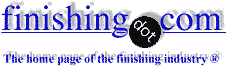
-----
Hard chrome pitting on high tensile material
Does anyone have a suggestion to minimize pitting and rough finish on 4140 induction hardened hydraulic rods.
Our typical build is .005" - .008" per side on diameters up to 14". The bath is a self regulating Atotech HCR710 with stick anodes.
Current process is 2 min. etch, scotch brite scrub, further 30 sec. etch, ramp up to 1 amp per in. Jobs come out bright but rough. After grinding we are left with pit holes particularly at the ends. The current density we are using is the lowest that will plate with our anode set up.
If we flash the parts and polish we can build up with no problems. but it is expensive to process as some of our parts are 1500 pounds plus.
Any suggestions would be appreciated.
James NadolnyHard Chrome and Hydraulics - Vancouver, B.C., Canada
2004
Your pits most probably come from nodules that break off during grinding. Improve your filtration and demagnetize your parts to avoid the pickup of metallic particles during plating. Also, eliminate sources of abrasive contamination around your shop.
Guillermo MarrufoMonterrey, NL, Mexico
2004
I understand the contamination theory causing nodules. But what I don't understand is why my mild steel parts come out smooth as glass with no pits.
Also will a porous pot remove iron and would you recommend the use of one?
How does one go about demagnitizing a 1400 lb. hydraulic rod?
James Nadolnychrome and Hydraulics - Vancouver, B.C., Canada
2004
I think Guillermo is right, nodules that break off during grinding cause the pits. Especially as when you flash the parts and polish, they then plate OK. It all suggests that you are plating on to rough steel. 2 min. etch, scotch brite scrub, further 30 sec. etch, Seems an awful lot of etch to me, On hardened steel, IŠve found that over etching gives roughness, and on steels of Rc50 I would only etch for 10 to 15 seconds, on to plate and ramp up to current density. I did have a problem a few years ago with poor heat treatment, and as we ground the shafts, it plucked at the surface, if you rub your hand over the surface after grinding you will feel any roughness.
Steve Kelsonhard chrome platers - Sandbach, Cheshire, UK
2004
I agree on the over etch on really hard steels. I hate tank anodes. Conforming is far superior, less time,less grinding less grief. A simple caustic clean, rinse and activation in a chrome based etch in reverse should work wonders and not require any hand work.
You need to look at the pits with a 10X glass. If they are round bottomed, they are gas pits. If they are craggy edged and have a tiny post in the bottom, then you are plating trees or needles that break off. (a grit like dirty part before plate that could be metallic or abrasive from the hand operation.)
If your using a self regulating bath, the porous pot will be destroyed by the fluoride. If not, they are great. filtration of chrome tanks can be tough on filters, depending on the catalyst used in the formulation.Try not to stir up the sludge on the bottom of the tank during the week and have the last shift of the week hoe the sludge out as part of their job.
James Watts- Navarre, Florida
2004
Q, A, or Comment on THIS thread -or- Start a NEW Thread