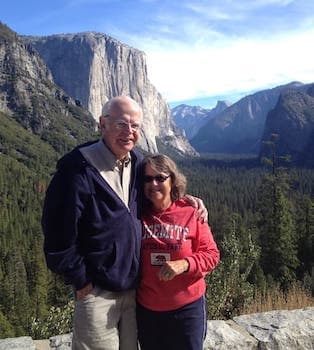
Curated with aloha by
Ted Mooney, P.E. RET
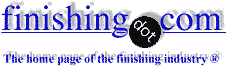
The authoritative public forum
for Metal Finishing 1989-2025
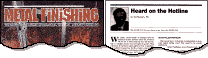
-----
Acid zinc plating Anodes Q&A
adv.: Supplier of Copper Anodes, Nickel Anodes, Bismuth Metal, & Other Metal Products for Industry & The Arts
Q. Ted-
I've also been wondering about basket anode surface area calculations. In your reply you state that you use the formula WxLxD to arrive at surface area. This, of course is not the surface area of the basket, it is the volume. Do you use this number, or do you use the outside surface area of the rectangular prism (i.e 2x (WxD) + 2x(WxL) + 2x(DxL) ?)
retired - Adelaide, South Australia
November 5, 2024
Ed. note: Hi Paul. You are clearly correct. I had meant to say "the surface area based on the L, W, and D", rather than "L x W x D". I've now edited that reply to try to make it less misleading :-)
⇩ Related postings, oldest first ⇩
Q. Hi there,
Our acid zinc plating bath got like 3 months running; everything is okay but a question surged because we noticed that our zinc anodes change their surface aspect, turning into a blackish color.
So we are wondering why is it happening and does it affect directly to our plating parts?
Thanks
- Sinaloa, Mexico
May 23, 2022
A. Hi Jorge. Not necessarily because of the color, but as general QA assurance you should probably (at least once) check whether your anodes have cadmium in them unless you have enormous confidence in your anode supplier.
Thread 56987 is about that subject.
Luck & Regards,
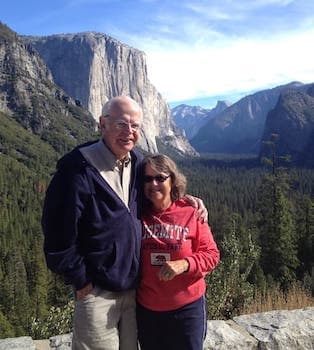
Ted Mooney, P.E. RET
Striving to live Aloha
finishing.com - Pine Beach, New Jersey
⇩ Related postings, oldest first ⇩
I have an ammonium chloride/Potassium chloride zinc plating bath and my metal is continuously climbing up. I am keeping my chlorides below 14 O/G and pH is about 6.0 Now, I have some options of either putting some insoluble anodes in or pulling out some existing anodes (without disturbing anode to cathode ratio).
I would like to see some debate at this wonderful platform about following things as different experts are giving me different advise.
Q1. Is pulling out zinc anode baskets is a good option. An expert has taught us not to do so as it may increase more metal as less anodes get more current density and will eventually throw more metal in the bath? (wait a minute, does not less anode area means less metal in the bath)
Q2. Which insoluble anodes are good for the above kind of bath.
Q3. Hey, interesting question: What is the best way of calculating surface area of an anode filled with zinc balls. Is this just one rectangular side area of the basket or is it the sum of one rectangular side and total area of all the individual zinc balls (and I hope in each case we are calculating one rectangular side of the basket only as the other side is facing the tank wall)
Let us do a little debate here. I need some help. I know the best way is to run my own tests and find out, but you may have some prior experience which might benefit us. Lets share our experiments here.
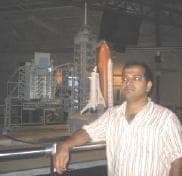
Hemant Kumar
- Florida, USA
2004
Hi, Hemant.
A3. Imagine a baseball and a sponge of the same diameter. How does the sponge's "surface area" compare to the surface area of the baseball? If you tried to determine the answer by counting how many ping pong balls you can glue to the surface of each, the surface area would be exactly the same. If you tried gluing bb's to them, you could probably glue maybe twice as many to the sponge because some bb's fall into the holes in the sponge. You could perhaps glue 10x more grains of sand to a sponge than to a baseball, and say 100x more grains of flower. So is the surface area of the sponge the same as a baseball or 100 times greater or somewhere in between?
