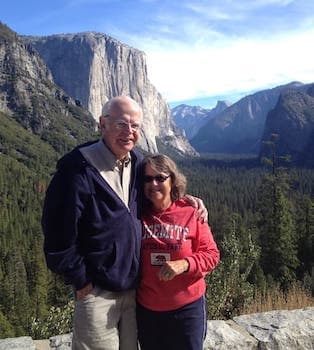
Curated with aloha by
Ted Mooney, P.E. RET
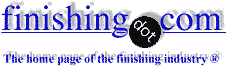
The authoritative public forum
for Metal Finishing 1989-2025
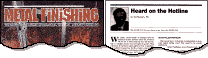
-----
Acid copper sulphate plating problems: black anodes, excess copper, anodes passivating

Several different general types of solutions may be used for copper plating: Acid copper sulphate, Pyrophosphate, Cyanide, and several others. Each has advantages & disadvantages, and you can search the site for dozens of threads about each.
This thread is about "bright acid copper sulphate ⇦ this on eBay or Amazon [affil links] plating" and one of its problems: the anode composition has to be right and the relative surface areas of anode and cathode must be in correct proportion, or problems like too high a concentration of copper, and anode polarization (which will slow/stop the plating) will quickly develop.
Hobbyists might wonder why professionals seem to encounter problems that they don't; an answer which is especially applicable for copper sulphate plating and will help you follow this discussion better is that professionals require 'equilibrium processes'. Whereas a hobbyist might plate a few parts then dispose of his plating solution or put it away to plate a few more parts in a month, when a professional production plating shop plates parts, the composition of the plating solution after they are done must remain exactly the same as when they started because they will be using that same solution for years or decades, and fresh loads of dozens of parts may be going into the plating tank every 10 minutes around the clock. Thus a hobbyist might use a chunk of copper pipe or copper wire for anodes and his plating might turn out fine, and he may wonder why we need all this nonsense talk about 'phosphorized anodes' ... but actually if he continued plating lots of parts his plating solution would very quickly get out of whack and become unusable.
Hello,
We are trying an historical recipe for electrotyping. Unfortunately, after a few minutes copper sulphate crystals were growing at the anode, for which we have no explanation. Even though the copper deposit at the cathode looked fine (rose coloured), plating discontinued after the anode was fully covered with crystals. With a cleaned anode and yet slower plating conditions, a black film formed at the anode which had seemingly slowed down the plating, leaving a very thin layer of copper deposit.
Plating specifications:
Current density: approximately 1.2 A/dm2
Copper anode faces silver cathode with a distance of 11 cm, electrodes have same dimensions (approx. 4 cm x 3.5 cm)
Acidic copper sulphate solution consists of 300 g copper sulphate in 1500 ml demineralized water with 75 g sulfuric acid.
Plating was interrupted and the cathode removed from the plating bath on several occasions, assuming that the plated copper deposit would remain conductive.
Any advice would be greatly appreciated, many thanks in advance!
- Amsterdam, The Netherlands
June 2022
A. Hi M. The formulation you describe, and the current density you are using sound okay; but the presence of crystals indicates a copper concentration that is too high, at least locally where they are forming ... and yes, too high a concentration can stop or seriously slow the current flow. Is the bath heated? What temperature? Do you have air agitation or other good agitation?
11 cm anode-to-cathode spacing sounds like a lot more than needed, but it doesn't sound like the cause of the problem. Please double check that a mistake wasn't made in making up the bath which might have resulted in seriously too high concentration.
Popat's suggestion below of lower anode size might help. But an immediate fix, also discussed below, might be to simply dilute the bath by 25%.
Luck & Regards,
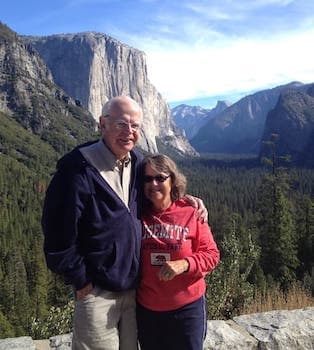
Ted Mooney, P.E. RET
Striving to live Aloha
finishing.com - Pine Beach, New Jersey
Q. Hi Ted,
Thank you so much for your quick response and your suggestions, which we'll follow up. I'll get back with what we might encounter. What I can say for now is that the bath has no agitation and is at room temperature without additional heating.
