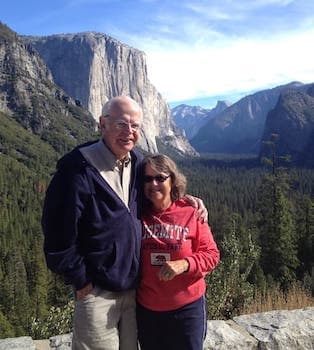
Curated with aloha by
Ted Mooney, P.E. RET
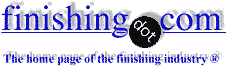
The authoritative public forum
for Metal Finishing 1989-2025
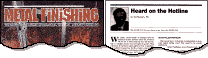
-----
Bare areas on ENP plated castings

Q. Hello,
I am a Lean Manufacturing Engineer for a company that makes in flight re-fuelling products. The problem in question is that we have a product that is made from a casting (material L169) and is ENP plated. After the plating process has taken place we have areas on the casting that have not been plated, it is almost as if the plating has 'soaked' into the casting in certain places. Has anybody else experienced this problem or does anybody have any suggestions as to what may be happening. I am by no means a plating expert so if more technical information is needed about the plating process that we are using please let me know and I will find out.
Many thanks in advance.
Rob Marshall2004
re-fuelling products - Verwood, Dorset, UK
![]() |
A. Your area of no plate is probably a recessed area which is an area of low current density and is surrounded by an area of high current density. The higher the current, the more plate. Another possibility is that it is trapping air or gas bubbles that is displacing the plating bath and thus a decreasing plate. What you need is a consultant that can look at your process and parts. That person can then sort out what your problems are. (you will very probably have more than one) Corrections may be racking, aux anodes, shields, robbers, chemistry, temperature and agitation as the most likely probabilities. James Watts- Navarre, Florida A. L169 is an aluminum cast alloy and it can contain defects, pores and a vast number of contaminants over its surface (release agents, debris from mould, sand if cast in sand moulds, etc.). On the other hand, it is well known that aluminum requires more attention and a carefull zincate pretreatment. You did not describe your process sequence, nor details of your parts so we can only speculate. Guillermo MarrufoMonterrey, NL, Mexico |
Q, A, or Comment on THIS thread -or- Start a NEW Thread