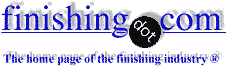
-----
I need advice on a rust inhibitor and need to know about autophoretic coatings
What is the process for autophoretic coatings. I nickel and chromate hose couplings for overseas shipments and need a coating for a rust prohibitor that can stand up to 36 hours in a salt fog test chamber. The oil we use now is causing organics to build up in our rinse tanks from the dragin. We coat the parts after the plate process in the oil , which tends to stay on the racks after we let them drip off, to some degree. What we need is a rust inhibitor that doesn't require as much to be applied or something that will chemically bond to the parts after the plate is on. Thanks for your help. By the way, Ted Mooney referred me to a man named Phil Johnson. If you are reading, please advise.
James D. Browning- oxford, missisippi
1999
I don't know if it is a typo, because it is possible to nickel and chromate parts. On steel parts, certainly on porous steel hose couplings, it is sometimes beneficial to dip plated parts in a hexavalent chrome solution to temporarily passivate porosity of the steel. But if you need so much oil, your plating must be thin, or the surface of the parts is very rough indeed.
But if you meant to say nickel and chromium plate, I wonder why you would need so much oil to extend the salt spray resistance. Is nickel/chromium/oil/wax/etc. the right choice for these parts in the first place?
How about a nice, solid, zinc and iridescent chromate instead? Or if you need a blue color, a heavy zinc with a leached yellow chromate.
It is an extra step, but the oiling should be done offline in a basket so you do not contaminate the plating line.
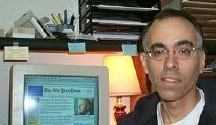

Tom Pullizzi
Falls Township, Pennsylvania
1999
Thanks for the response. The problem we would run into with dipping off to one side would be the dragin we are still having would still not be eliminated and our already stretched time frame would run over into overtime we would like to eliminate. (By the way, it was a typo, sorry.) Our parts are usually smooth but semi-rough depending on how well our basic parts start out from the presses and extrusion process. Our customer has let us know that the saltwater from shipping overseas tends to cause rust even with the chromium plate at times. There are other plate methods I agree, but our customer requested this process and we are pretty well stuck with it. If you have any other ideas I would like to hear them. The ones mentioned were great advice. Thanks again.
James D. BrowningOxford, Mississippi
1999
You need to provide a better nickel-chrome plating finish. The best of them can withstand that many hours of CASS or Corrodkote exposure, which are far more severe tests than neutral salt spray, without any protective oil at all.
But I have to agree with Tom that the oiling should be done offline even if inconvenient. You are putting something on the parts and racks that you want to be capable of standing up to an aggressive environment, then you want to know how to painlessly remove it with no mess. It's not going to work out that way.
Autophoretic coatings, a product of Henkel, are similar to electrocoating but without the need for the electricity. They are a paint-like organic finish, and considering your customer's spec they don't sound applicable to me in this case.
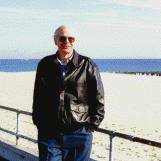
Ted Mooney, P.E.
Striving to live Aloha
finishing.com - Pine Beach, New Jersey
1999
Thank you for your input. Any other thoughts will always be appreciated. Thanks again.
James D. Browning- Oxford, Mississippi
1999
Q, A, or Comment on THIS thread -or- Start a NEW Thread