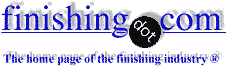
-----
Galvanic Corrosion: nickel-aluminum interface
Quickstart:
Aluminum is often 'chromate conversion coated' as a corrosion resistant final finish or as a pretreatment for painting or powder coating. The process actually involves many steps, usually including alkaline cleaning, etching, deox/desmut, the chromate conversion step per se, and water rinses between each step.
MIL-C-5541 / MIL-DTL-5541 / MIL PRF-5541 is the most commonly cited spec. "Alodine" and "Iridite" are proprietary trade names from two suppliers of the process chemistry. "Chem film" is a slang term for the process often used in the USA.
Q. Hi,
I have encountered galvanic corrosion in the fins of air cooling products. The product has copper and aluminium fin parts soldered together. The fins are made of soft aluminium Al1100, plated with 0.8 µm nickel. One of the steps in the production line is to clean attached copper using acidic solution, followed by passivation with other chemical. During this acid washing step, most of the fins gets corroded (white appearance near fins edges). I would like to know if there is any process to remove those white spots and gets the aluminum shine back?
Also, which acid would be more suitable to avoid this kind of corrosion. Reading your thread, I understood that nickel is a bad choice for plating.
Zeeshan Uddin- Taiwan
November 23, 2022
A. Hi Zeeshan. I suspect that this "white appearance" is corrosion of the underlying aluminum, so I doubt that removal, if successful, would extend the life very much.
Although tin plating would be better than nickel plating in terms of galvanic compatibility with the aluminum, and some acids might be less destructive, I believe that the real issue is that the plating is much too thin. 0.8 µm (0.000032") is less than 10% of the nickel plating thickness recommended for even mild service. In all probability, the nickel plating is porous and pin-holed at that thickness and you are exposing the aluminum to the acid and the copper passivation chemical.
I would suggest experimenting with significantly thicker nickel plating as your first step.
Luck & Regards,
Ted Mooney, P.E. RET
Striving to live Aloha
finishing.com - Pine Beach, New Jersey
Q. Thanks for your response. I too doubted that it is due to plating thickness. Is there any technique to identify pinholes? Can SEM/EDX work?
Zeeshan Uddin [returning]- Taiwan
November 24, 2022
A. Hi again. I suspect that trying to find pinholes via SEM/EDX may be a situation where "you can't see the forest for the trees" might apply, but I have no expertise in SEM/EDX. As previously noted, trying to get by with 8% of the suggested thickness for mild exposure would seem problematic even if you weren't acid-dipping the component :-)
Luck & Regards,
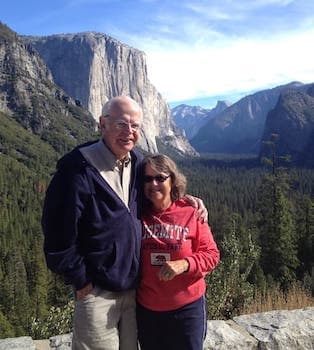
Ted Mooney, P.E. RET
Striving to live Aloha
finishing.com - Pine Beach, New Jersey
⇩ Related postings, oldest first ⇩
Q. Normally, do we need be concerned for Galvanic corrosion between substrate metal and plating layer?
We try to use nickel plating on our aluminum part (6061 or 5052) for corrosion protection. But the position between nickel and aluminum in Galvanic index (anodic index) is quite far. If a galvanic corrosion will happen between them. Normally electrode reaction occurs when water or other electrolyte solution existing as medium to transfer ions. When part was plated, the exterior surface all covered by plating layer. Do we still need concerning Galvanic corrosion between the substrate metal and plating layer?
THANKS A LOT,
Xiaoling Li- Montreal, Quebec, Canada
2003
A. Hi Xiaoling. If the plating is thick enough and high quality enough to suffer no porosity or pinholes, galvanic corrosion is not an issue because the aluminum is completely covered and not exposed to the environment.
However, poor nickel plating would mean that both aluminum and nickel are exposed, and the plating would not prevent galvanic corrosion, so if the environment encourages it you would get it.
Luck & Regards,
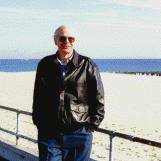
Ted Mooney, P.E.
Striving to live Aloha
finishing.com - Pine Beach, New Jersey
Multiple threads merged: please forgive chronology errors and repetition 🙂
Q. For the purpose of electromagnetic compatibility, I am inserting a gasket between a metal-shelled connector and an aluminum bulkhead. I am aware of the importance of metals compatibility for preventing galvanic corrosion in pairing materials used in electrical shields, but I am not familiar with readily available coatings and processes for producing a low-impedance, reliable connection. The equipment is targeted for a moderate industrial environment (warehouse with no temperature/humidity controls).
The connector shell is tin-plated, as is the gasket --- no problem. The tin-plated gasket mates to an 5052 aluminum bulkhead. The galvanic series charts I have do not specify 5052 aluminum, nor do they list our common coating for aluminum, gold Iridite (Alodine).
