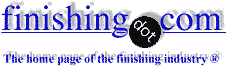
-----
Tank Material for Nitric Acid/ Sodium Dichromate Passivation
We have a requirement to passivate 303 stainless steel to Federal specification QQ-P-35C (canceled) [link is to free spec at Defense Logistics Agency, dla.mil]. We are using a 25% nitric acid and 2- 4 oz/gal sodium dichromate bath at 120 degrees F. The government specifications cover the process but don't say much about the tank material. We are currently using a PE tank. compatibility tables show that nitric acid in this concentration is only marginal compatible with PE. I am concerned that the nitric acid may attack the plasticizers in the PE and cause cracking. Can someone give me recommendations about the best tank material to use for this bath?
Paul SchendelerRadio Frequency Coax Connectors - Rock Hill, South Carolina
2004
A. 316L S.S. would be my choice.
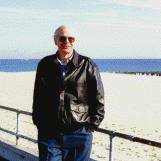
Ted Mooney, P.E.
Striving to live Aloha
finishing.com - Pine Beach, New Jersey
2004
A. Hi Paul:
You say you are using a PE tank, I assume that this is a moulded tank.
If this is the case, then the process is called the Engle process, in which case, one can increase the wall thickness to around 1/2"
The advantage of this, which does not cost very much because the manufacturer just uses more resin, is that the life expectancy in an oxidizer jumps up enormously
What you must NOT do is to do any welding. For any outlets you must use tank adapters (sometimes called bulk head adapters) which are available in PVC but just make sure that the O-rings are compatible, either flexible PVC (but not neoprene) or you could use Viton.
Another alternative is to use a dual laminate using PVC or, if you want to spend money, PVDF. Dual laminates are very superior materials because the bonded fibreglass outer surface enhances structural strength, reduces thermal expansion and increases temperature deflection.
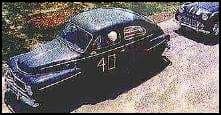
Freeman Newton [deceased]
(It is our sad duty to advise that Freeman passed away
April 21, 2012. R.I.P. old friend).
2004
Q. If we use 316ss tank for nitric 20% and sodium dichromate 2% do we still need to ground it if we do not have any heat on it?
Micheline Forth- Rincon, Georgia USA
February 2, 2017
A. Hi Micheline. I am not personally aware of any building codes that call for tanks to be either grounded or isolated from ground. Decades ago it was standard practice to either use fiberglass base beams, or a sheet of PVC between the tank bottom and the base, and just set the tanks on it so they were electrically "floating". But as design for earthquakes became more common, and concern for floor spills more necessary, I personally got into the design habit of bolting the tanks down but always using fiberglass base beams to retain the electrical insulation.
But I would think that if non-electrified tanks were really and truly effectively grounded, stray currents, galvanic corrosion forces, etc., would not be an issue. So my answer, pending any conflict with codes that you might discover is: I'd prefer isolated, but certainly no halfway measures, either isolate them or ground them very reliably :-)
I'd be happy to hear other opinions as I don't do design or consulting anymore and my knowledge might be becoming dated.
Regards,
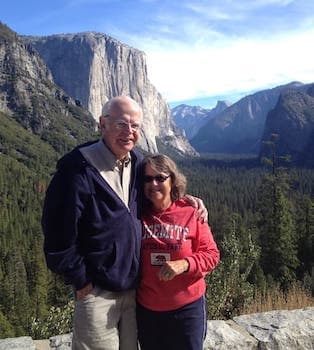
Ted Mooney, P.E. RET
Striving to live Aloha
finishing.com - Pine Beach, New Jersey
February 2017
A. I completely agree with Ted on this. Usually, we specify welded grounding lugs on metal tanks.
Lyle KirmanConsultant - Cleveland Heights
February 3, 2017
Q, A, or Comment on THIS thread -or- Start a NEW Thread