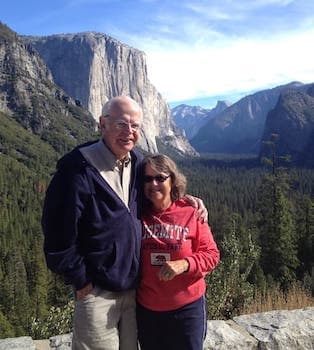
Curated with aloha by
Ted Mooney, P.E. RET
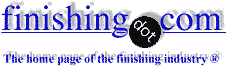
The authoritative public forum
for Metal Finishing 1989-2025
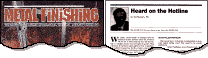
-----
Hard chrome plating thickness variation problems
Quickstart: Discussion of shields, thieves, auxiliary anodes, rotation issues, etc., in chrome plating to resolve thickness variation issues. Reasonable thickness variations are debated.
for Shops, Specifiers, & Engineers
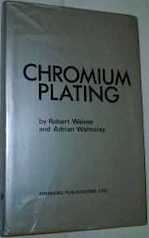
by Weiner & Walmsley (1980)
avail from eBay, AbeBooks, or Amazon
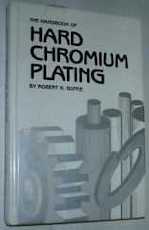
by Robert K. Guffie (1986)
avail from AbeBooks, or Amazon
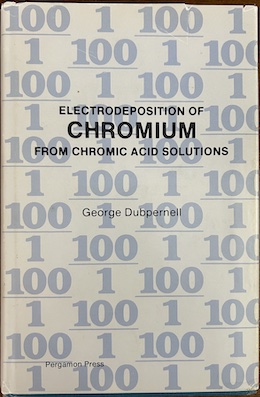
avail from eBay, AbeBooks, or Amazon
"Hard chromium plating: A Handbook of Modern Practice"
by John David Greenwood (1971)
avail from eBay
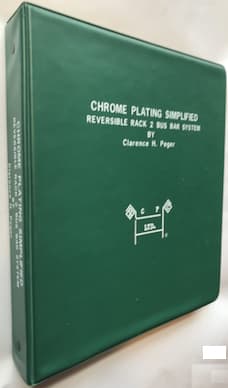
very rarely avail from Amazon
but copies are available in a few libraries)
"A Chromium Plating Bath With The Fluoride Ion"
by Alfred Perlenfein (2013)
avail from eBay, AbeBooks
(as an Amazon Associate & eBay Partner, we earn from qualifying purchases)
Q. We need min 80 microns in the plug bore body. What we achieve the plating thickness variation?
Prakash palaniEmployee - Tamilnadu, India
December 10, 2022
A. Hi prakash. Please attach a picture of the item in e-mail to mooney@finishing.com for posting here, and tell us the dimensions, etc. Getting hard chromium plating on the inside of a bore without auxiliary anodes in the bore is probably hopeless.
Luck & Regards,
Ted Mooney, P.E. RET
Striving to live Aloha
finishing.com - Pine Beach, New Jersey
⇩ Related postings, oldest first ⇩
Q. In hard chrome plating of piston rods (rod diameter 12.7 mm to 17.4 mm & length 150 mm to 500 mm), we are getting plating thickness variation up to 4 microns along the length and 2-3 microns on circumference. Could you please elaborate on the probable cause and the solution to the same.
Manoj GuptaAutomobile Shock Absorbers - Indore, M.P., India
2004
A. Hi Manoj. You didn't mention the thickness of the plating yet, so we don't know what the percentage variation is. And you didn't mention anything about the fixturing, so it's hard to say how to improve it. But, in general, chromium plating is more efficient at high current densities than at low current densities, so a high current density area will get much more plating than a low current density area. You need to be doing something fixture-wise to fix this (thieves, shields, anodes which conform better, rotation during plating, etc.) There is no solution adjustment that will cause the efficiency in the LCD area to even reach the efficiency of the HCD area, let alone exceed it. Good luck.
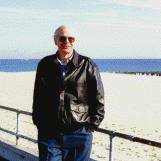
Ted Mooney, P.E.
Striving to live Aloha
finishing.com - Pine Beach, New Jersey
Q. Specified plating thickness to be achieved is 5-12 microns. Job is being held longitudinally on a vertical fixture with Plastic robbers on top and bottom. 4 to 6 rods on one fixture. Current density is 2.5 to 3 Amps/ Sq.in.
Manoj Gupta [returning]- Indore, M.P., India.
2004
A. Hopefully someone with substantial hands-on hard chrome plating experience will speak up if something sounds wrong, but this sounds to me like a reasonable variation in plating thickness for the conditions. Without rotating the parts, which would presumably be a very big problem, I doubt that you'll reduce that variation around the circumference. But slight changes in the shields, and making sure you have good agitation, may reduce the end to end variation.