For the safe capacity of a room you'd probably consider the size and number of doorways that lead into it because everybody has to pass through those doors quickly in the event of a fire. Likewise the current to an anode has to pass through the "door" that is the L x W x D surface area of the anode basket. ^ surface area of the basket based on its L, W, and D. So that's what I would call the surface area of the anode.
Although less current flows to the back of a basket, personally I use the surface area of the whole basket; consider that if you were using stick anodes you would calculate based on the surface area of the whole stick anode; and certainly, the surface area of basketed anodes is not less than the surface area of stick anodes of the same size as the basket.
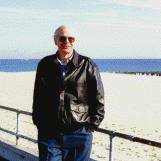
Ted Mooney, P.E.
Striving to live Aloha
finishing.com - Pine Beach, New Jersey
Ted Mooney
Wonderful, and that's the way I always thought. Previously I was calculating my anode to cathode ratio based on your logic. And everything was 2:1 (anode to cathode).
But now I have like 250 square feet at cathode whereas my total Anode basket area will be 25 square feet only. So I am down to 1:10 instead of 2:1 (anode:Cathode).
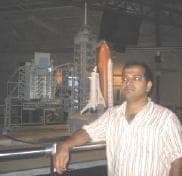
Hemant Kumar
- Florida, USA
A. Prior to changing to alkaline zinc solutions about 7/8 years ago we operated acid zinc solutions and found that increasing the total chloride concentration to about 200-210 grams per liter (about 34 oz/US gall I believe) had the effect of preventing the zinc content rising. This was based on advice from a rep who had seen this practice work in other plants. We were skeptical but followed the advice anyway. The theory behind it being that the solution reaches a saturation point where it won't accept any more zinc into solution. That may or may not be the reason it works, but once we tried it we ran for several years without any problems with rising zinc concentrations. I would certainly recommend increasing the chloride concentration and would advise against putting insoluble anodes into the solution.
Dougie Lightfoot- Fife, Scotland
2004
Wow, keep one constituent so high that other does not have chance to get in. To do this, I might need lots of lab work to make sure the process is robust. But wondering, would it not affect any after plating characteristics, any chromate, peeling off etc. All these parts go to bake and I hope there is no problem with Chloride level so high. Also what other platers think about pulling out anodes options. Any experiences to share!
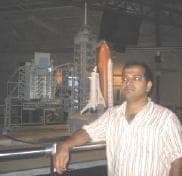
Hemant Kumar
- Florida, USA
A. Hemant,
Technically Mr.Dougie's opinion has a valued point as long it's possible to maintain the metal to chloride concentration in 1:4.4 ratio. A few brighteners have the property of oiling out when the chloride content goes above 150 g/l.Have to watch that! And moreover reasonably concentrated baths are high efficiency baths.
I also have a similar predicament and I am trying to avoid removing baskets or diluting the solution, either its cumbersome or wasteful.
One article says that use of magnesium or aluminium alloy will prevent zinc build up but till now I am aware of anyone using those anodes in industry.
Venkat Raja- Kitchener, Ontario, Canada
Buildup of zinc concentration in acid zinc plating has been a perennial issue ever since its invention. If magnesium or aluminum anodes can prevent it, I for one would like to hear more. Thanks for bringing it up!
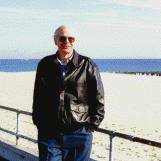
Ted Mooney, P.E.
Striving to live Aloha
finishing.com - Pine Beach, New Jersey
A. We didn't bake after plating but I wouldn't think the deposit characteristics would alter so much that it would be an issue.We did occasionally powdercoat some plated components and these were processed with no problems. The pH needed to be maintained around 5.5 to prevent roughness but that may have been more to do with the additive chemistry than the chloride concentration.
Dougie Lightfoot- Fife, Scotland
A. Subsequently you can try to reduce the anode efficiency with a combination of soluble and insoluble anodes. This will help you maintain a balance of metal getting into the solution.
The insoluble anode can be ferrite or RuO2 coated anodes or other material having a low Oxygen or Chlorine over potential. By using this you will enhance other reactions in the system and subsequently reduce the Zinc dissolution. But take a caution to make sure your brighteners or organics in the system doesn't break down due to oxidation (evolution of chlorine and oxygen).
Good luck...
Karthik Thambiduraielectronic components - Norwood, Massachusetts
Q, A, or Comment on THIS thread -or- Start a NEW Thread