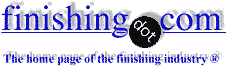
-----
Corrosion in Urea Reactor
Current questions and answer:
March 21, 2017Working Principle of Urea Reactor?
Q. Hello there, I am a chemical engineering student from University Malaysia Sabah. I need some help in acquiring this information for my plant design subject. As the title assigned to me was ammonia ⇦ on eBay or Amazon [affil links] urea plant, therefore I am acquired to design an urea reactor. I am having difficulty in obtaining this information on the internet. Therefore, I hope that you can answer my doubts or suggestions to where I can find the answers to them.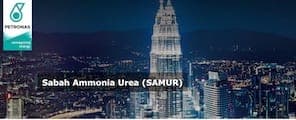
----
Ed. note Nov. 2018:
Apologies but SAMUR has re-arranged their site and Sarventhan's link to the urea reactor no longer works :-(
1. The simple working principle (inlet, outlet, how the urea reactor looks like) of the urea reactor in SAMUR .
2. Design of interior part (overview)
3. What is the safety elements used to avoid rusting?
4. Type of reactor used? If its PFR, then is there any specific reason why use PFR?
5. Suggestions if there is any calculation to get the retention time in the PFR.
6. If we want to recycle ammonium carbamate, then how do we manage the inlet for urea reactor?
7. Do we need a manhole flange design for our urea reactor design?
8. What is your suggestion for the reactor sizing if the capacity of the urea production from the reactor is 41000 kg/hr (urea alone not including water biuret and ammonium carbamate)
9. Are there any essential suggestions that you can recommend us to be included in our design that we may have left out?
student - Selangor, Malaysia
January 13, 2022
A. "1. The simple working principle (inlet, outlet, how the urea reactor looks like) of the urea reactor in SAMUR"
The urea reactor, the CO2 is limiting reactant and NH3 is Excess reactant, the conversion calculation in terms of limiting reactants, about 60-70 % conversion achieved as per process used.
"2. Design of interior part (overview)"
The Urea reactor. The Liner is used for Urea reactor, this liner is SS316L (Urea grade, 2-RE-69(25/22/2) and Titanium also used for urea reactor material. The passivation air is required for urea reactors and other equipments for pressure the CS shell are used in urea reactor this is multilayer vessel and designed as per pressure vessel.
3. "What are the safety elements used to avoid rusting?"
The passivation are used in SS material and depends upon N/C ratio, Temperature of the vessel.
4. "Type of reactor used? If its PFR, then is there any specific reason why use PFR?"
Generally used Plug flow reactor but you can install internals like baffles and trays the mixed flow CSTR can be used but overall must be PFR.
5. "Suggestions if there is any calculation to get the retention time in the PFR."
The Retention time =Volume of Reactor/Feed Volume
6. "If we want to recycle ammonium carbamate, then how do we manage the inlet for urea reactor?"
By Control Valves and Flow meters in inlet line of NH3/CO2 and recycle Carbamate.
7. "Do we need a manhole flange design for our urea reactor design?"
Yes, the man hole designed as per vessel entry rules generally 600 mm
8. "What is your suggestion for the reactor sizing if the capacity of the urea production from the reactor is 41000 kg/hr (urea alone not including water buret and ammonium carbamate)"
For 41000 Kg/hr Production The Minimum size of Urea reactor is 35-40 meter and ID is 2.0 meter.
9. "Are there any essential suggestions that you can recommend us to be included in our design that we may have left out?"
Safety in plant , i.e., instrument safety, mechanical safety and process interlocking should be there.
MATERIAL TECHNOLOGY FOR FERTILIZERS INDUSTRIES
UREA PLANT ENERGY SAVING BY SELECTION OF LINER MATERIAL AND INTERNALS
REACTOR KINETICS OF UREA FORMATION
AMMONIA UREA PLANT ENERGY CONSUMPTION CALCULATION
Rtd Employee - Agra U.P
⇩ Related postings, oldest first ⇩
Q. Dear sir:
Our urea reactor bottom liner and baffles corroded after 22 months (UTI Plywell) 50% is whitish and 50% is Black from the bottom.