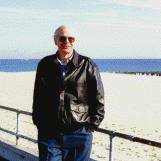
Ted Mooney, P.E.
Striving to live Aloha
finishing.com - Pine Beach, New Jersey
A. Manoj,
I think the thickness variation you describe for a hard chrome solution can't give you a better metal distribution then you have. If you like to have a better metal distribution change to electroless nickel.
Regards,
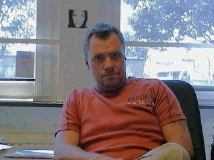
Anders Sundman
4th Generation Surface Engineering
Consultant - Arvika,
Sweden
A. Dear Mr Manoj,
If your spec says 5-12 microns, and you already have a tolerance of 7 microns and are achieving a variation of just four, everything seems to be working for you, the variation is within reasonable limits.
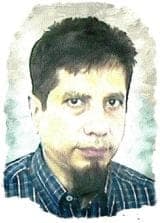
Khozem Vahaanwala
Saify Ind

Bengaluru, Karnataka, India
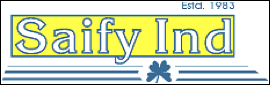
A. Dear Mr. KV,
I think you got it wrong tolerance and variation are two different things. The specs demand coating of 5-12 microns, which means that the coating can be minimum 5 microns and maximum 12 microns but does not say that it can vary from 5 to 12. I think you can get me. As far as the initial question is concerned, I think job rotation, fixture design and robbers can solve your problem. We plate rods 8 to 20 mm dia 7 to 14 microns, both parallel and true within 2 microns. Go ahead try a better job holding design.
ALL THE BEST
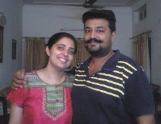
Vikram Dogra
Irusha India - Chandigarh, India
A. PLATING THICKNESS VARIATION DEPENDS ON
1. SURFACE PREPARATION
2. CONTROL OF BATH CONDITIONS
3. UNIFORMITY OF THE POWER SOURCE
4. ANODE PLACEMENT
5. SHIELDS, THIEVES
6. TANK DESIGN, etc.,
Practically variation is there .
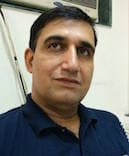
Ajay Raina
Ludhiana, Punjab, India
A. Manoj,
I agree with many here about your question about thieves & shields. To get a better metal distribution you must think about this. How long is your anode, because the anode must be a little shorter than the part. Are the anodes active. Is the anode arrangement so that it goes around the part. Sulphate ratio to the chrome, trivalent chrome metal contamination, temperature. Also a low current density will help you with a better metal distribution.
Regards,
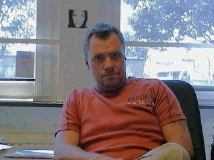
Anders Sundman
4th Generation Surface Engineering
Consultant - Arvika,
Sweden
![]() |
Q. I noticed that one of the factors listed in the chrome plating process includes "shields and thieves". Can anyone elaborate on what these items are, and if so - what exactly they do? Eric Burns- Buffalo, NY USA February 14, 2008 A. Shields are widely used in plating in general. They are pieces of plastic placed in an appropriate place somewhere between the anode and the cathode to block a short electrical path (solution path). The current cannot flow through them, so the 'shortest path' for the electricity, which might have built up too much plating on a protruding corner of the part, doesn't exist anymore and the electricity must take a different path that hopefully leads to better plating distribution. ![]() Ted Mooney, P.E. Striving to live Aloha finishing.com - Pine Beach, New Jersey |
Q. My name is WALMIK PAWAR I am in NASIK. We mfg. piston ring from dia. 48 to 160 mm. I have big problem in chrome plating. The problem is chrome thickness variation within length and circumference.
WALMIK PAWARPLATING SHOP EMPLOYEE - NASHIK, MAHARASHTRA, India
February 10, 2011
Need 50 micron chrome plating thickness but can only get 25
Q. What are the probable reasons for not getting chrome plating thickness as required? Required is 50 micron but able to reach up to 25 micron only.
Sandip mahajan- ahemadabad, Gujarat, India
August 6, 2014
A. Hi cousin. Your question is too brief. Are you saying that you can't get 50 microns even if you plate for two days? Or are you saying that you don't achieve it in the arbitrary time period that you wish?
Let's start with a Faraday's Law calculation to determine what efficiency you are achieving --
What is the total surface area of the plated parts, the plating time, and the amperage reading of the ammeter on the rectifier?
Regards,
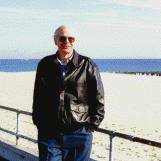
Ted Mooney, P.E.
