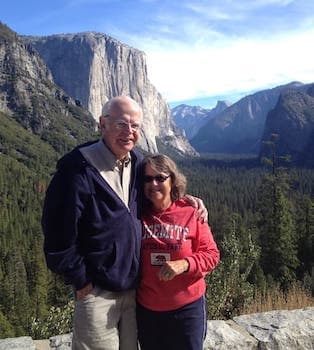
Curated with aloha by
Ted Mooney, P.E. RET
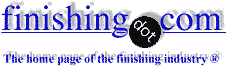
The authoritative public forum
for Metal Finishing 1989-2025
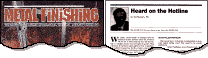
-----
Stainless Steel Corrosion Woes
We are a stamping house that is currently producing a perforated 304 SS part that is passivated at the final stage. We have successfully produced nearly 10,000 parts and suddenly we have been informed that around 30-40 parts are experiencing a great deal of corrosion 1-2 weeks after the passivation process. We have done humidity and salt spray testing on these parts in the past and were successful on each occasion. What could be causing this type of reaction and how can this be prevented?
Shawn Wiglesworth- Lexington, Kentucky
1999
The first thing is probably to look at what other things may have been punched on this perforating machine. I'm not sure that I fully understandwhy and how it happens but it is accepted that if you use a tool to work steel, and then use it on stainless steel, you are going to have rusting problems with those stainless steel parts even when passivated.
The second thing to study is whether any changes were made in the stamping oils or other oils the parts have been exposed to. The oil must be completely removed before passivation, and this can take hours in a soak clean tank if the oil is really trapped.
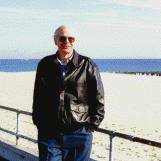
Ted Mooney, P.E.
Striving to live Aloha
finishing.com - Pine Beach, New Jersey
The surface condition at holes punched by a dull tool may be causing a decrease in the corrosion resistance. Smeared material, especially if the smearing creates small crevices, will not be as corrosion resistant as the original annealed sheet material. Where is the corrosion occurring, i.e. is it limited to the area around the holes? You might also investigate the history of the parts after passivation. For example, are all of the 10,000 produced parts subjected to the same process and conditions, or do they go to different customers? There may be circumstances where the parts are contaminated after passivation. Metallurgical examination of the corroded parts may be able to provide you with valuable clues, such as the presence of surface contamination, surface mechanical damage, etc.
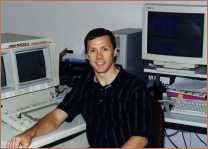
Larry Hanke
Minneapolis, Minnesota
1999
1999
Hi Shawn , The trouble with passivating Stainless steel after it has been worked is that the passivation process is really unreliable, it assumes that the underlying surface is microscopically clean and it is frequently not. The only way to be certain that the parts are clean & ready to be passivated is to electropolish them before passivation. Electropolishing (and deburring) enrich the metal surface in chrome & nickel by removing Iron which allows for more efficient & effective passivation. I suggest that you contact Team Metal Finishing (I think I have spelt it correctly) of Georgia who are experienced in this process and market systems to do it; they have a attachment from this web site , probably under "Jobshops". Speak to Dan Weaver . Best Regards

John Tenison - Woods
- Victoria Australia
Q, A, or Comment on THIS thread -or- Start a NEW Thread