Best,
M. Pilko
- Amsterdam, The Netherlands
June 15, 2022
A. Hi again. Besides cutting the concentration of the bath, I think it's necessary to add agitation (air agitation should be okay), and you may need to add just a pinch of chlorides (I don't know if you have any analytical capacity); a little chloride not only improves conductivity and anode corrosion but, in your case of plating onto silver, precipitates any rogue silver that has entered the solution and may be contaminating it.
Luck & Regards,
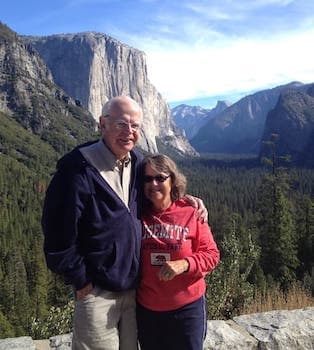
Ted Mooney, P.E. RET
Striving to live Aloha
finishing.com - Pine Beach, New Jersey
Q. I have a 150 litre acid copper plating tank. I got it analyzed and was told that it was over concentrated with copper sulphate by a 1/3. I think I may have been using too large of an anode area. If I plate with the very minimum anode area that I can get away with, will the concentration start reducing?
I hope someone out there will be able to help me on this subject.
Hoping for a reply.
Regards,
Daniel
plater - Belfast
July 20, 2022
A. Hi Daniel. We appended your inquiry to a thread where you can see that this problem is perennial. One reader suggests it can be fixed with greater anode area, another suggests it can be fixed with lower anode area. But I think the most trustworthy fix would probably be to make sure you are using only phosphorized anodes, and installing some titanium anodes temporarily until the concentration is reduced.
Alternately, the traditional simple but wasteful answer is to throw away 25% of your bath and replace it with that much distilled water :-)
Luck & Regards,
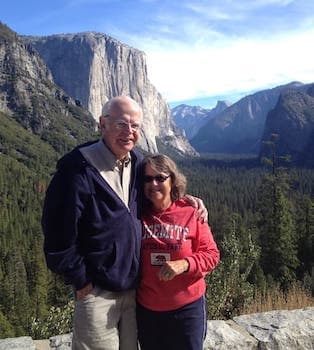
Ted Mooney, P.E. RET
Striving to live Aloha
finishing.com - Pine Beach, New Jersey
⇩ Related postings, oldest first ⇩
2002
Q. I am new to electroplating and required to do copper electroplating. My copper electrolyte contains copper sulphate, sulfuric acid, and hydrochloric acid, without brightener. A black film has formed on phosphorized copper anode during plating. Since I only have temporary setup, the filmed copper anode was kept in deionized water. I have noticed the black film has gone within a day. Can this be caused by:
1) The type (and quality) of my copper anode,
2) The electrotype recipe I used, or
3) The prolonged immersion in water>
Note that when I took the filmed anode out of the tank and placed it vertically inside fume cupboard, the film has gone within an hour.
Any help of what would be the cause of my problem is greatly appreciated.
Regards,
Olarn Rojanapornpun- Sydney, NSW, Australia
2002
A. Olarn Rojanapornpun,
I think black film on anode is normal but once you plate, the film dissolves in solution in some cases. If you have a black film permanently on anodes, it may be anode polarization problem. Once your anode polarizes, that time mostly gives lost coverage on parts and you want to get certain amps but you do not because of lost conductivity. If Anode polarizes, you do not need copper anode as usual or need less anodes than normal.
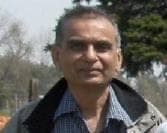
Popatbhai B. Patel
electroplating consultant - Roseville, Michigan
2004
Q. Hi:I am using a standard acid copper bath
33 oz per gallon copper sulphate
8 oz per gallon sulfuric acid
Proprietary levelers and brighteners.
The bath has been tested and is within good limits for operation. My problems is that as I plate, the voltage stays even but the amperage drops off after about a 1/2 hour of plating. Turn the voltage up to the correct amperage and it continues to drop off.
If I shut the power off and let the bath sit dead for a minute then the amps will go to the appropriate setting that I have the volts on. But, it will start dropping off again. I have swapped out the power supply and the same results. I pulled and cleaned the anodes/bags and it worked great for about 3 weeks. Then the same thing starts happening.
