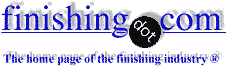
-----
Alternative to hex chromate for brightening
Q. My company uses Ardrox 160 (containing I believe hexavalent chromates) as a brightener for dipping Nickel Aluminium Bronze castings. We have been advised of it's toxicity etc and that an alternative should be sought - Anyone got ideas?
The treatment is specifically to reveal areas of weld metal, and any associated selective corrosion on sea water wetted surfaces so any alternative must do the job not just a general clean.
Thank you in expectation.
Martin RichShip Repair - Plymouth, Devon, England
2004
Q. My company may be forced, through lack of alternatives, to continue using a toxic cleaning solution for brightening copper alloy castings. The solution is Ardrox 160 which we are informed contains hexavalent chromate. Does anyone have an idea how we might treat the solution to render it less toxic prior to disposal when the solution becomes exhausted? Any guidance on alternatives would also be welcomed.
Regards
Martin RichShip Repair - Plymouth, Devon, England
2004
A. Hello Mr. Rich
There may be alternatives worth investigating, like proprietary sulfuric acid - hydrogen peroxide dips. Contact a distributor or manufacturer of plating supplies.
When one uses hexavalent chromate during processing, there are two alternative scenarios. The first is that some of the chromate must stay on the parts, which are then shipped, and people and the environment are exposed to that toxin. An example is the traditional chromate post-treatment applied to zinc plated brackets and hardware. The world is rapidly addressing that problem through end-of-life vehicle standards, etc.
The other scenario is that, although hexavalent chromate was required in the processing of the parts, none remains on the part. An example of this would be chrome plated goods, which can even be safe to eat off of.
I believe the critical issue is whether hexavalent chromate remains on your parts at ship time. To me, shipping parts that have a toxin on them is equivalent to a doctor sending a patient on his way with a virulent contagious disease, whereas ceasing to process parts the best way you know how because there are toxin hazards that must be managed, is equivalent to a dentists refusing to treat a patient with AIDS.
If you determine that there is no hexavalent chromium on your castings, wastewater treatment of hexavalent chromium is really no big deal. There is a reduction step required, where sodium bisulfite is added to the solution to convert the hex chrome to tri chrome, and after that the trivalent is simply precipitated.
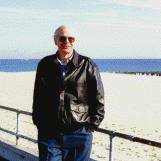
Ted Mooney, P.E.
Striving to live Aloha
finishing.com - Pine Beach, New Jersey
2004
Q, A, or Comment on THIS thread -or- Start a NEW Thread