Suresh- South India
2001
? What is the material of construction?
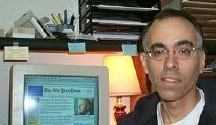

Tom Pullizzi
Falls Township, Pennsylvania
2001
A. Generally this is because of passivation layer loss by operating one of the feeds without passivation air. Presence of iron in feed also causes stress corrosion. Construction material may be defective partially, say at the bottom. Please furnish material of construction.
Stefen Edward- Edingburg, Scotland
2003
2005
A. Normally uneven corrosion occurs due to poor feed rate and quality, N/C ratio; high inert; chloride and sulfides and also iron precipitated water.
1. Increase liquid ammonia rate
2. Maintain volumetric flow rates
3. Complete primary reaction at the shell level
4. Keep mole ration above 4.4
5. Prevent iron precipitated water
6. Check CO2 purity - 99.3%
- Tampezeal, Austria
A. Normally high corrosion speeds in urea synthesis equipment occur due to lack of passivation.
316 L Urea Grade needs a continuous oxygen supply to assure a passive layer builds up.
What are the temperatures in the reactor bottom ?
- Maastricht, The Netherlands
January 13, 2009
A. UREA REACTOR LINING MADE OF SS316L MATERIAL IS PROVIDED WITH AN ON-LINE CONTINUOUS AIR SUPPLY THRU-FEED FOR PASSIVATION DURING OPERATION. AFTER ANNUAL MAINTENANCE AND REPAIR WORK ON THE REACTOR INTERNALS, WHAT IS THE PASSIVATION, IF ANY, THAT IS RECOMMENDED TO BE FOLLOWED (SAY, WITH SODIUM/POTASSIUM DICHROMATE. ETC.) ALONG WITH ALLOWABLE CHLORIDE LEVELS (TO AVOID ANY 'CHLORIDE STRESS CORROSION' AT THE SUBSEQUENT HIGH OPERATING PRESSURES AND TEMPERATURES DURING OPERATION)
K Ram- Chennai, Tamilnadu, India
May 3, 2012
Multiple threads merged: please forgive chronology errors and repetition 🙂
Effect Of Urea Reactor On Cast Iron and Stainless Steel
Q. Hi,
Right now I'm doing industrial training in L&T, Hazira in Gujarat, India. I want to post a question about Urea Reactor as I have done project on Liner Shell Set-up in Urea Reactor. I want to know what will be the effect of Urea reactor on cast iron shell and on stainless steel coating done on cast iron shell. Please answer me as early as possible as I'm on the verge of completing my training.
Thanking you,
Ashish Jain- Chandigarh, INDIA
2003
Q. My company manufactures a system used to hydrolyze urea to ammonia. This is accomplished in a 316L stainless vessel (somewhere between 500 and 10,000 gallons in capacity, depending on need) at roughly 300 degrees F. The process is "dead end" in that a liquid solution of urea is injected, and a mixed gas of ammonia, CO2 and water leaves the reactor. All the non-volatile dissolved and suspended solids stay in the vessel and concentrate there. We are concerned about minimizing the potential for corrosion and have two questions:
1) What possible constituents of water (like chloride and sulfide, for instance) could attack the 316L stainless steel
2) Are there any coatings that could protect the system components from attack by carbonic acid and ammonium carbamate?
Thanks for any help.
Jeffery E. Fisher- Santa Ana, California, USA
2003
A. Chlorine and chlorides are always bad for stainless steel and you are best to keep them out of the bath completely. You can use DI water or filter out the chlorine. Or, at least let the water stand for a period of days before you use it if you are using chlorinated city water.
I do not think you will have any trouble with the carbonic acid or ammonium carbamate with 316 stainless steel. Anything can happen at this temperature long range.
Good passivation of the tank prior to use is important, especially in the weld areas. You can coat the tank with various things, but coatings usually fail long term unless it is a good job of coating with a very tough material. There are good things available. If you are going to coat the tank you do not need to build it from 316 stainless, unless you are planning that the coating will fail.