Should I mate the gasket directly to the 5052 aluminum? the Alodine? Is Alodine conductive? Can someone suggest a cost-effective solution?
Thanks.
Steve KrupskyIndustrial Control Equipment - Blackwood, New Jersey
2004
A. Steve,
I hope I can offer some words of advice.
For the galvanic series, just try looking at aluminium for the metal to see the voltage difference.
Alodine is conductive but does add a small amount of resistance, however clamped down like you describe should not be a problem -- What I am trying to say is looks like tin to Alodine coated aluminium is sensible and should work but you better do some tests to be sure.
Regarding if you should or should not put on the Alodine coating I would come down on the side of should as without you will get aluminium oxide forming which is non-conductive and for sure this will mess your joint up.
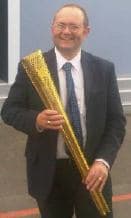
Martin Trigg-Hogarth
surface treatment shop - Stroud, Glos, England
Multiple threads merged: please forgive chronology errors and repetition 🙂
Nickel plated EMI Spring Clip compatible with aluminum?
Q. I have an application that requires an EMI spring clip soldered to a PCB to ground against an aluminum part. The EMI clip needs to pierce through the aluminum oxide via a sharp tooth formed on the clip to maintain an electrical ground connection. For this, we were considering nickel plating on the EMI clip, but nickel is not galvanically compatible with aluminum.
This cannot be the 1st time this kind of thing has been tackled. Is nickel plating the clip acceptable even though the galvanic charts say no?
Thanks,
Michael
Mechanical Engineer - Redmond, Washington, USA
March 24, 2011
A. Hi Michael. Tin would be more compatible with aluminum, and bare steel more compatible still. But many electronic devices do not see environmental conditions that would make galvanic corrosion an issue. It requires moisture and the presence of an ionic salt capable of transporting ions. I'd probably go with tin plating if no automotive or aerospace specification is involved.
Luck & Regards,
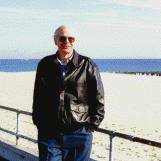
Ted Mooney, P.E.
Striving to live Aloha
finishing.com - Pine Beach, New Jersey
Multiple threads merged: please forgive chronology errors and repetition 🙂
Galvanic Compatibility of Aluminum to Nickel Plated Copper
Q. Need to know what are the effects of Galvanic Compatibility of Aluminum that has been chem-film finished when it comes in contact (attached to) a component that is Nickel plated Copper.
Alan RustQuality product designer - San Dimas California USA
April 15, 2016
A. Hi Alan. The chem-film doesn't hurt, but (at least according to MIL-DTL-14072) it doesn't help either: see Mark Whittum's posting on thread 19266, which I just re-checked and found to be current. So, you are attaching nickel to aluminum, and these are considered galvanically incompatible with an EMF differential of about 0.6 volts. If you are not obligated to conform to a particular spec the issue becomes less clear, of course, as you will see from many threads here about "copper aluminum galvanic" and "nickel aluminum galvanic". Nickel is slightly worse than copper.
We don't know your situation, but if you can tin plate the copper instead of nickel plating it, you'll have a more galvanically-compatible joint. Good luck.
Regards,
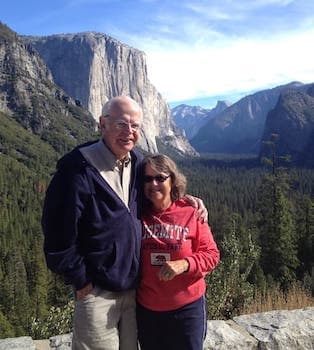
Ted Mooney, P.E. RET
Striving to live Aloha
finishing.com - Pine Beach, New Jersey
Q. I have a flange that is Aluminum chem film finish, and I am attaching it to a flange that is copper nickel plated. Is Galvanic Compatibility at risk or high?
Alan Rust [returning]- San Dimas California USA
April 18, 2016
A. Hi again. I still don't know quite what you are talking about (pipe flange? what is in the pipe?), inside a climate-controlled electronics cabinet, or out on an offshore oil platform?
The short answer is that the materials are highly incompatible and very subject to galvanic corrosion. So, unless it's a dry application in an air conditioned environment, it sounds like trouble. Once again, are you sure you can't change that nickel plating to tin? You could nickel plate the aluminum, but the plating must be heavy (pore-free) and unlikely to be scratched through. Good luck.
Regards,
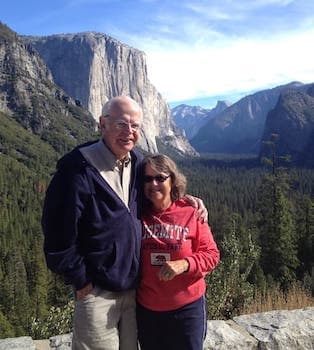
Ted Mooney, P.E. RET
Striving to live Aloha
finishing.com - Pine Beach, New Jersey
Q. Hello,
I have a flange that is Aluminum chem film finish, and I am attaching it to a flange that is copper nickel plated. Is Galvanic Compatibility at risk or high?
they are RF flanges on a unit that goes in the tail of a air craft. WR-28 & WR-42.
