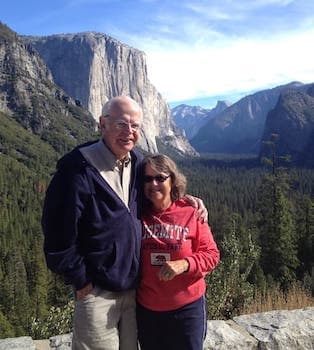
Curated with aloha by
Ted Mooney, P.E. RET
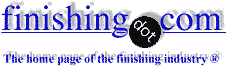
The authoritative public forum
for Metal Finishing 1989-2025
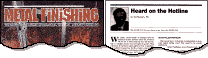
-----
Copper plating steel in home shop
Q. I have tried to copper plate steel for a while as well. I have a good lab supplier so I have access to high quality chemicals and it is still hard to do. Have any of you tried heating the plating with a torch of some sort? Perhaps heating the plated metal could smooth out the copper crystals by melting them together.
MJF MilesHome chemist - Denver, Colorado
February 14, 2022
A. Hi MJF. You're certainly welcome to try it, but I don't think it will work.
"Copper crystals" are not a normal part of copper plating to be resolved -- they are in indication of something being done wrong :-)
Luck & Regards,
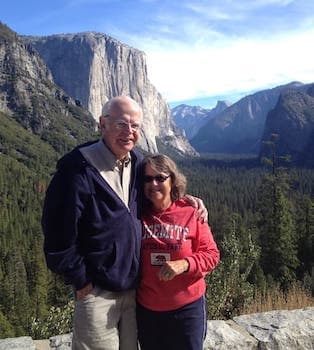
Ted Mooney, P.E. RET
Striving to live Aloha
finishing.com - Pine Beach, New Jersey
Q. Hi Dale,
Do you mind sharing your setup? It seems you've had some success which I'm looking to emulate. I'm seeking to get a decorative, hopefully polishable coating on some small welded art pieces I have made.
Regards, Mike.
Hobbyist - New Hampshire
April 9, 2022
⇩ Related postings, oldest first ⇩
Q. I build frames of 4" by 4" square steel tubing 20' long & 4' by 8' flat steel to mount exterior electrical services for my fish farming operation. I tried hot dipped galvanizing on a dozen but warping was a problem. I also painted some but paint acts as an electrical insulator and makes a good ground difficult.
Is copper plating a practical solution? I am working with new steel, have a sand blaster, and hot water pressure washer (sometimes erroneously called a steam machine) and am used to working with muriatic acid
⇦ this on
eBay or
Amazon [affil links] , and copper sulphate
⇦ this on
eBay or
Amazon [affil links] by the ton but am unwilling to expose myself or my farm to any really caustic or poisonous solutions.
If it is feasible where would I find information & equipment for a low tech copper plating facility.
farm - Greensboro, Alabama
2001
A. Hi, Bill.
Copper probably isn't the ideal choice because it will tarnish and corrode and become non-conductive (you may have seen green or brown copper roofs). When you see non-corroded copper, it is because it has a lacquer (insulative) coating. Nickel plating is probably a better choice.
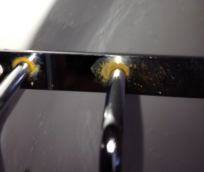
You may or may not know that plating jobshops are ubiquitous, and you can probably find an established shop in your area to plate this framing for you if you wish to go that way.
Electroplating as a kids' science experiment is dead easy -- third graders have done the experiments in our FAQ "How Electroplating Works". But robust, functional plating is something else. One issue is that most plating (the exception is zinc plating) is more noble than steel, so if there is any porosity or pinholes at all, the plating causes the steel base metal to rapidly corrode in an effort to sacrificially protect it. This photo shows a nickel plated bar rack designed for indoor use after one day outside.
My advice would be to play around with electroplating if you wish, and have fun (use your copper sulphate and a tiny dash of muriatic acid as long as you already know how to safely handle them) -- but to send your real parts to a plating shop :-)
Good luck and Regards,
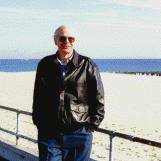
Ted Mooney, P.E.