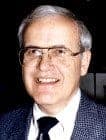

Lee Kremer
Stellar Solutions, Inc.

McHenry, Illinois
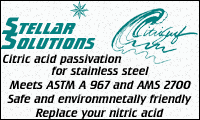
2003
Q. Lee,
Thanks for the input. We appear to have a corrosion problem on the gas side where we have "cold" spots (in comparison to the 300 F gas bulk). The constituents that can come out of the gas at those locations are water (first, since we're close to the condensation point already), anything that might dissolve in the water (NH3 or CO2) and, if it gets cold enough, ammonium carbamate. That's actually a separate issue.
In the bottom of the vessel, where the solids concentrate in the water, we are concerned about stress corrosion, crevice corrosion and pitting caused by what comes in with the water (usually deionized) and urea. So I'm trying to find out if halides in general are a problem, or larger ions like sulphate, thiosulphate, nitrate or phosphate can be a problem. I'm having trouble finding any information beyond the concern over chloride.
Again, thanks for your help.
Jeffery E. Fisher [returning]- Santa Ana, California, USA
2003
A. Sulfides cause stress cracking in stainless steel. Chlorides are somewhat corrosive to stainless steel. The combination is not good.
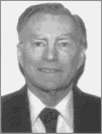
Don Baudrand
Consultant - Poulsbo, Washington
(Don is co-author of "Plating on Plastics" [on Amazon or AbeBooks affil links]
and "Plating ABS Plastics" [on Amazon or eBay or AbeBooks affil links])
2003
A. Check your DI water source and its pH. Usually it is deionized via a pair of catalytic resin reactors which are routinely washed out with hydrochloric acid and soda. Even when fully rinsed they can constitute a source of hydrogen and chloride ions.
Guillermo MarrufoMonterrey, NL, Mexico
2003
A. It sounds like you might be getting a lot of impurities in there from somewhere. Very small quantities of these things (other than halides) are not likely to be very much of a problem, but you need to have an analysis made of the sludge you are getting to determine what all you have in there. Then it will be easier to judge how bad the situation is. With this kind of mix (if you are getting all of those things) you can get a lot of side reactions. If you have that many anions, you will need to get cations from something. It is possible for it to find them in the stainless steel.
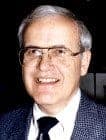

Lee Kremer
Stellar Solutions, Inc.

McHenry, Illinois
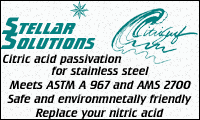
2003
Pinhole corrosion in titanium-clad urea reactor
Q. We have a complaint of a urea reactor manufactured in 1996 which has developed a lot of pinholes in the lower half of the equipment. The equipment has a 5 to 8 mm titanium cladding and these pinholes numbering around 1200 are found close to the bottom dished end.
Nitin JosephTechnology Center - Bombay, Maharashtra, India
2004
A. The problem is very familiar for us. You should reline your reactor and have get rid of your lower plates if they are used. We did it in Russia with good results.
Andrey Igolkin- Russia
2006
Multiple threads merged: please forgive chronology errors and repetition 🙂
Q. We are in the nitrogenous fertilizer business and producing urea, situated in Northern India. In Urea plant, we are having one urea reactor. In this reactor, mixing of liquid ammonia and gaseous CO2 takes place to convert carbamate which further dissociates to form urea having 33% concentration. This reactor is having carbon steel shell with internal lining of SS 316-L (urea grade). Lining is provided so as to protect the shell against highly corrosive urea & carbamate solution. Passivation air (0.3%) is also fed to urea reactor for passivation.
