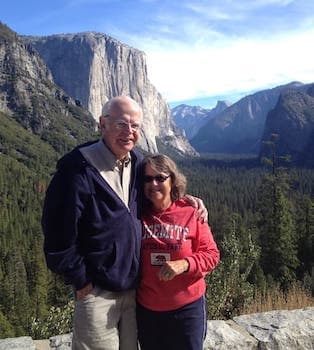
Curated with aloha by
Ted Mooney, P.E. RET
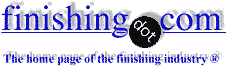
The authoritative public forum
for Metal Finishing 1989-2025
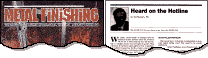
-----
Interpretation of ASTM B117 Salt Spray Corrosion panels
I am having difficulty in evaluating salt spray failure on conversion coated aluminum 2024 T3 panels per ASTM ASTM B117.
Please define a ratable spot or pit based on size(what is counted and what is not counted). I am seeing numerous spots of size barely discernible using naked eyes if not for striations of light pink identifying the spot locations, most spots would not be visible. In some areas still the panel shows light yellow color. Measurement of visible spots at 10X mag indicates perhaps 1-8 spots per panel up to 0.003" diameter).
I am allowed to have 5 spots or pits per panel or a cumulative total of 15 spots for 5 panels, none of the pits may exceed 0.031" and no specification mentions what is the smallest diameter to be considered a spot. Discoloration is permissible.
Duane PraymayerAerospace - Winnipeg, MB, Canada
2004
2004
ASTM D1654 gives some rating guidelines for decorative coatings, but they are useless for what you describe. There is no ASTM method of rating pits in the size range you describe, but there may be a mil spec or industry spec for it.
This type of specific interpretation is usually (and best) left between the vendor and customer. Depending on the application the definition of a "pit" may cover a huge range. I would generate a suggested set of standards using 10X micro-photographs, and present them to the customer for interpretation as to what is acceptable.
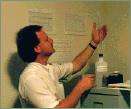
Jeff Watson
- Pearland, Texas
What you describe is somewhat common with panels that are over a year old. Try it in brand new panels from a new sheet of aluminum. Bet your mini pits go away.
James Watts- Navarre, Florida
2004
2024 is more difficult to pass salt spray. Best results if you do not etch, and use a good quality desmut. The proprietary desmuts work better than home brew. Allow the panels to air dry for 24 hours after coating, and handle very carefully to avoid any scratches or damage to the chromate coating.
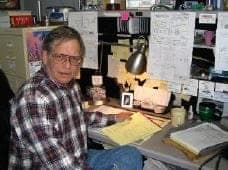
Jeffrey Holmes, CEF
Spartanburg, South Carolina
2004
I agree with Jeff. However, I have found that better test results are typical if you use a chromate containing desmut/deox as opposed to the ferrous types.
Gene Packmanprocess supplier - Great Neck, New York
2004
2004
Although MIL-C-5541 (Chemical Conversion Coatings) doesn't give any significant guidance on the matter, MIL-A-8625 / MIL-PRF-8625 [⇦ this spec on DLA] (Anodize) does define a pit as an area of localized corrosion with depth greater than its width. 8625 also lists 5541 as acceptable for touchups, so you may be able to use the same definition of a pit.
Good luck.
Jim GorsichCompton, California, USA
Q, A, or Comment on THIS thread -or- Start a NEW Thread