Striving to live Aloha
finishing.com - Pine Beach, New Jersey
Q. I have a shaft of dia. 170 mm and I have to chrome plate it to have a final dimensions of dia. 169f7, i.e. (168.957 / 168.917). What is the machine tolerance that has to be maintained to chrome plate it by 25 µm ± 5 µm?
Vikram Kulkarni- Dammam / Saudi Arabia
January 15, 2018
A. Hi. If the minimum allowable final size is 168.917 and it has the minimum of 20 µm of chrome, the diameter will increase by only .04 mm, so before plating it must be 168.877 mm or more before plating. If the maximum allowable final size after plating is 168.957 and it has the maximum of 30 µm on it, the diameter will increase by .06 mm, so it must be no larger than 168.897 before plating.
Regards,
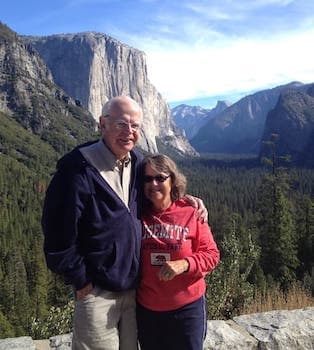
Ted Mooney, P.E. RET
Striving to live Aloha
finishing.com - Pine Beach, New Jersey
Q. Hard Chrome Plating:
I am trying to plate a 1" x 4" panel uniformly on one side using a rack that has a plate that measures 4.75" x 1.75". The 1x4 is mounted onto the plate and held with two 10-32 bolts on edges. I plated at 2 ASI for a surface area of 16.63 in^2 for 45 minutes. I got less plating in the center and more plating on the edges. Shall I use robbers or shields to limit the build up on the edges? The rack is already behaving as a robber.
- Los Angeles, California, USA
May 8, 2018
A. Hi Orlando. A sketch or photo of the arrangement would probably be worth a thousand words. Although I've seen shields successfully employed in plating, I have personally never seen them used in chrome plating and am not optimistic about it. I think the most straightforward solution would be a properly shaped conforming anode rather than a shield or a robber.
Regards,
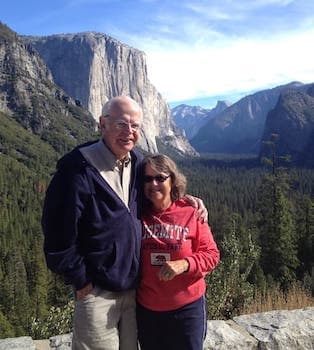
Ted Mooney, P.E. RET
Striving to live Aloha
finishing.com - Pine Beach, New Jersey
Q. we are doing hard chrome plating on shafts.In that plating thickness variation is occurred. One side 0.070 mm and opposite side 0.190 mm.
How to reduce The thickness variation in plating?
Employee - Ahmedabad India
September 4, 2019
A. Hi Anil. It is fairly common to keep shafts and rollers rotating during chrome plating, so that is one approach. It is necessary to maintain very consistent anode-to-cathode spacing, so that's another approach. If you are plating shafts vertically, it's possible that the plating solution at the bottom of the tank is colder than near the top of the tank.
You might want to have a hard chrome plating consultant, or at least a representative from your chrome plating solution provider take a look -- or forward photos and full details, and maybe a kindly reader can help. Good luck.
Regards,
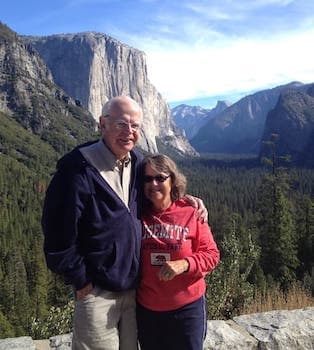
Ted Mooney, P.E. RET
Striving to live Aloha
finishing.com - Pine Beach, New Jersey
![]() |
A. HI. I'm not doing chrome plating. Asahi Aero Malaysia Sdn Bhd - Selangor, Malaysia January 8, 2020 |
? How did you hang the parts in your racks? Did you use thieves or in it the bottom of the parts there will be a thicker deposit?
Regards
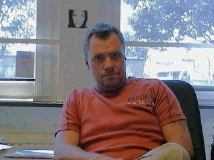
Anders Sundman
4th Generation Surface Engineering
Consultant - Arvika,
Sweden
January 16, 2020
A. Hi Anil,
You should check the distance between anode to cathode.
It must be same from both sides as well as not more than 5 to 6 inches every side as chrome has very less conductivity 12% to most effective 24% only.
And also you can make the arrangement of round moving cathode movement which would help you to balance the thickness distribution on the surface of component, as well by mild agitation -- it maintains the temperature of whole solution.
- New Delhi, India
March 21, 2020
Q, A, or Comment on THIS thread -or- Start a NEW Thread