This reactor is of 40-m height and originally was having 10 Nos. of sieve trays (inter-spacing of 2.5-m). Feed to this reactor is liquid ammonia along with Ammonium Carbamate and gaseous CO2. In the year 1996, we carried out some modifications in this reactor for increasing conversion efficiency. As a part of modification, 4 Nos. of additional trays were installed in this reactor. We have been observing that corrosion has taken place in the urea reactor and liner thickness has reduced from original 7-mm to 5-mm. As a precautionary measure, we have increased the passivation air from 0.3% to 0.45% in steps, despite this, we are observing corrosion on the liner and subsequent reduction in the liner thickness.
We seek your valued opinion in the above case and suggest what can be the exact reason for the continuous corrosion in the liner in spite of increasing passivation oxygen into the urea reactor. In case, you need further information on this, please do contact us.
Ajai Dwivedifertilizer company - Lucknow, UP, India
2004
A. You may consider to electropolish the inside of the reactor.
K.de Boer- Heerenveen, the Netherlands
2004
2005
A. Reasons for corrosion may be attributed to
1.Oil content in liquid ammonia feed, as few grades of oil contains sulfur.
2.Chloride in passivation air-seldom present in atmosphere
3.Hydrogen or iron in carbon dioxide feed
4.Holding reactor contents for more than 24 hrs during shutdown - avoid this
5.Poor CO2 purity - less than 98.8%
6.Mole ratio less than 4.0 ; C/N ratio
7.Ammonia liquid feed exceeding critical temp 132.6 °C
8.Excess passivation air as inert
Rule out these possibilities
K S John- S India
A. Holding reactor contents for more than 24 hrs during shutdown or low quality of CO2.
Muhammad Adnan- Pakistan
2005
2007
A. The rate of corrosion may be minimized as follows
- Ensure proper NH3/CO2 ratio
- ensure purity of CO2 (reduce hydrogen & organic matter slipping from CO2 removal section)
- Ensure water contents are within specified range in recycle load.
- After plant shutdown, ensure cut off NH3 feed with 10-15 min delay than CO2 feed.
- During start up introduce NH3 feed 10-15 min prior to CO2 feed.
- Pakistan
A. I personally feel that with the addition of sieve trays turbulence has crossed the limit to avoid corrosion.
Suggestions:
1) Use tube coil bundle instead of sieve trays
2) Use alloy of ss 316-l with Sandvik 2RE 69.
3) Adjust NH3/CO2 ratio in the range of 4.5/1.
- Lahore, Pakistan.
July 29, 2008
January 13, 2009
A. Re. corrosion in reactor in Northern India
Is the liner thickness reduction locally or overall ?
In what time period the reduction took place ?
Is a continuous refreshment of liquid assured between the trays and the liner.
Increasing the oxygen content from 0.3 to 0.45 vol% does not help as at 0.3 vol% the liquid contains already sufficient oxygen.
Pay attention to depletion of oxygen due to dead spots
- Maastricht, The Netherlands
A. Being working on a stamicarbon technology in Urea equipments a simple cause is the corrosiveness of carbamate due to presence of IONIC ammonia which is more corrosive towards Mild steel; however SS can resist it but it will be more more costly.
Simple way is to adjust the N/C ratio 3.1 and second one is the passivation layer presence.
- Pakistan
October 22, 2009
Aging of urea reactor studs
Q. We are a nitrogenous fertilizer manufacturing company located in north India and running since eleven years and since then our reactor manhole cover has leaked twice in 2005 and 2006. We would like to know that whether the problem is occurring due to aging of manhole studs and whether similar problem has been faced by some other organization, we had arrested the leakage online by tightening at 1400 bars earlier it was tightened at 1200 bars, so we would like to know that whether this overtightening will result in elongation of bolts leading to a dangerous situation for plant. Kindly suggest.
Sushil Kashyapkribhco shyam fertilizer, shahjahanpur - India
2006
August 15, 2008
Q. Subject: Failure in HP. Reactor R-101, Urea 1 Plant
Dear Specialists:
We have a Urea Production Plant at Brea Libya. In the Urea plant, we are having one urea reactor. In this reactor, mixing of liquid ammonia and gaseous CO2 takes place to convert carbamate which further dissociates to form urea having 33% concentration. This reactor is having carbon steel shell with internal lining of SS 316-L (urea grade). Lining is provided so as to protect the shell against highly corrosive urea & carbamate solution. Please refer to the technical information below. You are kindly asked to evaluate and recommend your repair procedures of the failure. Below you will find the details.
