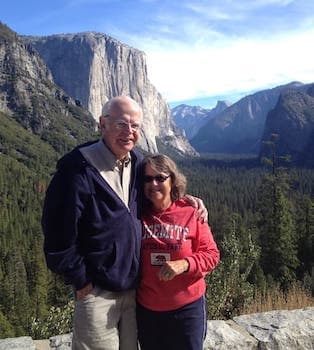
Curated with aloha by
Ted Mooney, P.E. RET
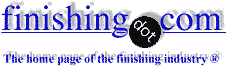
The authoritative public forum
for Metal Finishing 1989-2025
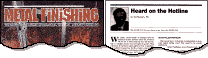
-----
Powdercoat Blistering on Zinc plus Chromate
Q. I wanted to know the pros and cons of powder coating over parts that have been zinc plated and chromated. Benefits? Problems?
John petro- Reading, Pennsylvania
1999
A. Hi John.
Powder coating offers generally better corrosion resistance than zinc plating because the powder coating is an organic topping which encapsulates the part and thus stops (or greatly slows electrochemical corrosion), whereas zinc plating is a sacrificial coating which slowly dissolves away until it's gone and the underlying steel is exposed.
On the other hand, it is much harder to scratch through and breach a metal plating than paint. And even if you do breach the plating, the surrounding zinc plating will sacrificially protect the steel like zinc anodes protect a steel hull boat (please take this as a reduced tendency to rust rather than as a guarantee of perpetual freedom from rust).
The benefits of combining the two would be that you get the corrosion protection of zinc plating and chromate plus that of powder coating.
The problems would be the extra cost of doing both zinc plating and powder coating, and some potential incompatibility problems that are addressed in this letter, letter #2922, and some others revealable by a search of the site. Good luck.
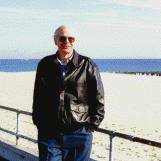
Ted Mooney, P.E.
Striving to live Aloha
finishing.com - Pine Beach, New Jersey
Powdercoat Blistering after Zinc Chromate Undercoat
Q. Hello, We apply a yellow zinc chromate finish to cold rolled steel parts before powdercoating with a TGIC-Polyester powdercoat. This is done for corrosion resistance, in our tests this combination was better by far than using a zinc-rich powder undercoat or a zinc-phosphate undercoat.
The problem we are having is the powdercoat is bubbling on some parts. From stripping the parts, it appears that the problem is related to the zinc finish. Has anyone had a similar problem?
My plater says there is no problem and if there is it must be the powdercoating. My powdercoater believes that it is the plating, and I agree with him, because the problem appears to be batch dependent (coming from the platers).
Thanks for your help.
Craig ChristensenCampbell Scientific Inc - Logan, UT, USA
2000
![]() |
A. Craig...it would appear that you have moisture/solvent on your substrate and/or in your powder. Trying one or both of the following might put your finger on the culprit; 1)recoat the same part after stripping and drying,hopefully the heat history from the previous cure schedule will have eliminated the problem liquid if it was in the substrate and the next coating will be trouble-free. 2)coat another substrate(without plating) of similar size or weight with the same powder and same cure schedule. If the problem is in the powder, then the problem should occur on the new substrate as well. Good luck. Manuel Tyler- Augusta, Georgia 2000 A. We have found that the problem you are describing is a shared problem between the paint and the plating. We successfully (without fail) powdercoated pre-plated (electro-galvanized) metal for years and then switched to zinc with yellow chromate due to customer design changes. Ever since we changed to the zinc/chromate process (using the same paint), we have had a miserable throughput due to paint outgassing/blistering. We believe there is a chemical reaction occurring between the plating and certain types of paint. Our worst failures are occurring with zinc/gold chromate & semi-gloss polyester powdercoat. We have not had any failures with clear chromate using the same paint nor have we had any failures with zinc/gold & textured paint. The platers claim that there is a higher water content in the gold. Chromate begins to evaporate (dehydrate) when elevated above 150 °F. Knowing this condition, we are confident that the chromate is outgassing through the paint. There are 2 solutions: Test the clear chromate. If successful, get your customer to change the color. Ask your powder supplier to formulate an anti-gassing additive to your powder. We are using this with Cardinal and the throughput has greatly increased. Kriss SteinAccurate Metal Fabricators - Seal Beach, California 2000 |
A. I read the previous three threads and wanted to add a few tidbits.
I zinc-chromate plate parts frequently and the process may give you a clue as to why it is behaving as you see. If you are going to just chromate plate a part you can plate as thick as you choose to suit your needs. If you are going to subsequently zinc chromate color it, you need to give it a thicker plate as the zinc coloring is actually an acid etch. This tends to remove a bit of the chromate layer. The deeper the color desired the more is etched away.