Striving to live Aloha
finishing.com - Pine Beach, New Jersey
Q. I am wanting to copper plate some steel figures for outdoor exposure. Will I have any luck by using your techniques and experimenting on a larger scale? The figures are heavy steel, about 6" tall. I have some electrical copper bus from the utility industry that I wanted to use for the anode, and a heavy booster type 12 volt battery charger ⇦ this on eBay or Amazon [affil links] to furnish the current. Could I use this to dissolve enough copper in the salts to adequately plate the figures? How much salts and what kind would be required for about 1 gallon of plating solution? Also, where could I find the salts? This is my first encounter with plating. I understand the process, but do not have much equipment to work with. I only want to try this for some ornamental figures -- any help would be appreciated. Would copper sulphate crystals dissolved in the water be of any help?
Dwain V [surname deleted for privacy by Editor]hobbyist - Abilene, Texas
2004
A. Hi, Dwain. You are understanding the principle of our electroplating science project instructions, but you are probably not quite understanding the real-world limitations of it :-)
You can force electrons from one pole to another with a battery or rectifier (or battery charger
⇦ this on
eBay or
Amazon [affil links]
) and in this way you can cause metal that is at one pole to dissolve into an ionized state in aqueous solution, convey those ions across the solution, and convert them back to the metallic state at the other pole -- moving metal from one pole to the other. This is very useful knowledge for students, helping them to understand the principles of chemistry and electricity and letting them see it in action -- which is why we prepared and posted the experiment. But, sorry, unfortunately this experiment doesn't put a homeowner/hobbyist too much closer to successfully electroplating copper as a functional coating on steel/iron figures :-)
'Functional' is the operative word. You can't successfully electroplate a functional coating onto steel/iron from a simple salt of copper, like copper sulphate or copper acetate (a vinegar solution) primarily because it will "immersion deposit" (remember the science class lesson where you drops nails into copper sulphate and they copper plate themselves with no electricity) and will have no adhesion. To get a functional, adherent coating you need to start over with a different plating solution (a cyanide copper plating solution) which is far too hazardous for home use, or a proprietary copper pyrophosphate solution, or do nickel plating first. The student plating won't be fine grained, it won't be pore free, it won't be bright, it won't be of consistent thickness, it won't plate onto the recesses of your figurines.
Good luck and have fun, but don't do it to the figures if they are of value to you until you've done a lot of experimentation -- instead send them to a plating shop which can use the proper cyanide-based chemistry for real-world applications as opposed to science class demos. Good luck!
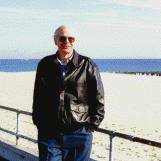
Ted Mooney, P.E.
Striving to live Aloha
finishing.com - Pine Beach, New Jersey
2004
Q. Dear Ted
You went on a bit about what one shouldn't do, but what CAN you do if you want to copper plate steel? Understood about the immersion deposit bit, for example.
But WHICH salts of copper are okay to use? How much current?
Thanks
Prashant
- Dehra Dun, Uttaranchal, India
2005
sometimes on
AbeBooks or Amazon
(affil links)
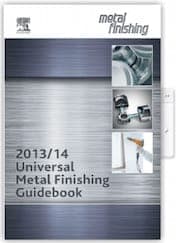
free pdf is currently available from academia.edu
A. Hi, Prashant. The reason I "went on a bit" was that I hoping to preempt your question -- but apparently it didn't work :-)
You have to switch to copper cyanide (very dangerous) or a proprietary copper pyrophosphate bath -- although a better approach might be to nickel plate first, and then copper plate. As for the amount of current, Faraday's Law tells you how many amp-hours you need for how much copper deposition. You need to use careful temperature control, uniform air agitation, and efficient continuous filtration. You need to forget using scrap copper as an anode material, and buy proper phosphorized oxygen-free anodes. You should get electroplating power supplies with periodic reverse current capability.
