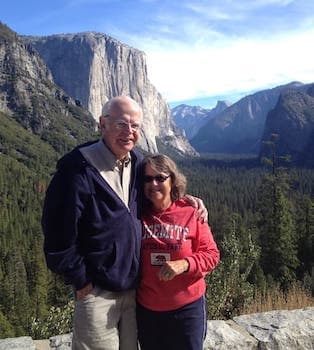
Curated with aloha by
Ted Mooney, P.E. RET
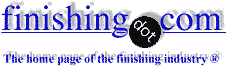
The authoritative public forum
for Metal Finishing 1989-2025
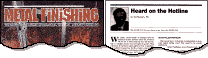
-----
High Scrap rate in nickel electroplating
My company makes Steel shafts by CNC machine. Range of diameter 6-
11 mm and length 30-50. We use an outside vendor (another company) to electroplate our metal shafts. At the next process after plating we always find scratches on the metal shaft. In total our productivity is more than one million pieces a month and the total scratched items can be 5-10%. We have a standard from customer of only 50 ppm. We use Nickel Plating.
My question: can we still scratch steel metal by re-electroplate. For effective result what kind chemical should be used to peel off scratched coating.
Regards,
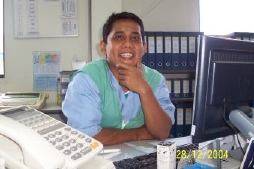
Rio Simbolon
Steel Shaft Company - Jakarta, DKI Jakarta, Indonesia
2004
2004
I'm sorry but I don't understand the question. Do you send scratched parts to the electroplating shop? Are the scratches in the substrate or the plating? Why is the plating shop sending you scratched parts, or aren't they?
This sounds like it is predominantly a contractual problem rather than a technical problem. Based on my limited understanding of what you've written, I think:
1. The plating shop should inspect the parts they receive from you and refuse to accept scratched parts.
2. The parts should be inspected by the plating shop (or your inspector at the plating shop) before shipment.
3. The parts should be inspected upon receipt from the plating shop.
Although 100 percent inspection is an impractical way to get to 50 ppm defective parts, as long as the reject ratio is 5 to 10 percent, it is very practical to inspect parts to see where the problem arises, and fix it.
You can re-plate the parts without stripping if tolerances permit, or you can strip and re-plate the parts--but I don't think you can ever achieve 50 ppm reject rates this way. You would need to do 100 percent inspection of a million parts; then strip and re-plate 100,000 rejects and then 100 percent inspect them, leaving 10,000 defects, which when stripped, re-plated and inspected would leave you with 1000 defects to be stripped, re-plated and inspected, leaving you with 100 defective parts, etc.
Let me conclude with a wild guess that the scratches arise in transit because no one is willing to spend the kind of money on packaging that would be necessary to stop the scratching.
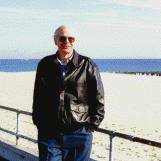
Ted Mooney, P.E.
Striving to live Aloha
finishing.com - Pine Beach, New Jersey
Dear Mr Rio Simbolon,
The transit damages are first and foremost cause for the scratches and the second is handling during the plating process; the components dimensions that you mention make me believe they are barrel plated; please work with your vendor to minimise Barrel speeds to about 6 RPM with adequate rubber or polypropylene lining on all the chutes, dryers and passage thru from which the parts travel to minimise scratching.
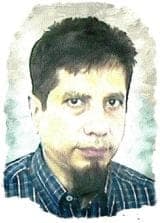
Khozem Vahaanwala
Saify Ind

Bengaluru, Karnataka, India
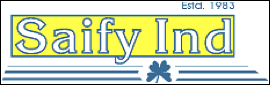
2004
Q, A, or Comment on THIS thread -or- Start a NEW Thread