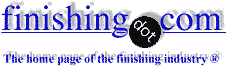
-----
Overetch / spangle effect
2004
Q. Dear Sirs / Madams
Recently we have rejected few lots material due to overetch defects. We did know whether we used correct term for describing this defect or may other term more relevant such as spangle effect. The defective parts look shine with coarse grain structure appeared on the whole surface of anodized aluminum. Look at Ted Short anodizing "Defects & Identification" reference book, when zinc content in 6063 alloy or in etching solution (NaOH) exceeded 0.03%, this defects will appeared. We have analysed the defective parts alloy composition, zinc content only 0.026 % which is within the range as suggested by Mr. Ted Short. We also read one article written by a Chinese Metallurgist, if
Zn content Etch temp appearance 0.016% >55°C 25% defect 0.026% >55°C 50% chance 0.036% >55°C nearly 100%Question: 1. Zinc can cause this defects? 2. What is the optimum Zn level? 3. Others than Zn, what else impurities can cause this defect? For information: We running our etching process as the following parameters: 1. F - [NaOH] 50 - 55 g/l 2. [Al] 25 - 30 g/l 3. Temperature : 55 - 58 °C 4. Etching time : 8 - 10 minutes (caustic soda ⇦liquid caustic soda in bulk on Amazon [affil link] Recovery System)
Best regards,
Eddy Lim Klang Malaysia
LIM HK- Klang, Selangor, Malaysia
A. Eddy,
I have experienced many similar situations on aluminum 6061-T6 alloy type 2 anodizing. From all the questions asked it seemed to point to the actual coarse grain structure (peripheral coarse grain) of the material that is formed during the extrusion process, rather than any impurities in the material itself. basically, it is process related where the extrusion billet cools at different rates which create regions of dissimilar composition and consistency, especially towards the outside of the billet (but not restricted to). This has been my experience. There are ways to minimise this through close control of the actual extrusion process itself - maybe you can discuss this with your suppliers?
Michael GeorgiadisRDI - Kzn, South Africa
2004
A. Hi Eddy,
My experience to control Zn below 0.01% and etch time 5 minutes is enough.
Please try,
- Surabaya Indonesia
July 20, 2011
Q. Will plate (rolled) aluminum 6061 be less prone to spangling when anodized over extruded due to a possible fine grain structure?
Steven Kaishian- Wauwatosa, Wisconsin, USA
October 7, 2013
Q, A, or Comment on THIS thread -or- Start a NEW Thread