It is one thing for us to teach a student to electrochemically move copper from an anode to the cathode as a lesson in chemistry and to demonstrate Faraday's Law, but it's an entirely different thing to apply a thick, bright, adherent, pore-free, corrosion resistant, robust, functional copper coating. It's a bit like showing students how to build clay models of automobiles so they can run wind tunnel tests, and then having them ask what tweaks they'll need to do to those clay "automobiles" so they can drive them on the freeway :-)
An inexpensive and ubiquitous book on the subject is the Metal Finishing Guidebook. It will introduce you to how to do "real" copper electroplating as opposed to a grade school science project. Further, it has tables that do the Faraday's Law calculation for you and tell you how many ampere-hours you need to apply for a given thickness of plating. Best of luck with it, Prashant!
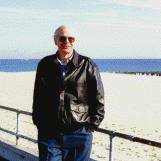
Ted Mooney, P.E.
Striving to live Aloha
finishing.com - Pine Beach, New Jersey
Q. Hi Ted,
I understand from this discussion that --
a) Simple D-I-Y electroplating is possible (copper on steel) at home
and
b) It can't be done at home on large scale but is possible at a small scale.
Here is exactly what I want to do. I have a steel water bottle (16 oz). I want to coat the inside wall of this bottle with copper. I want to leave the outside untouched.
Is it possible to do this at home, and if yes, what material do I need to buy.
If not possible at home, can someone help me find an electroplating shop in southern LA which can do this. This is a really small scale job so not sure if commercial guys would be interested in this.
- Torrance, California
July 8, 2009
A. Hi, Nishith. No, that is not what I was trying to say. Maybe I could put it this way:
a). Simple non-functional copper on steel plating for the sole purpose of science projects is possible at home, and so easy that grammar school kids can do it.
but
b). Functional copper plating on steel requires poisonous cyanide solutions (which are utterly inappropriate for a home) or proprietary copper pyrophosphate solutions, together with temperature control, air agitation, filtration, phosphorized anodes, proper power supplies, experience, and access to solution analysis equipment.
I am not saying it is impossible to do functional copper plating at home -- experienced and dedicated hobbyists do it (but again, they generally buy proprietary copper plating solutions, they don't use home brew). I am saying again that you can't "extend" our grammar school science experiment on copper plating to use it for functional plating anymore than you can "extend" a clay model of an automobile into a functional vehicle. The level of complexity is in excess of what people would expect, and we haven't yet even talked about the requisite cleaning, acid activation, and anti-tarnish post-treatment.
How thick must your copper be? How shiny, how pore-free, how tarnish resistant? Why do you want to do this?
Please see our Jobshops Directory for plating shops in southern California if you are interested in that route. Thanks very much and best of luck!
I am NOT trying to discourage you from experimenting and learning, but that involves practicing on scrap for some weeks and learning gradually. Expecting to do functional copper plating on the interior of a steel water bottle with no prior experience just isn't realistic.
Regards,
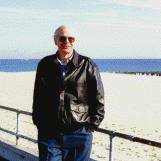
Ted Mooney, P.E.
Striving to live Aloha
finishing.com - Pine Beach, New Jersey
Q. Hello,
I am wanting to start turning projectiles for reloading ammunition, and need to plate them with an exterior of soft copper. My dad said that he was once told, that to electroplate copper onto steel, you need to first plate it with nickel as a "Primer" coat. I don't think it will be much of a problem to set up two tanks figuring they would only need to be about a foot square and maybe a foot deep give or take. The copper and "Primer" metal electrodes will be a big startup cost but well worth it for how long they would last.
Question #1: Will this work, to plate the steel with a base of nickel, then outer layer of copper?
Question #2: If this type of system will work, what "Primer" metal would be best nickel, brass, etc?
Question #3: If this will work, will the "Primer" metal adhere to the steel, and then the copper to the "Primer" well enough to take being shot out of a firearm?
Question #4: Will this type of process require cyanide?
Question #5: Can copper be easily plated straight to solid brass projectiles?
Thanks,
Nick
- Indianapolis, Indiana
December 24, 2009
A. Hi, Nick. You dad is correct! Rather than plate the steel with a cyanide copper process, an alternative is to nickel plate the steel first, then copper plate the nickel from a copper sulphate process.
So your answers are:
#1: Yes
#2: Nickel
#3: Yes, if plated properly -- but I might doubt that you could learn to do it well enough in short order and with no equipment or training
#4: No
#5: "Straight", yes but not "easily."
