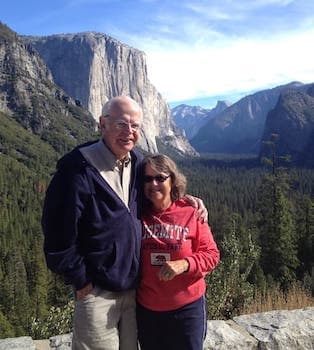
Curated with aloha by
Ted Mooney, P.E. RET
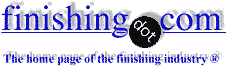
The authoritative public forum
for Metal Finishing 1989-2025
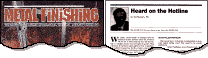
-----
Electrical contact resistance with electroless nickel plating
Q. WE USE ELECTROLESS NICKEL PLATING FOR SHIELDING OUR RJ45 PLUGS AND JACKS. THE BASE MATERIAL IS BRASS 0.2 mm-0.3 mm THICK AND PLATING IS PER MIL-C-26074 [⇦ this spec on DLA] CLASS 1 at 3-5 microns.
WHEN I CHECK THE ELECTRICAL CONTACT RESISTANCE I FOUND OUT I HAVE LARGER RESISTANCE THAN EXPECTED (2 TO 10 TIMES LARGER).
IF I GENTLY BRUSH THE NICKEL SURFACE WITH A VERY sandpaper RESULTS ARE GOOD. IT SEEMS LIKE THE NICKEL HAS SOME KIND OF OXIDATION.
WHAT CAN BE DONE TO IMPROVE THE COATING? DO WE HAVE A PROBLEM IN THE COATING PROCESS? I KNOW OTHERS USE THE SAME COATING AND DO NOT FACE THIS PROBLEM.
THANKS,
Pini Shifris- TEL-AVIV, ISRAEL
2004
A. Hi Pini. Welcome to the world of non-precious metals. All metals, except a few precious metals like gold, tarnish like this and then offer higher resistance. If you need very low resistance contacts for digital signals, that's what gold, palladium, and rhodium are for.
Electroless nickel is great for battery charging contacts of every variety and is widely used for that, but not for very low resistance contacts. A proprietary chromate dip may forestall the tarnishing a bit and for a while though, and that may be what others who are enjoying greater success do.
If you tell us what contact resistance you get, at what voltage and amperage, and what phosphorous level you have or need, a reader with real experience in this might be able to tell us whether you can expect better with improvements to your process. Good luck.
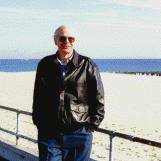
Ted Mooney, P.E.
Striving to live Aloha
finishing.com - Pine Beach, New Jersey
A. In order to prevent the tarnishing of the nickel your plater should use a chromate post dip. An electrochemical chromate is even better


Sara Michaeli
Tel-Aviv-Yafo, Israel
2004
Electroless vs Electrolytic Nickel Plating Contact Resistance
Q. Hello all,
I have been digging through the literature in a failing attempt to distinguish between the contact resistance of electrolytic vs electroless nickel plating on copper. My inquiry to you is this: do you have a link to literature with quantified data, or have you yourself run an experiment to measure contact resistance?
The best I've seen thus far is electroless plating of Si and other semiconductors, and I've drawn an analogous conclusion that the higher resistivity of electroless Ni corresponds to a higher contact resistance...can anyone confirm?
Thanks!
Materials engineer - Detroit, Michigan, United States
September 28, 2016
A. Hi William. There is a chart and discussion of electrical resistivity in Mallory & Hajdu.
Contact resistance would depend on the level of tarnish and surface dirts & oils, which in turn are a function of age and environmental conditions -- so I think you're far less likely to find such info in the literature. Still, there is an organization which tracks and abstracts all (or at least most) of the literature from the plating field, and you could contact them about their CDs, on-line access, or customized searches. I suggest that you try Anselm Kuhn of Finishing Publications/MFIS in the UK. Good luck.
Regards,
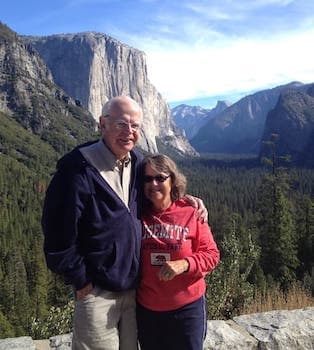
Ted Mooney, P.E. RET
Striving to live Aloha
finishing.com - Pine Beach, New Jersey
September 2016
A. Hi William,
Assume both are fresh deposit without tarnish, corrosion, oil/dirt, etc, electroless Ni contact resistance used to be higher than electrolytic (pure) Ni due to phosphorus containing (or boron containing, etc).
Low, mid or high phosphorus electroless Ni results in different contact resistance.
Regards,
David
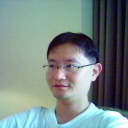
David Shiu
- Singapore
November 4, 2016
Q, A, or Comment on THIS thread -or- Start a NEW Thread