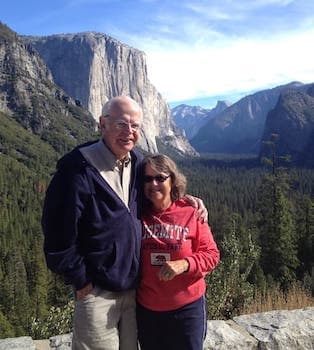
Curated with aloha by
Ted Mooney, P.E. RET
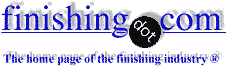
The authoritative public forum
for Metal Finishing 1989-2025
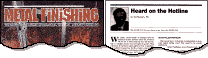
-----
Shrinkage allowed on Zinc Diecast parts
What is the industry standard for shrinkage allowed when plating Zinc Diecast parts? Is it in writing anywhere? What is the average reject rate when chrome plating Zinc Diecast?
Thank You.
Sharon MayberryPlating Shop - Franklin Park, Illinois, USA
2004
I'm confident there is no "industry standard", Sharon, although some buyers are looking for six sigma today. I did see in the "standard terms" of one plating shop that they permitted themselves to lose 2 percent of their customers' parts. I don't know that such a clause survived careful reading by buyers though :-)
I also saw a major consumer tool manufacturer accept ludicrously poor, marginally adherent, chrome plating on aluminum diecast because they felt they desperately needed the parts. They kept talking themselves into the parts being acceptable because the defects weren't on "the significant surface", and continuously reducing what they considered the significant surface so they could keep shipping.
With no intention to lecture you, Sharon, but just in recognition that this is a public forum that future readers will read, take the present situation, whatever it is, as motivation towards the need for continuous improvement.
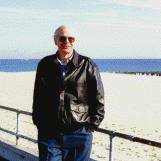
Ted Mooney, P.E.
Striving to live Aloha
finishing.com - Pine Beach, New Jersey
2004
Sharon, most job shop platers, including me, hesitate to commit to such high quality rates when plating most zinc diecastings, due to several factors which you may already be aware of. We have no control over the porosity, composition of metal or surface quality. We usually only have one shot to get it right. With those kinds of issues it's no wonder we cringe. Years ago I ran the plating department of a captive diecaster that made chrome plated knife handles. Our built in scrap rate was 2-5% for all imperfections whether they were plating related or not. When the diecasters and the grinding/polishing departments were running well, we had low rejects. When they had issues, we had issues. Your customer must be educated to the fact that you can only provide as good a part as you receive.
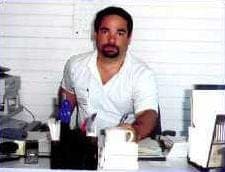
Jim Conner
Anoplex Software

Mabank, Texas USA
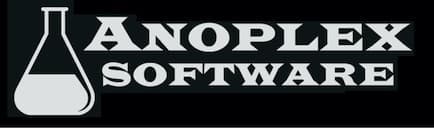
2004
2004
Its nice to have a commercial discussion every once in a while to get your head out of a tank!
The way we handle these issues is that I promise to return 100 % of zinc / aluminium diecast parts to the customer without quantity shortages.
The rejections which vary from 2 to 12 % are returned separately after segregation neatly packed. We expect to get paid the full plating charges since we provide the service of segregation etc. Sometimes the customer builds this into the price and does not pay for rejected parts that are returned to him.
We have had similar experiences as Mr Ted Mooney has mentioned, that on account of expediency, our customers do fish into the rejected packets every once in a while and manage to use these slightly defective parts.
There is no industry standard, but with Hot Chamber Zinc Diecast parts 5% is the norm.
My suggestion would be to accept Zinc-Diecast parts on a "Best Effort" basis.
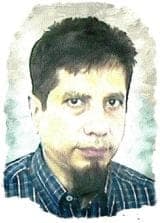
Khozem Vahaanwala
Saify Ind

Bengaluru, Karnataka, India
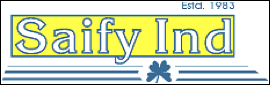

Q, A, or Comment on THIS thread -or- Start a NEW Thread