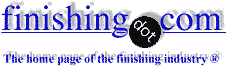
-----
Increasing humidity resistance of a chrome-plated ABS plastic part
Q. We are chrome-plating ABS plastic for automotive applications. What can be done during the chrome-plating process to increase the humidity resistance of the chrome-plated surface? Also, during an intense thermal shock test we are getting delamination of the chrome. What can be done to prohibit this from happening? Thank you in advance for your suggestions.
Greg Rivardauto parts mfg. - Oak Park, Michigan, USA
2004
A. What kind of problems do you have with humidity? About delamination, it may be a number of things, from production processing of the plastic part, mold design, selection of resin, to plating problems such as contamination, chemical unbalance, insufficient or excessive soak, temperatures, plating parameters. POP is very complex. Almost impossible to shoot problems via an internet chat, more so with such little information you gave.
Guillermo MarrufoMonterrey, NL, Mexico
2004
A. As a molder of platable ABS, I can tell you a few tricks that are not commonly practiced by molders.
1. The tool steel should be above 150 °F.
2. The melt temp should be near the high end of the material spec.
3. Fill the mold SLOWLY. Run a viscosity curve on the mold and pick a fill time that is longer than the flat part of the curve. Or if you run a study of how fast you can fill(without burning) and the slowest it can be filled, pick a fill time in the middle.
When you fill too fast, the butadiene balls get stretched out and lay flat on the surface. They need to be round so that when they are etched out they leave under cuts in the surface for the mechanical bond.
Joe Phillips- Hillsdale, Michigan USA
2004
Q, A, or Comment on THIS thread -or- Start a NEW Thread