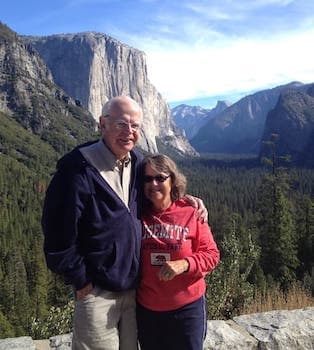
Curated with aloha by
Ted Mooney, P.E. RET
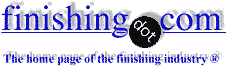
The authoritative public forum
for Metal Finishing 1989-2025
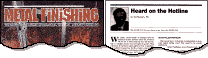
-----
Quality of rinse water and phosphate coating weight for powder coating
2004
We are experiencing corrosion problem on powder coated parts which are exported. Powder coating is carried out after 7 tank hot phosphating. The coating weight being given is 4.3g.sq.m. While trying to solve the problem we need the following clarifications:
1.The quality of water/or the specification of the rinse water.
2.The ideal coating weight to be maintained.
Kindly help us with the clarifications sought at your earliest convenience.
R.V.Ramanee- Bangalore, Karnataka, India
If the technical leaflet of the phosphating chemistry does not specify these details, you need a more competent chemistry supplier first.
Secondly there is no such thing as a 7 tank process!
7 tanks in a row do not suffice/constitute a decent phosphating processs, they are ok to swear by, but you will not ensure proper phosphating by dipping parts through in 7 cocktails.
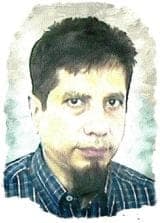
Khozem Vahaanwala
Saify Ind

Bengaluru, Karnataka, India
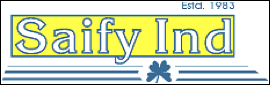
2004
If you are using 7 tank hot process,It means you are using di-cationic dip phosphating.Use tricationic phosphating ,It has better advantage . I want to ask you one thing that what is the geometry of your components.Are you dealing with box type of components?
Manish Dhyani- New Delhi
2004
You did not state the type of phosphating you were doing, iron or zinc. With a seven stage process the superior zinc phosphate system can be used.
Stage one cleaner, make sure all the mill oil and soils are removed. stage two rinse direct from your water source, as long as it is reasonably clean. The most important thing here is getting all the cleaner off by keeping the cleaner contamination of the rinse water low (overflowing), sufficient heat and volume to get good rinsing and enough pressure to get good impingement 1.75 kg/cm^2. Zinc phosphate forms by precipitation on pH change which can result from cleaner residue. Stage three phosphate application ideally 2-4 g/M^2. Stage four rinse with reasonably clean water to remove reaction salts. Again you need to keep the contamination level low. Salts Left on will cause build up of osmotic pressure under the paint film causing blistering in the field over time. Stage five, chrome rinse sealer or some other non-chrome substitute. Stage six DI water rinse with a conductivity of 10 mho's or less. Since you have seven stages a second cleaner stage would be most effective with a titanium phosphate application halo on the last set of sprays.
Use statistical process control (individuals moving range) for controlling all the significant characteristics and make sure plugged sprays are promptly fixed. Canister bag filters on the rinses will help immensely.
Ronald ZeemanCoil Coating - Brampton, ON, Canada
2004
Q, A, or Comment on THIS thread -or- Start a NEW Thread