To stop the etch the part is rinsed in distilled water and the process is complete. Any water from the chromate process MAY be trapped under the zinc finish. I say may, because I only suspect this from your problems. By heating the part in curing the powder coat, the moisture may be released. I suspect something else may also be happening. The zinc color as I said is an acid etch with a water rinse. If there is any residual acid on the surface it is also feasible that it might also be released during the heat cure. I would be more inclined to think this is the culprit as opposed to water. If water were outgassing it would occur at 100 °C and you're going to what, 175 °C? I would imagine the water would be outgassed well before the polymers even began to set-up. Water in minute quantities shouldn't blister the coating other than possibly causing a blush. Acid however could conceivably damage the polymer coating and wouldn't completely go away till a much higher temperature.
So what to do? One thing to try might be to bring the part to about 115 °C after the initial chromate step and hold it for awhile to dry the part out. Secondly after the zinc etching and rinse with distilled water bring the part up to the cure temperature you are using for your powder coat. Hold it there for a time and then as it cools to around 100 °C rinse with boiling water to remove any residual acid.
This would obviously add a cost to your overall process and maybe you might want to consider other substrate options. But if it is critical to use a zinc chromate then this may help with your problem.
Good luck!
- Buffalo, New York
Blistering of Powder Coating on a Zinc Plated surface
Q. We have experienced an issue with powder coating over a zinc plate with yellow chromate. The defect is blistering which occurs immediately and also after 48 hours room temperature. I have been advised that this is not unusual and the reason is the hydration condition of the chromate. Is this correct? If yes, what is the solution to this problem? Thanks for your responses.
Carol Shibles- North Andover, Massachusetts
2002
A. Carol,
We also powder coat over zinc with yellow chromate, and have problems with Blistering and out-gassing. The blistering in most cases seems to relate to a problem with the plating: poor preclean, or plating too thick, and can be seen easily by removing the powder coat and checking to see if the plating is still intact. The out-gassing is different, the powder coating has what appears to be tiny eruptions in the surface from the gas exiting the part and bubbling in the surface of the powdercoat while it is in it's liquid state. When the powder coat is stripped on these parts the plating still looks good.
Although I do not have anything conclusive, we have gone as far as have a nickel strike (2-3 microns) put on the base metal and then put the zinc over top of it. This is just my opinion but I think this levels the surface of the base metal, filling in any tiny voids that may trap moisture that would be released when the part is heated. Another cause of this out-gassing can be not enough time between plating and powder coating, causing the moisture in the chromate to pass through the powder as it is in the liquid state. We have had some success with running the parts through the cure oven before we powder coat, thus dehydrating the chromate.
Hope this helps.
Regards,
Kevin Davis- Versailles, Kentucky, USA
2002
Blister after powder coating on zinc chromated surface
Q. Dear sir,
We have some blister problems on components. The process sequence as follows :- Base material mild steel => cyanide zinc plating => yellow passivation => powder coatings. Blister appears on the component after Neutral Salt Spray test and also it shows lesser salt spray life (250 hours),whereas requirement is 480 hours minimum. How to eliminate blister problems and how to increase salt spray life to more than 480 hours? Is any intermediate coating required to adhere the powder coating to the zinc chromated surface or any sealant required.
Ashok Nalawade- Mumbai, Maharastra, India
2003
A. Apparently your yellow chromate is too heavy and when you cure the powder paint the heat dehydrates the chromate. Try putting on the chromate very lightly, just barely get a light yellow hue.
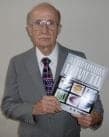
Robert H Probert
Robert H Probert Technical Services

Garner, North Carolina
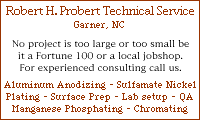
2003
2003
A. If you replace the yellow chromate by a filmogeno fosfation, that contributes great adhesion to painting. That way we will eliminate the Cr VI of its passivation. Also I change the bath of Zn Cyanided by another free of cyanided. Another suggestion is to change all the process by a covering (plate) of Zn/ni with free passivation of Cr VI; the adhesion of the paint will increase formidably. I feel my poor English.
A best regard.
