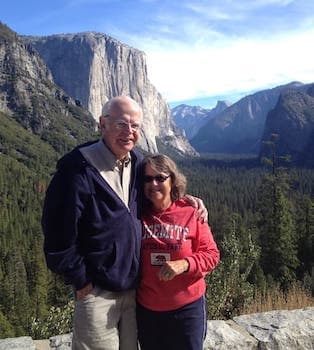
Curated with aloha by
Ted Mooney, P.E. RET
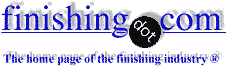
The authoritative public forum
for Metal Finishing 1989-2025
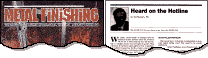
-----
Biocompatibility of 302 SS wire parts - passivation issue?
Q. My company has a part formed from 302 stainless wire. After forming, it is annealed, ground, ultrasonically cleaned, passivated per ASTM 967 and dried before being shipped to us. We have two vendors for these parts and their processes differ slightly, but are made to the same basic specification. This part is a component of a medical device and given its function is subject to biocompatibility testing to meet FDA requirements.
The testing is done by first soaking and agitating our parts for 72 hours in each of four different solutions: 0.9% sodium chloride solution (SC), alcohol in saline solution 1:20 solution (AS), polyethylene glycol (PEG), sesame oil NF (SO). These solutions are then injected into mice.
Much to our surprise, mice injected with SC and AS made from one of our vendors died, in some cases very quickly. Mice injected with solutions from the other vendor, as well as those injected with AS and SC control solutions (i.e. without any parts soaked in them) were fine. This is causing us much consternation and schedule slip, and we need to identify the root cause before we can proceed.
The most obvious difference in the parts is that the first vendor (the toxic parts) uses citric acid passivation (33%) while the other vendor (safe parts) uses nitric acid (25% ± 10%). The results seem counter-intuitive given what I have read about the two methods.
Other differences are in heat treatment (toxic = 250 °C for 6 min, safe = 400 °C for 30 min) and drying (toxic = oven baked at 80 °C for 30 min, safe = spin dried for 15 min) as well as the supplier of the wire stock.
With that preamble, my question is: could this issue arise as a result of the process steps I described? Would, for instance, citric acid passivation inherently leave behind more chromium or nickel that could be agitated off of the parts? Are there other things that we should be looking at? I am still keeping my fingers crossed that the lab screwed up, but I doubt that it will be that easy. Any guidance that could be provided regarding my investigation into this matter would be very much appreciated. I am a product design engineer and not a finishing specialist.
David Maltzmedical device design - San Carlos, California, USA
2004
A. My first suspicion is that, for whatever reason, the parts from the one vendor were poorly rinsed. Obviously, specifications should be in place to prevent that, but it's easy to fix if that's the problem.
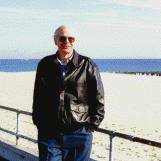
Ted Mooney, P.E.
Striving to live Aloha
finishing.com - Pine Beach, New Jersey
2004
A. Ted's inadequate rinsing is step one. My guess is that the nitric solution is rather new while the citric solution has passivated a substantial amount of 302Se. IE, do a trace metal analyses on the two offending solutions as well as a sample of the citric solution. Me thinks that you will find a culprit. Small amounts of selenium are toxic and there is a fair amount of it in 302Se, thus my scientific WAG.
James Watts- Navarre, Florida
2004
A. You are correct in that this all sounds counter-intuitive. Certainly the passivation method would not give you any difference in the results of your test unless the citric parts were not rinsed well and something was in the bath (e.g. Selenium) that was toxic and did not get rinsed off. Whatever killed the mice has to be pretty toxic to kill them that quickly, so it is going to be more than a little chromium or nickel from the stainless steel.
It is true generally that citric passivation will yield a higher chromium content on the surface of the steel (hence the higher chrome oxide ratio and improved corrosion resistance) than nitric, but this is a very stable chromium oxide layer that would be affected by your test solutions the same for either the nitric or citric.
I would look at what impurities are in the bath or some other difference in the process. It is a far stretch to say there was something in the drying chamber that deposited a toxic material on the screen. You can only repeat tests with all conditions being the same except one to determine what it is. You have too many differences between the two tests to assume any one of these as the cause.
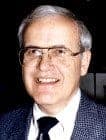

Lee Kremer
Stellar Solutions, Inc.

McHenry, Illinois
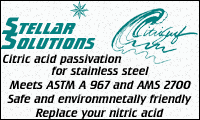
2004
Q. New information: We did a metals analysis of the two parts and found that the parts that failed had a high concentration of nickel -- 10000X the parts that passed. It turns out that the supplier is using a nickel-coated wire fabricated in Japan. I gather that they do mostly electronic components, not medical devices.
We have not yet concluded that this is the source of mortality, but it is looking like it might be.
Apparently, the nickel coating is allowable in the ASTM spec -- is there a better spec to use other than the ASTM spec, disallowing nickel coatings?
Also, what type of nickel is typically used to coat stainless wire? I have heard that nickel sulfamate might be a candidate, but are there others we should be looking for as well?
Lastly, are there any reliable ways to remove this free nickel if it is in fact the culprit?
David Maltz- San Carlos, California, USA
2004
A. Try using a soap-coated wire instead of a nickel coated wire.
Kevin Kirchner- Irvine, California
2007
Q. Kevin (or anybody else),
Could you elaborate on the "soap-coated"?
Our spring manufacturer suggested we use such a wire to ease his own process. We currently use uncoated 302.
Following the manufacturing and heat setting we passivate the springs.
What could you say regarding passivation of the soap-coated wire? Should it be removed beforehand? How?
- Caesarea, Israel
March 4, 2013
A. If it's a normal type of soap, it should come off by itself in the passivation acid bath, though precleaning never hurts anything.
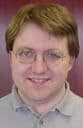
Ray Kremer
Stellar Solutions, Inc.

McHenry, Illinois
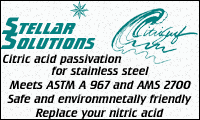
March 11, 2013

this text gets replaced with bannerText
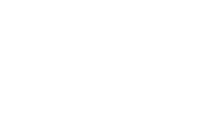
Q, A, or Comment on THIS thread -or- Start a NEW Thread