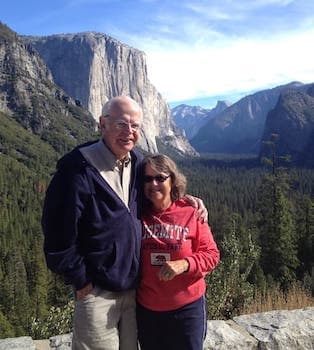
Curated with aloha by
Ted Mooney, P.E. RET
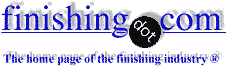
The authoritative public forum
for Metal Finishing 1989-2025
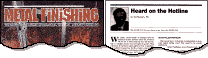
-----
What metal to resist corrosion in vaporized sodium?
I have a design issue where vaporized sodium (Na) at 700 - 800 C, is flowing in a vacuum. I would like to have a recommendation as to the material that will provide suitable corrosion resistance for this service. I know that 316SS is used for the liquid metal reactors. However here we have considerably higher temperatures, a vacuum, and vaporized sodium.
Brian ThurgoodConsultant - San Diego, California
2004
Try asking Southern California Edison what their experience was at their (now de-commissioned) Daggett Solar-Electric plant.
Tom Gallant- Long Beach, California
2004
February 26, 2010
Here are some metals that are highly resistant to sodium metal:
Tungsten, Molybdenum, Vanadium, Niobium and Iron.
Iron pipe might be your lowest cost solution, followed by molybdenum and tungsten.
Inventor - Bronx, New York
March 11, 2010
You might consider using force fields to direct the vapor away from the wall. If the vapor does not touch the wall, there can't be any corrosion.
For example, electrostatically charge the vapor and the pipe wall with the same polarity. The higher the charge, the less frequently gas atoms will hit the wall.
Electromagnetic fields are used in fusion reactors to keep plasma away from walls. You might look into a scaled-down version of that technology to protect your pipes.
- Bronx, New York, USA
March 11, 2010
I am confident you can use ordinary iron pipe without the use of force fields. Here is why:
At the temperature of sodium vapor you anticipate using, the partial pressure of sodium is very low. Even at 800 C, the vapor pressure of sodium is only 0.941 KPa, <1% of atmospheric pressure. At this pressure, heat is not efficiently transmitted throgh the vapor or into the pipe by convection.
Presumably the outside of the pipe will be at room temperature. Thus, although the gas vapor will be very hot, the inside wall of the pipe will be relatively cold.
A tiny fraction of gas vapor that hits the cold iron will condense onto the wall. In time, a thin layer of solid sodium should develop. Iron is known to be completely inert to corrosion by solid sodium (in the absence of air). Gaseous sodium will be prevented from touching the underlying iron by the overlying solid sodium. Your sodium vapor will not be contaminated.
You can "strike" the inside of the pipe with thin sodium before you start your process by chilling the pipe before filling it with sodium vapor. Then you are sure of complete isolation of the iron from your vapor.
Were you transporting liquid sodium, that would be a different story, especially if the temperature in your plumbing changes significantly. There is a big difference between comparatively cold low pressure sodium vapor and hot molten sodium. Don't be fooled by research done for nuclear power plants; your application is considerably less demanding, at least as far as corrosion is concerned.
PTFE (Teflon) is surprisingly resistant to sodium and has a very high service temperature. You can probably use ordinary PTFE pipe tape, with attention to not exposing a loose end of tape inside the pipe where it would be directly exposed to vapor. Otherwise, you'd end up with NaF contaminant, which depending on your process could cause problems.
By similar arguments, ordinary cheap steel pipes might even work for your application. For very little money you could do an experiment with the cheapest steel plumbing you can find. If it doesn't work, you will have spent probably less than $100. But if it works, you will save probably tens of thousands of dollars.
How are you creating the vapor? Do you expect hot spots in your plumbing?
I would be very interested to hear how it works out.
- Bronx, New York, USA
Q, A, or Comment on THIS thread -or- Start a NEW Thread