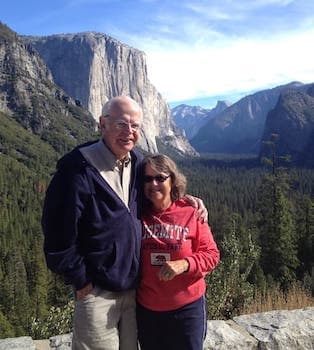
Curated with aloha by
Ted Mooney, P.E. RET
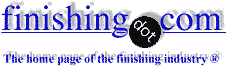
The authoritative public forum
for Metal Finishing 1989-2025
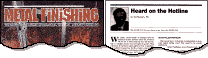
-----
Golf head nickel chrome plating corrosion
We are trouble shooting some inconsistent nickel chrome plating corrosion results on a 1025 low carbon steel golf club head. The interior deep sharp corners get inconsistent plating coverage, and the 48 hour salt spray tests are varying.
Are there any recommendations for pre or post plating operations which may improve?
Ever passivate a plated part in case there is some residual free iron?
It is a Trivalent chrome process.
Thanks
Mike PetersManufacturer - Vista, California, USA
2004
You should take a look at racking to see if a different racking method will produce better plate distribution in the low current density corners. It may be necessary to increase overall nickel thickness in order to get a thick enough nickel deposit in the low CD ares to pass salt spray. If you are using single layer bright nickel, a change to duplex nickel will improve salt spray performance. Any of the major suppliers of nickel plating processes can help you with that.
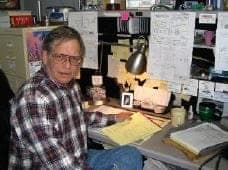
Jeffrey Holmes, CEF
Spartanburg, South Carolina
2004
I'm surprised you consider trivalent durable enough for golf clubs. I've been turning this type of work away.
Am I missing something?
Steve Clarkpolishing and plating - Belfast, Maine
2004
I have over 25 years of experience manufacturing golf clubs and additional experience working with different Companies plating golf clubs in California.
The problem described is a common problem in plating golf clubs. The best feasable solution is to plate duplex nickel. The corrigation lines and stamps are the typical areas of corrosion failures. This is due to the extreme LCD areas and geometry involved. Rack positioning will not resolve the problem. Conforming auxilliary anodes might help but will be very costly.
You should be able to increase the salt hours by 2 to 3 times by using duplex nickel.
J. Bruce Anderson- McAllen, Texas
2004
Q, A, or Comment on THIS thread -or- Start a NEW Thread