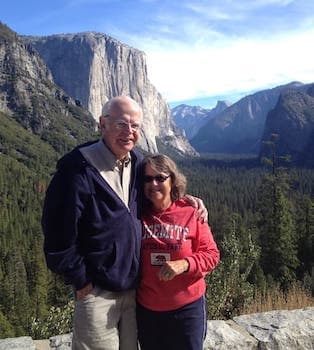
Curated with aloha by
Ted Mooney, P.E. RET
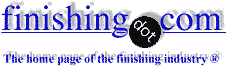
The authoritative public forum
for Metal Finishing 1989-2025
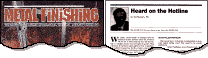
-----
Solutions to heat loss from plating/rinse vats
2004
We are a surface treatments engineering company in the civil aerospace sector. As environment officer I am responsible for energy policy.
We need to reduce heat loss from our plating/ rinse vats but our operators are not keen on croffles (hollow plastic spheres). They complain they get stuck in jobs whatever the size and represent a house keeping problem. Are their any other equally simple products available that do the same job but don't have the downsides?
Regards
Chris Jockelaerospace surface treatments - Stroud , Glocestershire , UK
2004
Hi Chris, What a helluva weird name, CROFFLES! Yuck.
There are, as someone else more qualified will tell you, liquids that one cautiously covers the tops of the liquid with to reduce heat loss. They cost $. And one person said that there are some negative side effects ... but then I'm no plater.
Re your heat loss, one of the problems with the hollow spheres is that sometimes they sink .... one Indian came up with a solid shape, made of PP, I believe, which should partially solve that problem ... what did he call it? A Flying Saucer? ... but not a waffling croffle, that's fersure.
Sometimes you have just have to put with inconveniences especially if they contribute to reducing heat & fume losses.
The smaller 'spheres' or hollow balls would be more of a pain in the neck ... but can't you get them to 3" diameter?
I'm a great believer in reducing heat losses so you have the following options a) reduce your airflows b) improve your hood design to allow for adequate capture but to still reduce the airflows c) have a hinged flip-flop lid and lastly ... d) Have a BAll .... ie. many of them!
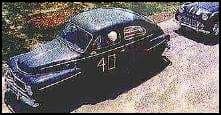
Freeman Newton [deceased]
(It is our sad duty to advise that Freeman passed away
April 21, 2012. R.I.P. old friend).
Freeman forgot to mention one of the most obvious solutions to your problem. All of our heated/chilled tanks are insulated, and covered at night (when not in use). While its difficult to come up with an exact savings cost, I'd did a little experiment recently. I turned our 150 degree NaoH tank off after our shift, and covered it. When I came in the next am (almost 16 hours later), and turned it on, I had only lost 14 degrees (136). These are all poly-pro tanks that are wrapped with insulation, and then "skinned" with another layer of poly pro.
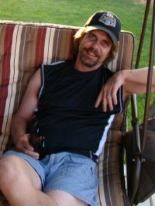
Marc Green
anodizer - Boise, Idaho
2004
In addition to the previously listed mechanical methods, some plating solutions lend themselves to the use of surfactants which will form a foam blanket and retain heat. Consult with your chemistry supplier and see if any are applicable to your uses.
Gene Packmanprocess supplier - Great Neck, New York
2004
As Freeman mentioned, covers can drastically reduce heat loss. I use them every day on my coffee cup. Covers have other advantages as well to offset their initial capital cost. Covers help reduce fugitive emissions and reduce cross contamination between baths. If the hoist is automatic, then covers can be automated as well to reduce the overall CFM requirements (fan size, pump size, make up air size) for the line by more than 75%. That leads to tremendous annual energy savings, which can pay for the covers in short period of time. We did a recent study of heat loss on a covered v/s uncovered tank. The customer had a $2,000 yearly savings on his electrical bill with the covered tank. That # only includes the kW reduction for one tank.
Kyle Hankinson- Forest City, North Carolina
2004
2004
Hi Chris, again !
I forgot something ... well, it may be more pertinent to Canada (i.e., c o l d e r winters) than the UK.
This occurred at Court Industries in St. Catherines, Ontario, a hard chrome plater of some renown. They have highish ceilings. Heat rises. Then, that year the energy/heat prices rose ... but theirs DIDN'T.
You may be familiar with greenhouse ventilation. They use a push fan onto which is a long, very LONG el-cheapo floppy Polyethylene bag or tube. This has holes punched in it. The design concept is that the number and size of the holes equals, say, an outlet velocity of around 2,000 fpm. What happens then with a, say, 40 foot long flexible bag is that the entire bag OPENS UP and the air, push air, is evenly distributed ... in Court's case, the holes would be probably vectored downwards.
ERG0 .... happier workers as the high level 'hot' plant air was pushed downwards and evenly distributed.... and a reduction in the plant heating costs.
I have recommended this usage to some Companies but forget where. A super idea. Mind you, surfactants help (if they don't, cause, I'm told, sometimes deleterious effects), ditto for insulated tanks AND covers. .... May you have a ball (3" dia, perhaps?) !
P.S. Something suddenly dawned upon me ... something that will have or can have some people up in arms!
What about recycling the air? Yes, this has been done and one Canadian hard chrome plater is NOW using this ... albeit NOT using a conventional mass transfer scrubber but one of my LMITS ... in his case it was an S-LMITS. This consisted of two banks of highly efficient mist eliminator blades adjoined to some mesh and followed immediately by another blade bank. The two banks approach, a CT-120/2 I dub it, was tested in Vancouver in the early 80's as being 30 times LESS than the then allowable emissions of chrome sulfuric, ie. 0.35 versus max. 11 grains. But in EPA terms this only works out to 0.700 mg/M3 but full acid recapture was achieved DRY .... but by adding on the above mesh coalescing fully sprayed approach, then the EPA specs of 0.050 mg/M3 have been met.
I would NOT recommend this approach for any nitrics. One of my first ever LMITS was for air recycle of chromic but how successful it was, I never found out. The 2 bank approach is for 12 micron capture, the LMITS is for 3 micron capture ... but on one test (INCO # 2 research in Port Colborne, Ont) they said that in that sulfuric spectrum it attained 86% efficiency for a 0.2 to 0.8 micron range, albeit using Na0H washdown.
Food for thought. ,,, and long live the 4th Glosters!
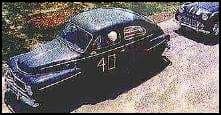
Freeman Newton [deceased]
(It is our sad duty to advise that Freeman passed away
April 21, 2012. R.I.P. old friend).
Q, A, or Comment on THIS thread -or- Start a NEW Thread