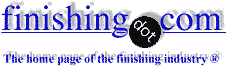
-----
Looking for an application or treatment to steel to resist friction marring
2004
I am looking for an application or treatment to steel that will resist marring of other steel that is running against it.
What I have is continuous strip steel that is being fed into a machine. The strip steel currently is guided through the machine with a series of rollers. Problem is, the oil and shmootz thats on the strip steel gums up the rollers, causing them to freeze.
I have attemped to replace those rollers with a spring loaded stationary guide plate. However, my new problem is that the strip steel has continuous scratches. We had considered using something like HDPE pads on the stationary guide plate, but they wear out too quickly. Any thoughts or information on applications would greatly be appreciated.
Tom Beyreis- Wheeling, Illinois, United States
Try large rollers, maybe a foot in diameter. That will allow you to have their axles far enough away from the work to fit in some shields. Also could try some dust covers over the bearings, similar to what you find covering automotive wheel bearings.
Tom Gallant- Long Beach, California, USA
2004
Try a wiper system made of suitable rubber-like wipers to remove debris from steel rollers.
Guillermo MarrufoMonterrey, NL, Mexico
2004
2004
Thanks for the info so far. First, the entire assembly that houses these rollers is 8 inches in length, 5 inches deep, and just over 4 inches in height. The "rollers" are double sealed abec 1 bearings. We have tried using wipers to clean the blade before it enters the assembly, but the oil is particularly sticky and does not really "wipe" off. And, the space is waaay too small to be fitting large rollers as suggested.
As an update, I am attempting to use carbide that fully supports the blade, and an oiler. The attempt is to make some sort of friction barrier (similar to that of a piston running in a cylinder) that the material can run on without actually contacting the carbide. So far, the results have been so-so, as I also have to have a force that "pushes" the strip down onto this surface (thus squeezing out the oil and creating a suction contact). I will keep you posted, and keep the suggestions coming as I sure could use them!
Tom Beyreis- Wheeling, Illinois, USA
What I understand is that to kill this problem the oil should not travel between the rollers at all. Introduce an oil wiping mechanism before the strip enters between the rollers. After the rollers , introduce an oiling mechanism for strip. This way a very little amount of oil will travel between the rollers , hence increasing the life.
SHARAD GUPTA- Faridabad, Haryana, India
2004
You could always try coating the rollers with a PTFE baked on that would allow a non stick surface. Certain coatings available have molybdenum disulfide added as a secondary lubricant which can help with the sharp surface. Plates used in the breweries have been coated where the bottles run and spin along. Uncoated plates show definite 1/8" deep grooves after 3 months. Coated plates last about 1 year.
Wayne McKee- Mississauga, Ont., Canada
2004
May I suggest a profiled roller with a series of "V" cuts to minimize contact surface between the strip steel and the roller and that provides a path for this debris to collect. Along with this configuration, include a profiled scraper that form fits this profile to clean the grooves of the "V" cuts in the roller. Position this scraper horizontally, 90 degrees before strip contact. This will provide a surface for this debris to accumulate and be scraped away periodically. I believe that the problem occurs due to the debris build-up on the roller surface. This debris collects up to sufficient quantities and "stalls" the roller due to this contamination. The rollers must be free to rotate, therefore use quality precision double sealed bearings to support it.
Eugene Sessa- Harrison Twp., Michigan
2004
What about powering the rollers? If you can keep them moving and maybe add a wiper at the bottom to keep them clean you should be able to at least not get the long scratches you get now. If you do use powered rollers you can go to hard rubber on the top for a more forgiving system...?
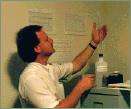
Jeff Watson
- Pearland, Texas
2004
Could you maybe use blocks of UHMW plastic in place of the rollers? The oil shouldn't affect them. The plastic won't mar the steel. I don't know how much pressure is involved, but for just guides, I would think that it would be reasonably durable as well.
Shane Harris- Indiana
2004
Q, A, or Comment on THIS thread -or- Start a NEW Thread