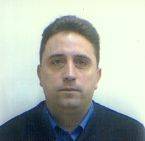
Miguel Angel Martín
surface finishing shop
Madrid, Spain
Great point Miguel! Zinc electroplating usually gets a chromate conversion coating to maintain the corrosion resistance and good appearance of the plating ... but if the item is going to be powder coated rather than remain bare, phosphatization can probably be a better approach than chromate conversion coating.
Regards,
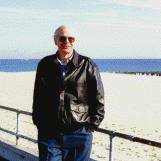
Ted Mooney, P.E.
Striving to live Aloha
finishing.com - Pine Beach, New Jersey
Q. How long does it take Clear Zinc Plating on steel to complete its out-gassing if it is not Baked?
Allan WrightSheet Metal Fab - Austin, Texas
2004
2003
Q. I need advise on the best process for powder coating over clear zinc (zinc chromate). We will build a product out of Hot Rolled Pickle and Oil (HRPO), send it out for clear zinc plating, and then powder coat over the clear zinc.
Questions...
A. What is the best wash method/pre-treatment of the clear zinc part before powder?
B. Is adhesion best on clear or yellow zinc?
C. Is salt spray best on clear or yellow zinc?
D. What questions or instructions should I discuss with the plater?
- Monticello, Indiana, USA
A. Hi Rob.
A. Mild alkaline cleaning is probably all you should do to avoid damaging the chromate. In turn, this means that you should do the powder coating in relatively short order (maybe 24-48 hours after plating) to minimize the handling, aging, and potential soiling.
B. Adhesion is probably better on clear chromate than yellow chromate because it is thinner and less likely to shear.
C. Salt spray resistance will be best for the yellow zinc because it contains more hexavalent chromate.
D. General questions on this subject have been perennial, and for good answers to them you may wish to review the rest of this letter, and search the site. Good luck.
Regards,
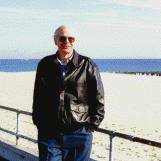
Ted Mooney, P.E.
Striving to live Aloha
finishing.com - Pine Beach, New Jersey
2003
----
Ed. note Dec. 2014: These days most chromating is trivalent (for RoHS compliance) and most trivalent chromates are clear. So when you see yellow chromate these days, chances are good that it is just dyed and has the same corrosion resistance as clear chromate.
Multiple threads merged: please forgive chronology errors and repetition 🙂
Adhesion problem in powder coating on zinc plated product
Q. Dear sir
My problem is powder coat adhesion problem over zinc plate blue passivation.
I want zinc plating with blue passivation before powder coating because I am coating only outer surface of component ... inner surface I can't coat due to CE test getting failure; for same reason I can't go for phosphating.
regards
ELECTRONICS - Bangalore, KARNATAKA, INDIA
2005
Q. Dear sir
Before powder coating on mild steel (CRCA) shall we can go for zinc plating (blue passivation) YES or NO?
YES Means what type of Zinc plating
NO Means why ?
ELECTRONICS - Bangalore, KARNATAKA, INDIA
2005
A. Dear friend,
You have put two different questions.
First of all you can do a powder coat on the zinc plating. But blue passivation means you have converted the zinc into zinc chromate. Zinc chromate coating will have lesser adhesion than your plain zinc plating.
If you have done this zinc plating through a commercial zinc plater, please check with him whether he had given you a lacquer coated blue passivation. If the passivation is lacquer coated, then the situation becomes worse for adhesion of your powder coating.
You can try powder coating with only zinc plating without passivation and lacquer coating.
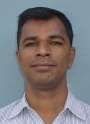
V. G. Rajendran
- Trichy, Tamilnadu, India
2005
A. Hi. Virtually anything is possible with sufficient funds, but it may not be economically practical. For example, if you can afford the masking effort, you can plate the inside surface with zinc and blue chromate for your test, while phosphating and powder coating the outside. Or you can phosphate the whole component, powder coat the outside, and use the powder coating on the outside as the mask for plating only the inside.
But the most practical approach is probably to zinc plate and chromate the whole component, and heed VG's advice to make sure the plater doesn't use a lacquer topcoat. Many shops powder coat their zinc plated and chromated components, and it can be done with reasonable reliability. Good luck.
Regards,
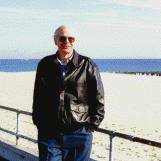
Ted Mooney, P.E.
Striving to live Aloha
finishing.com - Pine Beach, New Jersey
(you are on the 1st page of the thread) Next page >
Q, A, or Comment on THIS thread -or- Start a NEW Thread