I am using phosphorous copper anodes. I have a mix of bar and basket type copper anode.
Temp is 75 °F.
Air agitation
It seems to me that the anodes are going passive as I plate?
Is this why people do periodic reverse current? If so, how often should I do this and what do you use to do this with? i.e., what is hanging on the bar at the time you reverse the current. Another copper anode?
Any help would be appreciated.
Thanks
Tom Haltmeyersmall shop - PHX, Arizona, USA
2004
A. TOM !
I READ YOUR PROBEM IN ACID COPPER BATH -AMPS GOING DOWN
1. I would like to check your rectifier ripple. 2. What kind of the bags you use and wash the bag before you use. 3. Look like you lost the conductivity in bath. 4. If your copper sulphate concentration too high and bags plugged up & temp too low- you lost conductivity in bath. 5. Check sulfuric acid concentration more often. 6. Check all electrical connection -rectifier and plating bath.
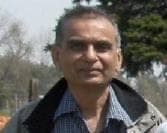
Popatbhai B. Patel
electroplating consultant - Roseville, Michigan
A. What is your anode to cathode ratio? What is the chloride level? What current density are you attempting?
Russell Richter- Danbury, Connecticut, USA
2004
A. Hello. In my opinion, this event is related to rectifier problems. Your bath parameters normal. And we consider your baths contacts good. So there is left any suspicion event. You must maintenance your rectifier, then we can think other reasons.
Emre Tuna- Turkey
2004
2004
A. MAXIMUM LIMIT OF IMPURITIES IN PHOSPHORISED COPPER ANODE
- COPPER:- 99.9 % MIN.
- PHOSPHOROUS:- 0.038 % MIN.
- sulfur :- 0.0018 % MAX.
- ZINC :- 0.0025 % MAX.
- SILVER :- 0.001 % MAX.
- NICKEL :- 0.0015 % MAX.
- LEAD :- 0.001 % MAX.
- BISMUTH :- 0.0001 % MAX.
- MANGANESE:- 0.0001 % MAX.
- SILICON :- 0.0001 % MAX.
- ARSENIC :- 0.001 % MAX.
- ANTIMONY :- 0.001 % MAX.
- TIN :- 0.001 % MAX.
GOOD LUCK.
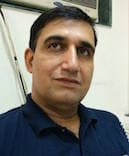
Ajay Raina
Ludhiana, Punjab, India
Q. Thanks for your replies........
I am getting the baths reanalyzed now. I will post the results.
I have found that heating the bath to about 80 °F will cause the amp drop to slow down.
To me is seems the copper anodes go passive and get a non conductive film on their surface. Once I shut the power off and let everything sit for a minute, turn the power back on, the amps are back up to where they should be.I figure this is because the sulfuric in the bath takes the non-conductive film off.Then they start falling off again to about 1/4 of what they should be. I can turn up the volts but it will continue to fall off on the amps. I'm suspicious that I don't have enough sulfuric in the bath to keep it conductive.
Also, I swapped out the power supply and the results are the same. Anode/cathode ratio is at a min of 2:1. I did pull all anodes and clean them in a 1/4 sulfuric to 1 water bath. Everything worked good for about a week and then the problem came back.
Thanks
Tom Haltmeyer [returning]small shop - PHX, Arizona, USA
2004
A. Tom,
I had a similar problem a few months ago and after going crazy a little by doing a number of things like the ones in these postings. I end up adding more copper bars, and guess what, my problem disappeared. Sometimes the ratio is a very tricky thing. I hope this works for you. Please let us know how do you end up fixing your problem.
Sergio Gonzalez- Guadalajara, Jalisco, MEXICO
2004
A. If your bath contains sulfuric Acid more than 50 ml/litre. Then copper sulphate in your bath gets crystalized. It gets crystalized on the anodes as well. So if you increase the temp it gets dissolves & again it gets crystalized after temp comes down and electrolysis starts. I faced similar problem a Year ago, when I decreased sulfuric acid content in my bath the problem got solved. Another reason may be insufficient chloride it should be around 60-80 ppm. Kindly let me know if the problem got solved.
N K Praveen Kumar- Secunderabad, ANDHRA PRADESH, INDIA
2004
After analysis it looks like my sulfuric acid was too high.
