposit. Furthermore, I would suggest the following pretreatment:
1) Alkali soak clean; 2) Rinses; 3) Hydrochloric acid dip; 4) Rinses; 5) sulfuric acid dip; 6) Rinses; 7) Tin Plate.
In the conventional manufacture of tinplate, they would flow melt and rapidly quench the tin after application. This was to both give a bright deposit and to fill in the pores. It also forms an intermetallic compound (FeSn2)that both imparts improved corrosion resistance and assists adhesion of the tin to the steel.
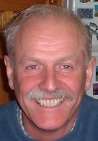
Trevor Crichton
R&D practical scientist
Chesham, Bucks, UK
Second of two simultaneous responses --
From the limited information in your question it would be difficult to offer anything but an educated guess. With blistering, contaminated acid is usually a common culprit. Residue left from the drawing process is also a possibility as soils are actually pushed into the surface and are hard to remove. I can't comment on the process itself since there is no mention of the type of Tin, such as Alkaline, sulphate or MSA but high colloidal Tin will cause poor covering throwing power and an imbalanced bath will cause the surface imperfections. Try some samples with another plater to compare the results and find out the type of process they run.
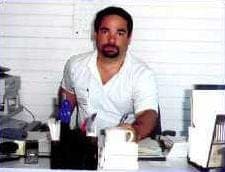
Jim Conner
Mabank, Texas USA
2004
First of three simultaneous responses --
Sounds like the steel isn't clean. Try solvent cleaning a can or two and plating.
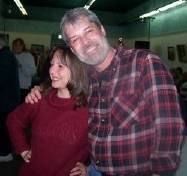
Trent Kaufman
electroplater - Galva, Illinois
2004
Second of three simultaneous responses -- 2004
My first question is what type of tin chemistry are you or your plater using (acid sulphate, alkaline stannate, MSA)?
This would make a difference in how one would approach this problem. Also, how long is the plating time, how much thickness is being applied, etc.
More information. Never can have too much information when trying to troubleshoot!
Gene Packmanprocess supplier - Great Neck, New York
Third of three simultaneous responses -- 2004
David
Normally when you plate acid tin you never can use HCl in pickling because chloride is poison for acid tin solutions.
And it is better to use after the hot alkaline cleaner an electrolytic cleaning working in anodic mode, rinse, sulfuric acid 10% in volume, rinse, acid tin.
Your Hull Cell ⇦ huh? looks good ( 1 amp 5 minutes )
Your acid concentration is up to 11% in volume.
I hope this helps
Gabriel Ramirez Nuñez- Toluca, Mexico
From the limited information in your question it would be difficult to find an exact answer.when there is dull and white areas on the surface of tin plate,it means tin coating is not uniform over the surface.the cause of this defect normally is high or low current density in plating cells. blistering, may be resulted from poor melting process.when alloy tin(FeSn2) layer is low,then adhesion to iron surface will be poor.in other hand quality of tinplate strongly depends on good cleaning of surface before the plating process.if your material is corrosive, it is recommended to use higher coating mass tinplate or lacquered tinplate.
NOROOZI ALItinplate specialist - IRAN
2006
When you carry out tin plating on steel, it is better use sulfuric acid pickling the go for flash Nickel plating and then go for acid tin plating with minimum of 12-12.5 microns and the it is to rinsed thoroughly and can be given a post dip preferably proprietaryy chemicals.
Thanking you
- Bangalore, Karnataka, India
July 24, 2009
Q, A, or Comment on THIS thread -or- Start a NEW Thread