And answer the following:
General Information:
Vessel Manufacture: VEW Kapfenberg, Austria.
Year of fabrication: 1977
Vessel construction: Single Wall
Liner material: 1.4435
Liner thickness: 7 mm
Shell Material: 1.6368
Shell thickness: 82 mm
Shell thickness on top dome: 60 mm in the drawing (recorded 70 mm on site by UT.)
Design & Operating Temperature: 183 c
Design Pressure: 162 kg / cm2
Operating Pressure: 140 to 142 kg / cm2
Inside Diameter: 2400 mm
Length: 30000 mm
No of trays: 8
Tray Material: 1.4435
Introduction:
During planned turnaround of Urea-1 Plant which started on June 8th, 2008, HP Reactor was offered for internal visual inspection, heavy corrosion of the liner was noted at one of the vertical welds of the top dome (see pictures 1, 2, & 3).
Investigation Actions:
The investigation actions were as follows:
1 The affected liner area was cleaned form Urea carbamate deposits.
2- The linear was found completely corroded at that area.
3- Bigger area of the liner was cut around the affected zone until clean surface achieved on the liner (see pictures 4, 5, &6).
4 Accumulation of urea carbamate deposits and further corrosion was noted on the carbon steel section. (see pictures 4, 5, &6).
5- Further grinding and cleaning of the carbon steel section was done in order to perform UT. and MT.
6- UT. Was done and the thickness recorded was 61 mm (the nominal is 70 mm) meaning that 9 mm were gone.
7- MT .was done, several cracks were noted spread mostly on the affected area. (See pictures 7, 8, 9 & 10).
8- In order to assess the depth of the cracks they were ground about 9 mm and the crack appearance still appear.
9- The thickness of the carbon steel section left after grinding the cracks is 60 mm Min. at the top area up to 40 cm under the top manway; and 49 mm Min. at the area underneath. (See pictures 11 &12).
10- After removal of the cracks final Fluorescent MT was carried-out after 48 hrs and revealed minute cracks (See pictures 13 & 14).
We seek your valued opinion in the above case and suggest:
1. What is the exact reason for damage and cracking in the Stainless Steel liner, and the Carbon Steel?
2. Is this cracking a Hydrogen Damage Crack or a S.C.C.?
3. After removal of the cracks final Fluorescent MT was carried-out after 48 hrs and revealed minute cracks. (See pictures 13 & 14). Can those minute cracks be accepted for safe operation of the plant for one year until we purchase a new reactor?
4. Is the remaining thickness acceptable for safe operation in the plant until we purchase a new reactor?
5. Finally, can we run the plant safely for one year?
Your urgent reply is highly appreciated.
Regards.
NDT Inspector - Tripoli/ Libya
Ed. note: Dear Mr. Omar, we didn't receive the photos you reference. Even so, this is simply a public forum; knowledgable readers may not even stumble upon this page for weeks or months, and can't be expected to reply urgently. Nor will most people make a safety evaluation for free or based on a verbal description. Sorry, but if you need a professional opinion you must retain a safety consultant specializing in that area. Apologies and good luck.
Q. We want to procure stainless steel liner for urea reactor.
Please suggest what are the standard specifications of liner?
What standard test to be performed during manufacturing of SS liner?
What are the ASTM/IS codes?
- Namrup, Assam, India
April 26, 2012
Q. Please anyone explain the reason why Reactor bottling of solution can be done for 48 hours if plant tripped after continuously running of more than 1 week smoothly ... and if the plant tripped before 1 week after plant start up it is to be bottled to a max to 24 hours. What is the reason -- please explain the concept?
Kumar Sourav Duttafertilizer - Durgapur India
July 30, 2014
Q, A, or Comment on THIS thread -or- Start a NEW Thread