We diluted the bath by 25 percent and it's working perfect now.
Tom Haltmeyer [returning]small shop - PHX, Arizona, USA
2004
Multiple threads merged: please forgive chronology errors and repetition 🙂
Copper anode appearance
2007Q. Hello,
I have some oxygen free copper anodes that have been pulled from an acid bath. They are discolored (light blue) and rough (some are pitted). What would cause these conditions? The tank parameters are as followed:
baumé 19-21
CuSO4 220-235 g/l
H2SO4 45-55 g/l
Temp 27 °C
A/dm 20
The copper anodes also form a black film. I have read conflicting information in regard to rinsing the oxidized film off. Rinse or leave on? We do not bag the anodes, they are in racks.
Thank you,
Rotogravure - Harrisonburg,Virginia
A. Michael,
The reason the anodes look the way they do is because oxygen free Cu anodes don't belong in an acid bath. Cyanide or alkaline baths, yes. You should be using phosphorized Cu anodes. In your acid Cu bath formulation you don't mention the chloride level, which also aids in proper anode corrosion. Most baths require a minimum of 85 ppm. Go to your tech data sheet for the bath and it will tell you the phosphorous content for the anodes.
Process Engineer - Syracuse, New York
2007
2007
A. It looks like your ratio of sulfuric to copper sulphate is off. Try to run a ratio of 1/3 sulfuric to copper sulphate or better. Check your chlorides (50 to 80 ppm). Do you run a wetter? Anode to cathode surface area could be off. You could be passivating. Temperature should be approx. 70-100ish.
Good Luck
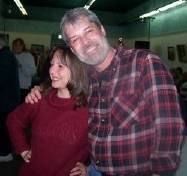
Trent Kaufman
electroplater - Galva, Illinois
Q. We are using Okuno copper plating system. What is the anode to cathode ratio? Why phosphorised copper anodes are used in copper plating?
Vijikumar Abelpinang, Malaysia - Bayanbaru, Pinang, Malaysia
May 20, 2008
A. Hi, Vijikumar. Sorry, but I'm not quite clear what you mean by 'what is the anode to cathode ratio?'.
If you asking for the meaning of the phrase, it's the surface area of the anode basket compared to the surface area of the workpiece. If you are asking what anode to cathode ratio Okuno recommends for this process, you would have to ask them, but it's usually between 1:1 and 2:1 (it may be on their technical data sheet).
Is this an acid, pyrophosphate, or cyanide bath? Probably the main reasons phosphorized anodes are used is to try to minimize copper buildup by slowing dissolution, as well as keeping copper particles from breaking off the anodes; such particles could plate out onto the workpiece as roughness. Good luck.
Regards,
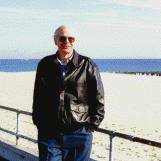
Ted Mooney, P.E.
Striving to live Aloha
finishing.com - Pine Beach, New Jersey
May , 2008
Q. I'm using copper acid bath and use OFHC phosphorized copper anodes.
I have a question that when the titanium anode baskets are cleaned monthly the copper anodes turn to black colour.
Please explain what is the black thing and why it developed?
