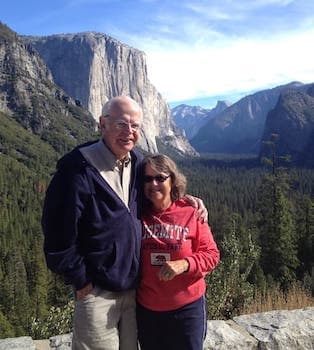
Curated with aloha by
Ted Mooney, P.E. RET
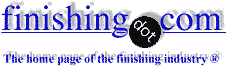
The authoritative public forum
for Metal Finishing 1989-2025
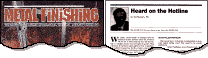
-----
Platinum Plating with P-salt
Q. Steve Koelzer I know this is an old post....but I'm looking into issues with our existing Pt plating bath. I am curious about your comment regarding Technic bath. Do you know if the solution is anything other than ammonium hydroxide? Do they add both ammonium nitrate and ammonium sulfamate ?
John Burgess- Houston, Texas
August 18, 2023
Ed. note: We doubt that Steve follows this anymore or is reachable at his old e-mail address from 23 years ago, but perhaps another reader or Technic's technical data sheet can help.
⇩ Related postings, oldest first ⇩
Q. In an effort to create a very specialized Platinum Plating bath I have been searching for Platinum Diamino Dinitrite. My question is this: Is platinum Diamino Dinitrite the Platinum "P-Salt"? What is the chemical formula for "P-salt" I thank you in advance for any help obtained here.
Anthony J. Coveyelectroformer - Corona, California
1999
A. Hi Anthony,
Michael Murphy, editor of Metal Finishing magazine looked this up for us. It's dinitro-diamine-platinum.
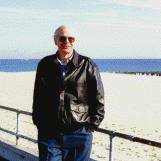
Ted Mooney, P.E.
Striving to live Aloha
finishing.com - Pine Beach, New Jersey
A. Platinum 'P' Salt is the diammine dinitro Platinum, Pt(NH3)2(NO2)2. It is conveniently mixed in solution with ammonia ⇦ this on eBay or Amazon [affil links] or ammonium compounds. Use neither ammonium nitrate (potential explosion! when dried [cf. ANFO]) nor ammonium sulfamate, as that is Technic's formulation. Check this out:
cis-Diammineplatinum(II) nitrite [14286-02-3] H6N4O4Pt
[(H3N)2Pt][NO2]2 Reference(s) 1. Brauer, 1965, Vol. 2, 1560 2. Holifield, P. J., private comm., 1974 3. Fountain, N. O., private comm., 1983
Hazard It decomposes explosively at 200 °C [1]. Dry material stored in clear bottles in sunlight for several weeks became sensitive and exploded violently on slight mechanical shock. The material is now supplied commercially moistened with water [2]. The dry salt may be readily ignited, and deflagration under confinement is similar to that of gunpowder. Presence of 10% of water reduced ignitability but did not slow the deflagration rate thereafter. Sensitivity to impact or friction was greater than that of nitrobenzene [3].
Steve Koelzer- Sunnyvale, California
2000
Q. Thanks for your long-lasting support to us, as a patronage. We are expecting the same in the future too. Kindly clarify the following:
We are a manufacturer of platinised titanium anodes. With our past experience, we'd like to step forward our activities to the process of platinum plating on NIOBIUM. However, we are interested to know about the procedure of pre-treatment (surface preparation, etching, surface cleaning) of niobium mesh and sheet, before plating.
For titanium, we conduct the following pre treatment (surface preparation):
1. Shot Blasting
2. Etching with HCl mix.
3. Cleaning with DM water.
Like the above procedure, we want to do the surface preparation of niobium. Kindly advise us the procedure please.
Regards,
Jaykumar.V- Chennai, India
2001
Q. Dear Friends:
I tried to coat Ni-base superalloy samples with Pt by using P-salt solution. My parameters: Temperature--90 degree C; Current: 2A/dm square; (the voltage will be automatically set, it was 2.30V).
However, I found some black matts on Pt coated surface (the black matte can be removed easily by using compressed air), the Pt coating color is semi-bright (instead of bright). The black matt is mainly Pt.
Could somebody here tell me why? Could you please provide me with a set of good parameters for this? Thanks.
coatings process engineer - Minneapolis, Minnesota
2007
Q. Hello and good day to you, sir. I do wish you the best of your forthcoming lifetime. I do apologize for asking this unfair question in unsuitable moment. I am Reza Aalizadeh Molayousef who is graduated of Chemistry(B.Sc). I was on my way to research in synthesis of some salts (Organometallic salts). dDue to the fact that we are faced with sanctions, I need some help to know how I would be able to synthesisze them. I couldn't find enough documents and papers or patents to figure out the way. The salts are listed below I do thank if you can help me with the mentioned unfair plea.
TaCl5
Pt(NH3)4 H3PO4
RuCl3.6H2O
H2IrCl6 6H2O
DNS for Pt
Look forward to hear from you soon,
April 8, 2012 - Iran
Q. I am using p-salt to plate titanium and I am aiming at 5.5 - 6.5 gms/per unit. If I could control the process to guarantee 5.5 gms/unit the savings would be worth an equipment upgrade. At the start of the working day the cycle time is 40 mins but by the end of the day it is up to 70 mins.
1) How can I constantly hit 5.5 gms/ unit? and 2) is there a way of constantly monitoring the solution and automatically adjusting the strength to enable me to plate more units per day?
Any suggestions?
Regards,
plating shop employee - Canterbury, Kent, England
November 21, 2012
A. Hi Keith. We appended your inquiry to a thread about platinum plating of titanium. Just to be clear: that is what you are inquiring about?
Amp-hour feeders which will add a concentrated solution in proportion to the ampere-hours consumed are pretty simple, inexpensive, and available -- from the vendors of plating power supplies/rectifiers and others.
Regards,
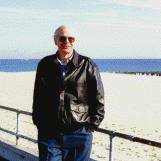
Ted Mooney, P.E.
Striving to live Aloha
finishing.com - Pine Beach, New Jersey
Q, A, or Comment on THIS thread -or- Start a NEW Thread