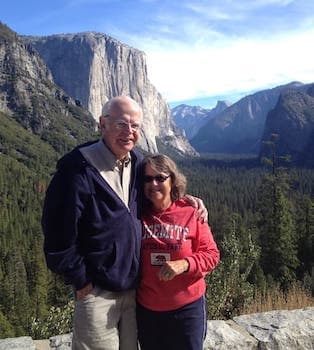
Curated with aloha by
Ted Mooney, P.E. RET
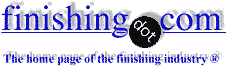
The authoritative public forum
for Metal Finishing 1989-2025
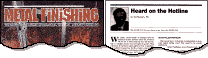
-----
Zinc phosphate and powder coating to prevent rust from spreading from scratch
Q. I have several questions regarding Pipe coated with zinc phosphate and powder coat. The situation is the coated pipe (described above) was put under salt spray testing, we put a line of scratch through the coating before putting into the salt spray testing. what happened was, the scratch started to rust, and the powder coating surrounding the scratch started to peel. Is this normal? Isn't the zinc phosphate coating supposed to prevent the rust from spreading even if there is a scratch? Or isn't the powder coating suppose to prevent the rust from spreading and stay on the pipe instead of peeling off? Can anyone help me on this subject?
Johnny Chwangstudent - Chino Hills, California, USA
2004
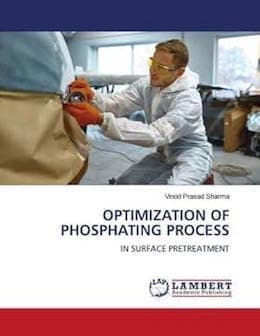
avail from AbeBooks, or Amazon
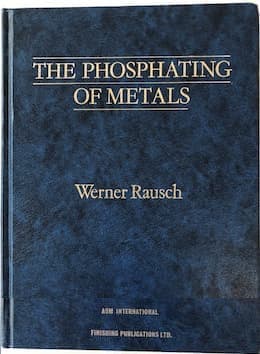
avail from eBay, AbeBooks, or Amazon
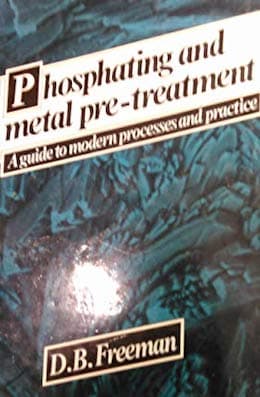
avail from eBay, AbeBooks, or Amazon
(as an Amazon Associate & eBay Partner, we earn from qualifying purchases)
A. Hi Johnny. Yes, zinc phosphatizing is supposed to be of substantial help in resisting undercut corrosion; but that does not mean it stops it dead, 100 percent, regardless of circumstance or length of exposure. Without any data or any comparison runs, it's not possible to say what the problem is or even if there is a problem.
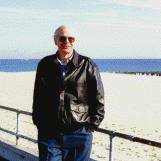
Ted Mooney, P.E.
Striving to live Aloha
finishing.com - Pine Beach, New Jersey
Q. Is it even possible to pass through a 1000 hour salt spray test for this application?
Johnny Chwang [returning]- Chino Hills, California, USA
A. Yes.
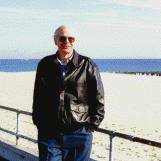
Ted Mooney, P.E.
Striving to live Aloha
finishing.com - Pine Beach, New Jersey
Q. I have several questions for my research paper. I used a steel pipe coated with zinc phosphate, then powder paint. Going through the salt spray test. But before the test, I cut a scratch into the steel pipe, then put into the test, the test shows with approximately 200 hours, the steel beginning to rust on the scratch. And cause the paint surrounding the scratch to peel off.
My questions are:
1) how come the paint start to peel off?
2) Is it possible to have the pipe pass 1000 hour salt spray test?
3) Any suggestions to prevent these?
Thank for anyone that could help me on these questions.. thanks...
Johnny
Johnny Chwang [returning]Direct leader - Chino Hills, California, USA
![]() |
A. Hi Johnny, You need to provide more information before your questions can be answered properly. 1. What does the phrase "pass 1000 hr salt spray" mean to you? For one person 3 mm of creepage would be considered a "pass." For others, it might be 6 mm or some other value. 2. Can you describe all of the steps in your pretreatment process? 3. Has this paint been formulated to provide the kind of corrosion resistance that you're looking for? In other words, have you run your salt spray test with some kind of standard, whose results can be compared with those of your pipe? George Gorecki- Naperville, Illinois A. Johnny, A typical corrosion requirement defines the number of hours in salt spray (1000 hours in your case) and the maximum allowable creepback from the scribe, which does not appear to be defined in your case. 3 mm maximum creepback is a common requirement for high-performance applications. Toby PadfieldAutomotive module supplier - Michigan Q. Sorry to bother again, but I really wonder what could have cause the paint to peel in the salt spray test? Some told me the dust between the layer of powder coating and the zinc phosphate coating caused the paint to have bubble and start to peel off during the salt spray test. Are there any possible reasons? Thank you very much for answer all these questions for me... Johnny Chwang [returning]- Chino Hills |
Q. The salt spray test is the typical ASTM B117 test, with a scratch on the tube. The 3 mm corrosion will consider a fail in the salt spray test. I have searched many places, and one of the biggest factor they told me was the crystal size difference would make the specimen to fail within 1000 hours. Is this true? What would consider a good crystal size that can pass the test? Thanks for all the response, I have really gained a lot from it.
Johnny Chwang [returning]- Chino Hills
Q. Hi,
Would anybody be able to tell me of an economical way to purchase zinc phosphate. The only stuff I've found is $40 a gallon. The application I want to use it for is to spray down areas on the frame of my classic car that I'm working on that have bare metal and I'm not ready to paint. My goal is to limit surface rust while I work on my car over the next year. Very much appreciate any information you may have.
Thank you,
- Santa Barbara California US
January 29, 2016
A. How about purchasing a rattle can of galvanizing spray paint they are like $6 a can. The ones that show they have over 90% zinc are very good at providing you with a zinc coating; on some tests they have been able to outlast even hot dip galvanized steel.
Marvin Sevilla- Managua, Nicaragua.
January 30, 2016
Q, A, or Comment on THIS thread -or- Start a NEW Thread