But showing through your question, is the belief that you just mix simple chemicals and come up with a simple, safe, reliable two-step process :-)
Rather, you'll need to buy proprietary process chemistry, not mix stuff in a sink. You'll need ten tanks (electrocleaner, acid activate, anti-tarnish, multiple rinses), not two. And you'll be at risk of cartridges jamming in the barrel or exploding from hydrogen embrittlement. Certainly anything can be done if you apply yourself hard enough, but you won't get to the point of sufficient knowledge with internet forum answers; you need to get plating books and study them and mostly put in long hours of practice :-) Best of luck!
Regards,
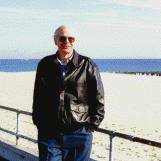
Ted Mooney, P.E.
Striving to live Aloha
finishing.com - Pine Beach, New Jersey
Q. I heard that steel and iron can be copper electroplated with something called "Copper strike" or a thin nickel plating.
My question is what is Copper strike and where can I purchase the "proprietary solutions"?
Thank you
- Huntington Beach, California
March 23, 2011
A. Hi, Mario.
"Strike" in this context means a thin initial layer of plating.
Yes, it is possible to plate onto steel by starting with a thin coating of nickel plating or a thin coating from a cyanide copper solution or a proprietary copper pyrophosphate solution, and then finishing up with a heavy coating from an acid copper plating solution.
Adv.
Suppliers of these proprietary copper plating solutions include finishing.com's supporting advertiser EPI / Electrochemical Products Inc. [a finishing.com supporting advertiser], but you can also google "hobby plating supplier".
Regards,
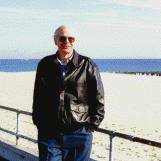
Ted Mooney, P.E.
Striving to live Aloha
finishing.com - Pine Beach, New Jersey
Q. Talking about the zinc penny blanks that are then coated in copper: Can I zinc plate steel and then copper plate that with electrolysis? I.e., vinegar/salt solution and use zinc anode for the first step to plate the steel then swap it for a copper anode for the copper plating?
My problem is I have been trying to copper plate steel with electrolysis but it just isn't adhering to the steel. I can literally see all the copper forming but it just sits on the surface and knocks off. I want to have some adhesion so if any ideas on the best way to do this (with household products) would be great! Thanks!
Josh Warb- Vancouver, Canada
February 24, 2013
A. Hi Josh. An intermediate layer of zinc will only make the problem worse. If you will read this page to which we have appended your inquiry, you'll have a better understanding of the problem. Make sure the steel that you are trying to plate is utterly clean and free of oxide by scrubbing with pumice powder, rinsing, dipping in muriatic acid, rinsing, then make sure the current is on before you start immersing it, and maybe consider a very dilute solution as a strike, then a more concentrated one for the bulk of the plating ... and that will be the best you can do from a copper sulphate solution. Either a proprietary copper strike, or nickel plating is really the right path. Good luck.
Regards,
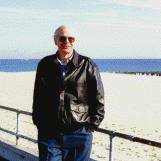
Ted Mooney, P.E.
Striving to live Aloha
finishing.com - Pine Beach, New Jersey
Q. Thanks so much. So after reading this it seems zinc isn't the way to go but Nickel plating as a strike/underplating sort of coat then copper will work fine.
Can I nickel plate with a vinegar/salt solution and nickel as an anode or do I need to have nickel sulphate? What does nickel sulphate do that vinegar/salt doesn't or do they do the same thing and allow ion transfer (guessing that's what they do).
Thanks for you help!
- Vancouver, Canada
A. Hi Josh. Try both as a learning experience and let us know what happens.
But no, it won't "work fine". I have tried both by explanation and by example to convey that an elementary school experiment with safe household ingredients, which is intended to demonstrate the electrochemical principle of how plating works, simply cannot be extrapolated into robust industrial quality plating that will offer thickness, brightness, freedom from porosity, and proper adhesion.
If you want robust plating you either have to send the components to a plating shop or you need to buy the proprietary plating solutions with their trade secret addition agents, and the filters, heaters, regulated power supplies, air agitation systems, hull cell test equipment, lab equipment, and other equipment associated with industrial quality plating. Then you have to really study. There are books devoted exclusively to nickel plating, books devoted exclusively to plating equipment, books devoted exclusively to troubleshooting plating problems like limited adhesion.
