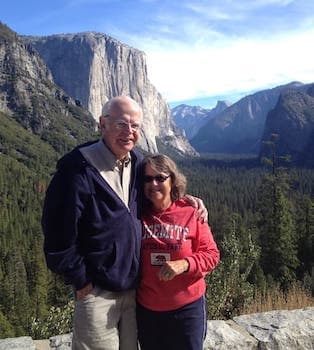
Curated with aloha by
Ted Mooney, P.E. RET
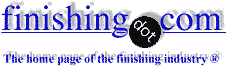
The authoritative public forum
for Metal Finishing 1989-2025
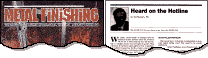
-----
Surface prep for 2024-T3 human powered vehicle
Hi everyone,
I am a hobbyist working on a recumbent bicycle made of riveted/bonded aluminum -- mostly 2024-T3 .025" Alclad sheet with a few 6061-T6 components. The techniques used are all standard aircraft methods -- formed sheetmetal components are match drilled and prepped; pa room temperature cure 2-part epoxy is applied; and the components are assembled using rivets. My immediate intention is to build one for my own use and see how it goes.
What do you folks recommend for a safely applicable, environmentally friendly surface treatment protocol? My goal is corrosion protection for a vehicle lifetime <= 10 years and, if possible, adhesion promotion as a bonus.
The experimental aircraft community spans a wide range, from those who don't worry about priming at all (usually for 6061-T6) to those who conscientiously chromate conversion coat and zinc chromate prime each and every part. However, my situation is different from the experimental aircraft for a variety of reasons -- mainly related to the short intended lifetime of the entire vehicle and its low capital cost.
Thank you very much for any and all help. Peace,
Ihab AwadHobbyist - Palo Alto, CA, U.S.A.
2004
If you do not like the idea of chromate, consider type II sulfuric anodizing. If that is not an option, consider a phosphate coating. a good powder coat or a great wet paint should follow any of the above.
James Watts- Navarre, Florida
2004
Q, A, or Comment on THIS thread -or- Start a NEW Thread