I was told as long as the two different metals were plated there should not be any galvanic corrosion; this is why I put it out there for more information.
Thanks for your help.
Alan
- san dimas California USA
May 2, 2016
A. Hi Alan. If the two flanges are plated with the same metal then there would be no galvanic corrosion because no other metal would be exposed. I think you may be misunderstanding what you were told about this, or the person who told you misunderstanding what he was told and leaving out a critical part of the statement.
For a galvanic current to flow and corrode something requires:
a. Two different metals with different positions on the galvanic series (the further apart they are, the more powerful the battery they create).
b. The two metals must be in metallic contact with each other so electrons can flow from one metal to the other. If insulators prevent metal to metal contact, electrons can't flow
c. A wet conductive situation that allows metal to ionize into solution.
If conditions "a" and "b" exist, electrons will want to flow from the more active metal (aluminum) to the more noble metal (nickel), but as long as condition "c" is not met, the circuit is not complete, so they can't. If condition "c" becomes met, the circuit becomes complete because electrons can flow from the aluminum to the nickel through the metal, and the aluminum atoms, now stripped of an electron, dissolve into solution as positively charged ions and migrate over to the nickel to recapture those electrons. So the aluminum corrodes.
As mentioned, aluminum and nickel are far from each other, so unless freedom from moisture is assured, this is a galvanic problem. Sorry, I don't know enough about RF flanges and aircraft fitting to know whether this is a problem or not.
Regards,
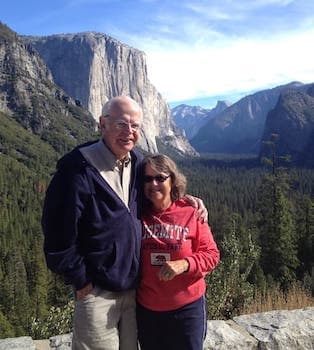
Ted Mooney, P.E. RET
Striving to live Aloha
finishing.com - Pine Beach, New Jersey
Q. Hello
I am a biomedical engineer. I am working on designing a PCB with with three USB connectors which are nickel plated. I want to use a sheet metal as shielding/protection for EMC (electromagnetic compatibility) purposes. The sheet metal component is screwed to the Aluminum (6082) enclosure while its three wings/arms are in contact (touching) the nickel-plated surface of three USB connectors.
What material can be used for sheet metal component so that it can be galvanic compatible with both Aluminum and Nickel-plated surfaces of USB connectors?
Note: The end use environment will be general indoor environment in humid countries such as India.
Any feedback or comment is appreciated.
- Eindhoven, North Brabant, The Netherlands
November 25, 2020
A. Hi Sepanta. If I am understanding your description, you have a galvanic compatibility issue no matter what conductive material you make the sheet metal shielding of because you are providing a metallic path from the nickel plating to the aluminum. But I'd probably tin plate it. Tin falls in between aluminum and nickel in the seawater series.
Luck & Regards,
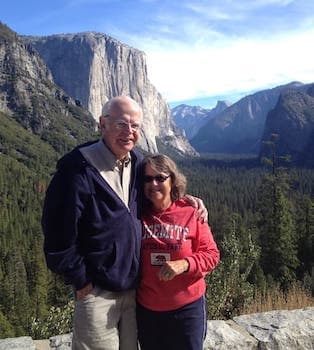
Ted Mooney, P.E. RET
Striving to live Aloha
finishing.com - Pine Beach, New Jersey
Q. Hi Ted
Thank you for your comment. Given the current circumstances and lack of options for changing other mating materials, I think the Tin is my best option to go for plating. As you mentioned it falls between Nickel and Aluminum.
Do you perhaps have any impression of how long it may take for the corrosion to take place and becoming an issue in this case. I understand that this can depend on several factors. A wild guess would also suffice. I appreciate it.
Regards
Sepanta Fazaeli [returning]
- Eindhoven North Brabant The Netherlands
November 30, 2020
A. Hi again. It depends on the smoothness of the sheetmetal (which helps reduce porosity and pinholes) and the thickness of the plating, as well as the environmental factors, but tin plating is very widely used in electronics work of all sorts; it's not uncommon to finish up with a chromate or other tarnish inhibitor.
Luck & Regards,
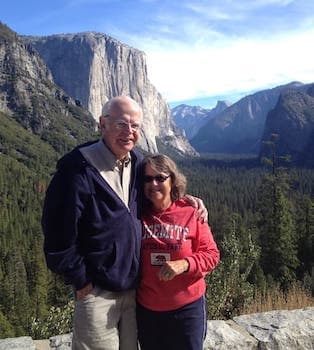
Ted Mooney, P.E. RET
Striving to live Aloha
finishing.com - Pine Beach, New Jersey
Q, A, or Comment on THIS thread -or- Start a NEW Thread