- Rudrapur, Uttarakhand, India
August 2, 2010
![]() |
Q. What does the anode to cathode ratio mean? - Mumbai, Maharashtra, India March 18, 2013 March 19, 2013 Hi Abhiraj. Let me quickstart any readers who may be confused -- HOW ELECTROPLATING WORKS: In the electroplating process, the item you wish to plate onto is immersed into a bath of plating solution and attached to the negative pole of a direct current circuit (battery, rectifier, or power supply); for this reason, that workpiece is called the cathode. Another piece(s) of metal is put into the plating solution and attached to the positive pole, and for this reason it is called the anode. As the battery pulls electrons from the anode and pumps them over to the workpiece, the workpiece begins to accumulate a negative charge, and attracts the positively charged copper ions, Cu++, that are in the solution. As those ions touch the workpiece, the excess electrons neutralize the Cu++ ions, turning them into Cu0 metal. Meanwhile, you can choose to either make the anode(s) from an impervious material like platinized titanium, or you can make it from copper. It is usually best to make it from copper because then, ideally, for each Cu++ ion that was in the bath and became plated out onto the workpiece as a copper atom, a new copper atom, Cu0, from the anode will dissolve into solution as a copper ion, Cu++, and keep the bath in balance. When the balance is working properly, the concentration of copper in the bath stays consistent instead of growing or declining and things remain under control. To keep this balance, i.e., to make sure that the anode will dissolve copper into the solution at exactly the same rate as plating onto the workpiece removes it, requires that we watch several things: First that the surface area of the anode is in good proportion to the surface area of the workpiece, generally that there is about 1 to 2 square feet of anode surface area for each square foot of cathode area. That is the 1:1 or 2:1 anode to cathode ratio we speak of. Secondly, that the composition of the anode be carefully controlled so that it neither 'passivates' (refuses to dissolve) nor dissolves too efficiently (resulting in an ever increasing copper concentration in the plating bath). That is why different anode compositions are used for acid vs. alkali plating baths. As for the positioning of the anodes, you can see from the above discussion that the plating goes where the current goes. And you already know that electricity takes the path of least resistance. So it is important that the anodes be as close as practical to equidistant from all points on the workpiece; since items to be plated usually have two sides, this generally means that your little " + - + " is correct most of the time. Regards, ![]() Ted Mooney, P.E. Striving to live Aloha finishing.com - Pine Beach, New Jersey |
Q. I also have similar problem to this, that is, in our acid copper electroplating bath all the copper anodes gets black.
We are using phosphorized copper anodes in baskets? If the chloride concentration of the bath is high, how it can be brought to normal range?
What should be the pH of acid copper bath?
Your opinions in this regards highly appreciated.
- Anuradhapura, Sri Lanka
April 25, 2012
A. Harsha,
It is natural for Phosphorous Cu anodes to build up a black film in acid Cu plating. This presence of black film doesn't mean your anodes are passivating. I am not sure of what exactly you are seeing. Because acid Cu plating baths contain sulfuric acid, the pH is not something that has to be monitored. To answer your question, the pH should be less than 1.0. If your anodes are passivating you should do a complete analysis of the bath, then take measures to bring the bath to operating range. If the bath analysis does reveal a high chloride level, bath dilution with the add back of other key components would be the easiest.
Engineering - Mesa, Arizona, USA
April 30, 2012
Q. I would appreciate if someone could advise me when the anode black film is formed and peeled off during the plating cycles, what is the factor to control the black film formed and peeled off in the cycles -- such as the plating potential difference I guess? I have seen this in the Hull Cell test but could not determine whether a rapid form and peel off will be better than a longer period of forming and peeling off of black film?
Albert Gwee- Johore, Malaysisa
September 20, 2014
A. Hello Albert,
Since no one has answered your question I will try. First of all it is very common for black film to form on Cu phos anodes in an acid Cu plating solution. I am not sure what you mean by "peeling" of the black film. This film that is formed is cupric oxide and will not peel. When you pull the anodes out of the bath after plating cycles you will notice a light film which you can rub off a good portion with your finger. If you are referring to Cu flaking from the anodes, then you have a serious problem which can be caused by a few different reasons. Your anodes should be bagged using polypro or Dynel. The amount of chloride in the solution facilitates proper anode erosion. Check your tech data sheet for the Cu bath and it will tell you the range. Normally is is 50 - 70 ppm. Hope this helps.
Process Engineer - Phoenix, Arizona USA
October 2, 2014
Researching passivation level of copper anodes
Q. I'm working on a project to evaluate the efficiency of copper anodes, and the theme of passivation is getting into my project. I wanted to know a trustable method to measure the passivation level of the copper anode. Also I did some research about copper anodes, and found that increasing the salts concentration (Cl-) I could extend the anode working time before it starts to passivate, any thoughts on this?
Thanks.
- Mexico
October 25, 2017
A. Hi Ricardo. I'm a little confused about your project...
First off, exactly what do you mean by efficiency? In electrochemistry of this sort it generally means what percentage of the applied current goes towards the desired electrochemical reaction (in this case, dissolution of copper) vs. undesired reactions (like separating the water of the solution into H+ and OH-). Depending on the electrolyte you are using and some other factors, the efficiency can exceed 100%; in some cases that can be a problem since the buildup of copper can throw things out of balance.