I'm just trying to be realistic, not discouraging. If you want to experiment and learn, by all means try all this stuff! But if you actually need copper plating, send it to a plating shop. You can't build an FAA certified aircraft from children's Lego blocks in your kitchen and you just can't do robust copper plating on steel in a kitchen using child-safe household supplies. But you can certainly enjoy the experiments and learn from them!
Regards,
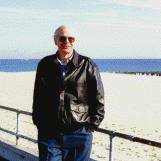
Ted Mooney, P.E.
Striving to live Aloha
finishing.com - Pine Beach, New Jersey
Q. I guess what I really want to know is what is the easiest way I can with available home ingredients plate copper over steel. I was also just thinking brass -- can I brass plate steel and then copper plate that? Nickel seems like it is hard to get hold of. I want to be able to get hold of the ingredients easily -- seems like copper plating may just be too hard to acquire for steel.
Thanks again.
- Vancouver, canada
February 25, 2013
Electroplating Steel with Copper Sulphate and Cerium Oxide
Q. I have made a bath of copper sulphate with cerium oxide using 0.4 amp. current for 10 mins. but did not find good coating on M.S. Can anyone tell me and help me to solve this?
fahad jabbar- Karachi,sindh,Pakistan
February 23, 2014
A. Hi Fahad. We appended your inquiry to a thread which hopefully explains why you are having a problem with this. Can we start with a few questions in return?
- Have you previously done successful electroplating so that you understand the issues of cleaning to a waterbreak-free surface and properly acid activating, or is electroplating new to you?
- Is this "copper sulphate" that you mention just plain copper sulphate or is it a properly formulated proprietary bright acid copper plating bath?
- Is there a reason you can't start / didn't start with a nickel strike or cyanide copper strike?
- What are you trying to do? What does cerium oxide have to do with it?
Thanks and good luck.
Regards,
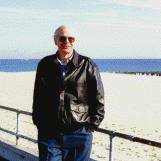
Ted Mooney, P.E.
Striving to live Aloha
finishing.com - Pine Beach, New Jersey
Q. Hey Ted,
I enjoy reading your answers, and while I do agree that if a professional finish is what you're after then it's best to take it to the professionals - but that being said I still want to do it myself. I'm looking to copper plate steel with no nickel strike or cyanide copper underneath (Pure nickel seems to hard/$$$ to get and cyanide too dangerous). I know I won't get as good a result as all these proprietary blends but I think I can get better results then the vinegar & coins method I first learned beck in elementary school. Maybe I can lay out what I know and you fill in a few of the blanks/ offer some tips? I will number my limited bit of knowledge on the subject so you can best critique each step separately.
1) I know preparing the steel is very important, I would polish the steel to be plated up to 2000 grit sandpaper, then polish it with a buffing wheel and compound. After this I would clean the part with brake cleaner brake cleaner
⇦ this on
eBay
or
Amazon [affil links]
.
2) I would load up some distilled water in a spray bottle to make sure water doesn't bead on the steel. This I believe is done by dipping the steel for approx. 5 min in a strong acid. Any ideas how to acquire a suitable acid for cheap? Or concentrate one myself?
3) I know the first layer or "strike" is very important, but I also don't know how to accomplish this in my D-I-Y project. I'm thinking at lower amps, and less acid in the bath. The composition of this "strike bath" I need help on. It could be one of the following but I need help in which to pursue in my D-I-Y adventure (even though I won't get my hopes set on anything other than advancing my knowledge on the subject)
3.1) non oxidized scrap copper dissolved in acid, muriatic, sulfuric, concrete etching acid from Home Depot? I know it matter but what I can get my hands on for cheap might win out. I also think non iodized salt has to go in there, at this point I'm just guessing.
3.2) an alkaline strike other than cyanide, I read there was a new environmentally friendly version even stronger than cyanide - I know hobby plating D-I-Y flash copper kit uses something like this. Can this be bought/made cheaply?
3.3) copper sulphate or copper acetate [affil links]. No this would not be a proprietary blend but probably something bought for killing roots also from Home Depot.
