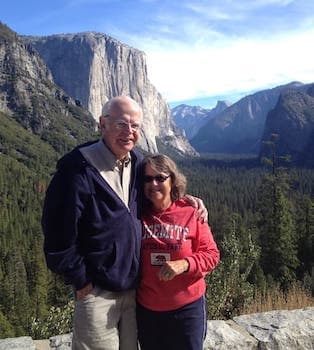
Curated with aloha by
Ted Mooney, P.E. RET
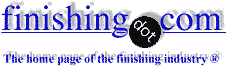
The authoritative public forum
for Metal Finishing 1989-2025
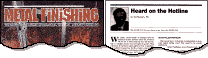
-----
Problems with EN adherence on 5083 aluminium
2004
We plate a number of aluminium components, 2-4µm Electroless Nickel underplate, followed by 8µm Silver. All components are subjected to a 160 °C (320 °F) 1-hour adhesion test bake.
Generally we do not have a lot of problems with our process, but recently items from a particular manufacturer are causing us on end of distress, with failure rates approaching 50%. This has happened with two consecutive batches of product from this manufacturer, but parts from all other suppliers we can process as normal. The material is 5083 alloy.
Our examination of the failures indicates the adhesion problem is between the EN and the base aluminium, the EN/Silver interface is fine.
This is our usual process:
1. Soak clean 70 °C (160 °F)2. Rinse x2
3. Acid Etch (proprietary, but contains sulfuric and ammonium bifluoride)
4. Rinse
5. Desmut 33% nitric acid
6. Rinse x2
7. Zincate
8. Rinse x2
9. Zincate
10. Rinse x2
11. Electroless Nickel Plate
12. Rinse x2
13. Silver Strike
14. Silver Plate
So far we have tried adding a very hot cleaner (90 °C/195 °F) before the usual soak clean, this is made up with a product that is designed to withstand that temperature (our usual cleaner is recommended for <= 71 ° C/160 °F).
We have also tried adding an alkaline etch prior to the acid etch, with varying etch times between 1-4 minutes and temperatures varying between 32-50 °C (90-120 °F).
Finally we tested with an alkaline electroless nickel prior to the main EN bath - this actually made the problem worse rather than better.
We have also tried combinations of the above (e.g. all three, just the alkaline etch and alkaline EN with no extra cleaner, extra cleaner and alkaline etch without the alkaline EN) with no positive results.
I am at a loss what to do about this problem, if anyone could help me I would be most delighted.
John ReidPlating Shop - Brisbane, Queensland, Australia
![]() |
Try reversing steps 5 and 7. You should zincate up to 2 min., rinse x2, strip zincate with up to 50% nitric, rinse x2, zincate 15-30 secs., rinse x2, E/N plate. Hope this helps. Paul Szymanowski- Erie, Pennsylvania I guess you just forgot to list it. Or are you not stripping the first zincate before you do the second? It is a MUST. Guillermo MarrufoMonterrey, NL, Mexico It may be a typo, but you did not indicate a strip step between the two zincate operations. My guess is that your problem lies in the zincate operation as there is no good visual QC check. Too little or too much can cause adhesion failure. I have used the alkaline EN strike with superb adhesion. Other than the ammonia ⇦ this on eBay or Amazon [affil links] smell and the propensity to self destruct when not used daily, I think that it is great. I would politely and strongly insist that the vendor of the zincate operation send in an extremely well qualified tech service rep. You might indicate that if you can not solve this problem rapidly that it may drive you out of business.That will normally get their attention. Have you considered trying a test tank of another vendors zincate. If you can stand the trace of cyanide, the ternary zincate MIGHT offer better results. There is a remote possibility that you are over-etching the part. Another possibility is that you are using a silicate containing soak cleaner, probably hot, and it is drying on the surface. It takes mechanical means to get that off. James Watts- Navarre, Florida
After all the extra cleaning, it seems that the problem is the zincate. If indeed the separation is under the electroless nickel ![]() Don Baudrand Consultant - Poulsbo, Washington (Don is co-author of "Plating on Plastics" [on Amazon or AbeBooks affil links] and "Plating ABS Plastics" [on Amazon or eBay or AbeBooks affil links]) Dear Reid, I have two doubt in mind first are you using non silicated cleaner for aluminium or try one piece with 5% sodium hydroxide (short immersion it should not etch aluminium). Second from process no. 7 means zincating to second zincate you should first remove first zincating in nitric (separate not what you using for desmut) and then go for second zincate or same process you can repeat thrice also . Hope above helps Regards Qutub Saify- Ajman, UAE |
![]() |
Why are you etching the parts? How many metal turnovers on the plating Bath? Todd Osmolski- Charlotte, North Carolina, USA Apologies to all readers, I did indeed forget to mention the zincate strip between the first and second zincates. First zincate is for one minute, followed by double rinse, strip in 33% nitric acid for 15-30 seconds, double rinse, second zincate 15 seconds. The first cleaner I am unsure as to whether or not it is silicated. The second cleaner I know for sure is not silicated, but I guess that would not make any difference if the first one is, seeing as silicate must be removed mechanically? Thanks everyone for your help so far. John Reid- Brisbane, Queensland, Australia |
2004
First be sure the zincate is a dilute formulation and stay in 30 to 45 seconds. Then insert:
10a 4 oz/gal sodium carbonate
10b Rinse
10c Alkaline Electroless nickel, 5 minutes
10d Rinse
11. Process to acid electroless nickel as stated.
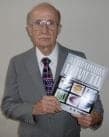
Robert H Probert
Robert H Probert Technical Services

Garner, North Carolina
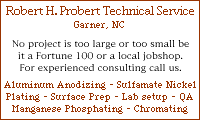
A. Mr Reid
Hi, have you tried nickel strike after alkaline electroless nickel and prior to acidic electroless nickel .
Regards
Qutub Saify- Ajman, UAE
2004
A. Since you are plating a 5000 series Al alloy that contains Mg. I would use a pretreatment cycle with no fluoride. Fluoride containing solutions will form MgF2 which is difficult to remove off the surface.
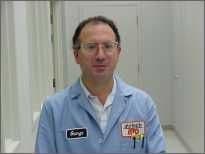
George Shahin
Atotech - Rock Hill, South Carolina
2004
A. My experience of double-zincating Al, EN then AgCN had 2 problem areas, cleaner overuse and zincate age/degradation. Cleaner required a visual control. I implemented an elemental analysis (AA or ICP) of the zincate deposit to monitor changes in the composition of the deposit.
Don Wright- Portland, Oregon, USA
October 17, 2014

Q, A, or Comment on THIS thread -or- Start a NEW Thread