I'm not sure whether 'passivation level' is even a clear and valid concept, let alone measurable, when separated from bath conditions. But you can determine the anode efficiency by weighing the anode before and after the application of a given number of ampere hours of current, and applying Faraday's Law (96,485 ampere-seconds dissolves one gram equivalent weight at 100% efficiency).
High Cl- levels will almost certainly lead to high anode efficiency, but this seems a rather abstract finding unless we understand the application of your work because, for example, high Cl- levels might make for severely stressed and worthless copper electroplates or electroforms. Good luck.
Regards,
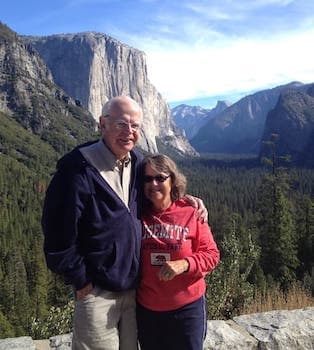
Ted Mooney, P.E. RET
Striving to live Aloha
finishing.com - Pine Beach, New Jersey
October 2017
Q. Thanks for answering so fast, Ted.
I'm using a copper sulphate bath and phosphorous copper anodes, and in our baths the anodes passivate around 3 weeks after the make up (they're used frequently). We want to know a method to evaluate how the passivation evolution (a quantitative method), in order to be sure that we are forced to etch the anodes for a next use. We propose to measure the Resistivity near the anodes, but there are some uncertainties. Any thoughts on this?
Thanks for the help.
PS: Big fan of this website.
- Sonora, Mexico
October 26, 2017
A. Hi Ricardo. Topic 848 contains a good discussion on this subject and recommends Modern Electroplating for a better understanding. It seems to me that you may not have enough anode area, as that seems to be the major cause of passivation in sulphate baths.
It would seem to me that you should be able to "track" passivation from the required voltage to maintain current density or from solution analysis for copper content. Good luck and thanks for the kind words.
Regards,
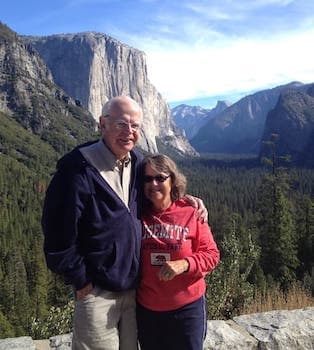
Ted Mooney, P.E. RET
Striving to live Aloha
finishing.com - Pine Beach, New Jersey
October 2017
Copper concentration keeps growing in copper sulphate plating
Q. My name is Deb, I work in a copper plating industry, the problem faced continuously that concentration of copper sulphate increase day by day, normal copper sulphate concentration 220 g/l and concentration of sulfuric acid 65 g/l current density 25 A/dm2.
My question is why concentration of copper sulphate continue increase and how to reduce without dilution.
- Kolkata, West Bengal, India
September 19, 2019
A. Hi Debdutta. In a typical plating line, failure to use phosphorized anodes, or perhaps imbalanced anode-cathode ratio or excessive chlorides could cause excessive anode dissolution. But your current density of 250 ASF is very high, about 10X what is used in typical rack plating ... so you are not describing a typical rack or barrel plating line. Is this a continuous coil coating or wire plating line? Please explain what kind of plating installation this is.
Regards,
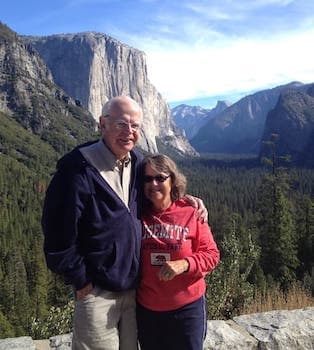
Ted Mooney, P.E. RET
Striving to live Aloha
finishing.com - Pine Beach, New Jersey
September 2019
Q. Can a TDS meter tell me % copper in acid Cu bath?
People are talking about "toss some bath to reduce copper"?
My anodes are 10 ga ss mesh with flattened copper pipe bolted to them. Pipes dissolve and I replace them. if TDS meter says too much Cu I can run SS only anodes and dummy, or add more pipes. If TDS meter won't tell me, what is easy test?
Thanks,
hobbyist - Springfield Oregon
August 7, 2021
Q, A, or Comment on THIS thread -or- Start a NEW Thread