4) After striking it, I think to get a brighter finish you use a bit more acid, dissolve a bit more copper, and flip the polarity of the power supply occasionally during plated (i.e., take a bit of copper back off. Electro polishing I think I heard it called -- even though that name sounds wrong to me)
5) After this I would polish it on the buffer wheel with compound and coat it with some clear coat ( I don't need it to be conductive just decorative) so it wouldn't corrode.
Re-reading this please note that I do understand how dumb I sound, this is not my area of expertise at all. But I do believe there are many more people like me who want to cut corners, save some pennies, but also achieve something nice for their hobbies and crafts that's better then just plain vinegar electroplating. Thank you for bearing with me and I appreciate any help.
-John
John beckerleg
- Tempe, Arizona, USA
November 2014
A. Hi John. I admit that it's frustrating that I can't seem to get across the central point about the problem with trying to copper plate onto steel with vinegar, battery acid, muriatic acid, copper sulphate, copper acetate, root killer, or any kitchen or hardware store chemical you can name -- and it's that copper is more noble than steel...
You can make a battery with electrodes of copper & zinc (the grammar school potato battery or lemon battery), or copper & steel. If you stick a steel nail and a copper penny into a lemon, you make a battery of about 0.3 volts as the copper dissolves into the lemon juice, migrates over to the steel nail and then coats it with copper metal. You can't actually "electroplate" copper onto steel this way because it deposits on the steel without any current applied, and generates about 0.3 volts while it's doing so. The copper-steel pair is itself a battery, it's not a resistance that your power supply must overcome. That is at the heart of why you don't get adhesion -- it just deposits all by itself, beyond your control, as a non-adherent immersion coating. The thing about copper cyanide, or copper pyrophosphate is that they don't form such a battery with steel because the copper is tightly complexed; rather you need to apply power to get the copper to plate.
The best that you can hope for with copper sulphate or any simple salt of copper, is that if you start with a very dilute (very low in copper) "strike" solution, and you apply power before immersing the steel part, you can minimize the "immersion deposit" and thus somewhat improve the adhesion. After it's covered with a thin layer of copper you can then use a higher concentration standard plating solution.
1. Water *will* bead on the steel after brake cleaner. You can clean with a solvent as the first cleaning step, but not the last step. The best pretreatment for very low volume would be scrubbing with a solution of pumice and a pinch of detergent. Then you can rinse with DI water, but otherwise skip step 2 and not worry about the acid.
2. DI rinse only
3. The proprietary plating solution would be best for the reason described: it avoids immersion plating. If you don't want to buy that, then all you can do if minimize immersion plating by use of a dilute solution and hot entry. You can't stop it.
4. Then try a stronger solution of copper sulphate and sulfuric acid for the balance of the plating. You can look up operating conditions in the on-line version of the Metal Finishing Guidebook.
5. Yes, you'll have to manually buff the copper as it will not deposit bright.
Finishing.com has been on the air 20 years now and received a quarter million postings with no hobbyist ever reporting back that they achieved robust copper plating on steel from kitchen or hardware store chemistry. Maybe you'll be first; I hope so! Good luck.
Regards,
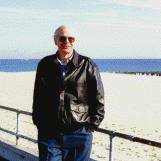
Ted Mooney, P.E.
Striving to live Aloha
finishing.com - Pine Beach, New Jersey
A. I have successfully plated copper at home. My mix is a weak solution of copper sulphate made with battery acid
⇦ this on
eBay
or
Amazon [affil links]
and copper. I added phosphoric acid ("Lime away") and tiny amount of surfactant (dish soap detergent). The surfactant makes the finish brighter.
Current was very low and copper bonded well to totally clean steel parts. Cleaning was by hydrochloric acid and scrubbing with pumice powder. The finish is dull copper but easy to polish. I used electrolytic copper (busbar) for the anode. Current about 1 amp/sq ft. Temp 80 °F. Slight agitation. Immediately after immersion I increased current to 10 amps/sq.ft for under a second then dropped down to the 1 amp/sqft.
