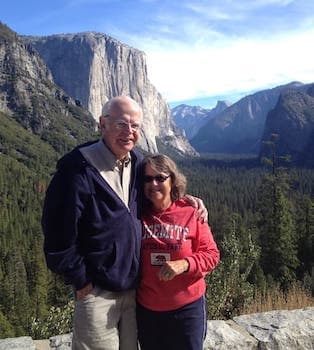
Curated with aloha by
Ted Mooney, P.E. RET
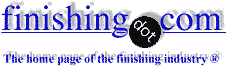
The authoritative public forum
for Metal Finishing 1989-2025
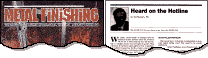
-----
Comparing Phosphating Treatments
Q. Hi, Firstly I want to know about the advantages / benefits of Phosphating (Iron,Zinc)Processes. Secondly which phosphating treatment is better (Iron, Zinc or Mn) and why? Thirdly, what are the applications of phosphating treatments (Iron, Zinc & Mn).
Muhammad AsifPakistan Ordnance Factories - WAH CANTT, Punjab, PAKISTAN
2004
by David S. Peterson
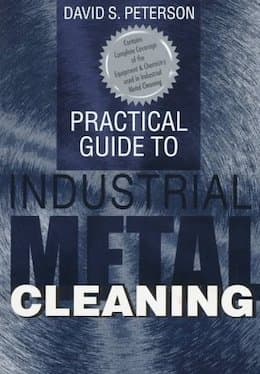
on AbeBooks
or eBay or
Amazon
(affil links)
A. Hi cousin Asif. Phosphating offers "key" to help paints adhere, forms corrosion resistant conversion compounds on the surface, helps relieve anodic "hot spots", minimizes undercutting after a scratch, and probably fights corrosion a few other ways as well. Iron phosphates are the thinnest and offer the least protection, but in combination with proper paints and powder coatings, they can still be outstanding. Zinc phosphates are heavier. Manganese phosphates are generally used for "break in" on mechanical parts rather than as a base for paint.
There is a book "Phosphating of Metals" ⇦[this on Amazon or AbeBooks affil links] by Rausch that you may want to obtain. There was another book devoted to similar issues, Samuel Spring's Preparation of Metal for Painting ⇦[this on Amazon affil links]. Unfortunately, I lost my copy, but it's excellent.
Amazon offers "Practical Guide to Industrial Metal Cleaning" by David S. Peterson.
which I haven't read, but which sounds quite good from the excerpts. The Metal Finishing Guidebook has a good introduction to phosphatizing.
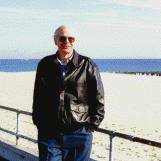
Ted Mooney, P.E.
Striving to live Aloha
finishing.com - Pine Beach, New Jersey
Q, A, or Comment on THIS thread -or- Start a NEW Thread