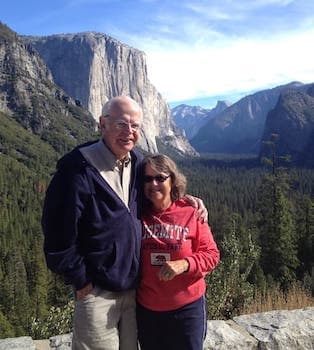
Curated with aloha by
Ted Mooney, P.E. RET
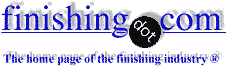
The authoritative public forum
for Metal Finishing 1989-2025
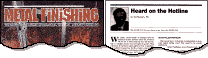
-----
Corrosion resistance of black oxide vs. zinc-iron phosphate?
Q. I'm a manufacturing engineer with a plating problem. We have a long acme threaded screw which is currently finished via the zinc-iron phosphate conversion process. We are looking into the possibility of moving the manufacture of this part off-shore and are finding that zinc-iron phosphate is not a common process offshore. Black oxide is more common. How does the corrosion resistance of black oxide compare to zinc-iron phosphate. The part is used in medium voltage electrical enclosures. The part is protected from the elements, and thermostats keep the internal cubicle temperature at 4 °C above the ambient temperature to control humidity.
Bob GlowienkaManufacturer of Medium Voltage Switchgear - Wendell, North Carolina, USA
2004
A. This sounds like a benign environment where the very limited corrosion resistance of black oxide won't be a problem. But this Acme screw sounds like a moving part that requires lubricity in the finish, and I think that phosphatization offers substantially more than black oxide. I doubt that a black oxided ball screw will be a good idea. But black oxide may be what you get anyway, regardless of what you specify, if you're not there to ensure compliance.
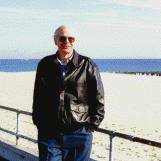
Ted Mooney, P.E.
Striving to live Aloha
finishing.com - Pine Beach, New Jersey
2004
A. Dear Bob,
Black Oxidising on ferrous metal, also called as blackodising, is a decorative finish and has very limited corrosion resistant properties. A suitable grade of Rust Preventive oil will increase the life. If a dry film as top coat is permissible, a thin film of clear PU, epoxy or other lacquer will give far better life.
Zinc-iron, zinc-calcium, manganese-iron phosphating with suitable anti-rust oil will give longer life. Manganese phosphating produces a dark grey finish. Alternatively, zinc plating with black passivation will serve the purpose.
PRABHAKAR GUPTA- Kanpur, U.P., India
2004
A. Since phosphate coatings and oxide coatings are very low corrosion resistance at low temperature, you may go for zinc plating with olive green conversion coating. It gives better corrosion resistance (more than 100 hrs salt spray comparing less than an hour for phosphate or oxide). Moreover this coating give adequate lubrication property.
N.KRISHNA PANDI- Madurai, Tamilnadu, India
2007
Q. What is purpose of blackodizing? We can use the same as rust arrestor?
Which DIN standard do we need to use for this? What is the test procedure?
Our requirement is to protect mild steel material components from humid atmosphere.
Also suggest alternate cost effective solution.
- CHENNAI, India
December 20, 2012
A. Hi Sunil. As you can see, we appended your inquiry to a thread which partially answers it. "Blackodizing" is a term used in India to describe the same process that is called "Black oxiding" here in the USA. It is not corrosion resistant. If you have a humid atmosphere, zinc plating might be a better choice, as it's the least expensive plating.
But in truth, mild steel components receive all kinds of metal platings and/or organic coatings, so it's hard to suggest the best one without a lot of information about your requirements. Good luck.
Regards,
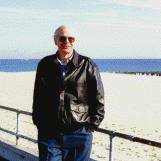
Ted Mooney, P.E.
Striving to live Aloha
finishing.com - Pine Beach, New Jersey
December , 2012
Rust preventive black oxiding
Q. We are frequently facing rusting of blackodised parts, is there any subsequent addition to blackodising process which can make it more Corrosion resistant in Normal weather condition?
I would like to know what is Salt spray life of Blackodised parts?
Thank you.
Buyer - Ahmadabad, Gujarat, India
August 13, 2014
A. Hi Kunal,
Black oxide coatings on their own offer very little in the line of corrosion resistance, they need a supplemental treatment to improve that aspect.
Common supplemental treatments vary from simply oiling them to applying coatings such as varnishes. The final use for the parts will determine which supplemental treatment you will require.
Aerospace - Yeovil, Somerset, UK
August 14, 2014
Q. Thanks Brian,
Please explore it a little.
employer - Ahmadabad, Gujarat, India
August 16, 2014
A. Hi cousin Kunal. As Brian implies, the ball is in your court as we await a description of your parts and their application -- all we can do is try to help with your specific situation.
But I raise a red flag when you say "normal weather conditions" -- outdoor exposure is not what black oxide is about. It can only be used outdoors in very limited situations like lovingly maintained firearms that are cleaned and oiled after each field trip. You may have the wrong finish for the application. Good luck.
Regards,
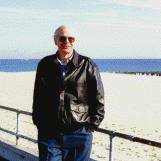
Ted Mooney, P.E.
Striving to live Aloha
finishing.com - Pine Beach, New Jersey
August 2014
Q. Hi ,
I wanted to know if after hot phosphating is done for a Hot Rolled fabricated tank, can ethylene glycol or commonly referred as "Radiator Coolant" be filled into the tank. There will be some amount of water content in the coolant. Will this affect the and react with the steel?
Please let me know,
Thanks,
Regards,
Bharath
Manufacturing of Tanks - Bangalore, KA, India
January 2, 2020
A. Hi Bharath. Sorry, I don't know and couldn't find anything on google easily -- but I suspect that ethylene glycol is harmless to phosphate coatings.
But the thing to remember is that commercial radiator coolant is not water plus ethylene glycol ... it is those two things PLUS about 10% corrosion inhibitors. Your tank will probably survive fine with commercial radiator coolant, but I would not bet on it surviving with just a 50-50 mix of water and ethylene glycol. Good luck.
Regards,
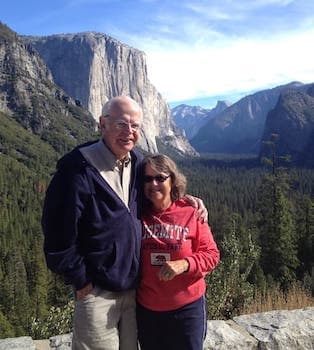
Ted Mooney, P.E. RET
Striving to live Aloha
finishing.com - Pine Beach, New Jersey
January 2020
Q, A, or Comment on THIS thread -or- Start a NEW Thread