Q. I am doing this so I can tin plate later. Not sure if the copper plate is needed but I can't find out if it is or not.
ron doctors- Santa Barbara, California, USA
July 31, 2015
Thanks Ron, and congratulations! What is the purpose of the tin plating? An under-layer of copper is not needed.
Regards,
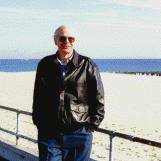
Ted Mooney, P.E.
Striving to live Aloha
finishing.com - Pine Beach, New Jersey
First just a thank you note for Ted for a very interesting discussion.
I'm going to try the Nickel strike as mentioned followed by a lot of trial & error in the copper plating.
In the end though I may just stick with the nickel as Ted convinced me beyond doubt that I'm an idiot in the making, for even thinking this is possible at home. It should be fun trying though. :D
- Yorkshire, England
February 1, 2019
A. Hi Tony, thanks for the kind words. While I am trying to dissuade people from unrealistic expectations and perhaps ruining objects that were important to them, I'm certainly not trying to dissuade anyone from safe experimentation on scrap; to the contrary, we wrote our "How Electroplating Works" experiments for grammar school children hoping they would experiment -- and I hope that adults will do so as well.
Regards,
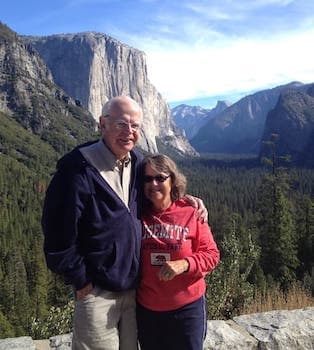
Ted Mooney, P.E. RET
Striving to live Aloha
finishing.com - Pine Beach, New Jersey
Alright ted, Mistake-maker here. I polished 8 bullet shaped nuts of steel. there was some copper present before polishing down to bare steel. I made a copper sulphate solution, cleaned my parts, them placed them in the solution and then applied 6 volts .4 amps. However, at the same time I was making my Nickel bath using vinegar and salt and just jumpered over to the copper bath energizing both baths using one power supply (quit laughing). None of the parts plated except one had an area about 3/8 in in diam that plated beautifully and thick. The rest of them all washed off easily and the parts looked pitted. Reading all your info I think these parts may have been nickel struck and then copper plated. The one that plated oh so beautifully maybe still had some nickel present. So tomorrow, we re-polish clean, nickel, then copper, polish the copper and then a nickel plate. I am not sure if I am getting anywhere but the part that plated was very good. I am having fun trying this. I take to heart your advice and tomorrow I will do things closer to what you recommend. Maybe adding a little muriatic to my brew.
Dale Scribnerretired machinist - Sacramento, California USA
May 7, 2020
Well Ted, believe it or don't, I did what you said. I did the nickel strike and then copper. I polished the copper and then plated nickel over that. It pays to listen to you. Thank you for your expertise. Dale
Dale engineering, retired - Sacramento, California USA
May 8, 2020
Great news Dale! I'm not a hands-on plater myself, but I try to be a listener also and to pass along what I hear :-)
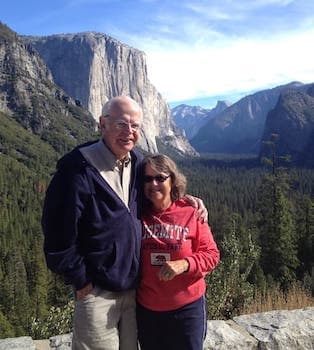
Ted Mooney, P.E. RET
Striving to live Aloha
finishing.com - Pine Beach, New Jersey
A. As a follow up my plating experience I have been having very good luck with Nickel plating. I purchased a polisher and find when I polish the parts they come out beautiful and fast. The prep is where the quality is. I made the simple vinegar, salt solution and used 2 Nickel electrodes. The positive completely dissolved in the solution. I am so impressed how easy this is. However, The prep is so important. You kind of get out what you put in. Polish a screw head, plate it in seconds, and it is bright and shiny. Again I thank you for all you do. Dale
Dale Scribner [returning]Dale engineering, retired - Sacramento, California USA
May 26, 2020
Alternating Copper and Nickel Plating Layers
June 12, 2020Q. I too am needing to plate steel using the simplest possible method due to lack of availability of chemicals, and me being a backyard enthusiast at the starting post.
I have had good success with plating bright steel nails using a bicarb soda solution with a very small amount of polyetheleneglycol added.
The plating seems to be quite robust, and has some depth to it, however, I don't think I am going to be able to achieve the thickness I require for the end game job, which is reducing the diameter of a reamed hole in a block of steel.
The thought occurred to me that the reason I am not going to achieve the thickness I require is that at some point, I am no longer trying to plate steel, but instead am trying to plate copper with more copper, which, if possible at all, probably requires a different process?
If it does, and that process is achievable with easily obtained chemicals and not a lot of expertise, then I'm all ears :-)
If not, then my plan was to plate with copper as above, then plate with nickel, then copper again, then nickel again until I get the required buildup.
Again, the nickel plating will have to be done in the simplest way possible, which will probably be using a vinegar solution, although I do have access to citric acid
⇦ this on
eBay
or
Amazon [affil links] and hydrochloric acid if either are a better choice.
Any advice would be greatly appreciated.
Cheers :-)
- Dardanup West Western Australia
A. Hi Phill. I would say that some of your observations and theories are correct: plating does tend to get "different" and softer as it gets thicker because the copper is no longer struggling to match the grain structure of the steel but builds up ever-bigger, softer, and more porous copper crystals. Thick copper electroforming is possible but it usually requires special additives to control the grain. Your ethylene glycol may offer such benefit but perhaps not as much as proprietaries specifically developed after significant effort.
Actually I see nothing "wrong" with your idea of alternating copper and nickel layers for a backyard enthusiast, but you should start with nickel because copper won't adhere properly to steel, and note that copper is quite soft as a replacement for steel.
Regards,
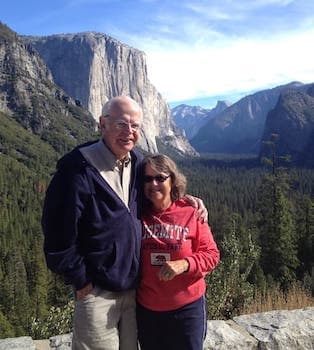
Ted Mooney, P.E. RET
Striving to live Aloha
finishing.com - Pine Beach, New Jersey
June 2020
Thanks for the response Ted.
The plating is inside a cylindrical hole in a tool holder, so will only ever have clamping forces applied to it to clamp it to the tool post, so basically under compression only. I am pretty sure the copper/nickel will survive that situation. Time will tell.
Best Regards.
- Dardanup West Western Australia
June 17, 2020
Q. I have done electroplating experiment with copper sulphate pentahydrate, Mixed copper sulphate salt in warm distilled water until it is saturated, Anode is copper metal plate, cathode I tried with different metals (iron, coins, steel). I also have tried different battery voltages, i.e., 3V, 6V, 12V (DC). The problem I am facing is whatever I have kept at cathode, the copper gets deposited but it comes off easily when I scratch it. Is there any way I can make this coating last for a long time? Not sure what is the error in my procedure.
Devanshi Doshi- Mumbai, India
August 10, 2020
A. Hi Devanshi. Getting copper to deposit is the easy part -- even 9 year old children have reported to us their successes with this experiment :-)
Getting good adhesion is a much more difficult problem. Make sure your substrate is copper, brass, silver, or gold; copper sulphate plating will not stick to iron or steel, or aluminum or nickel or stainless steel or zinc.
Then dilute the solution, you don't want it saturated. Then, while wearing rubber gloves, scrub the surface with a brush and pumice & detergent until it is absolutely clean, then connect the wiring and put the anode into the solution. Then with the power on, put the cathode into the solution.
The adhesion will be at least much better. Good luck!
Luck & Regards,
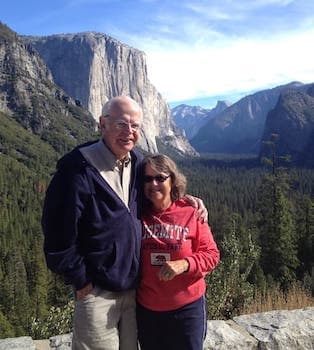
Ted Mooney, P.E. RET
Striving to live Aloha
finishing.com - Pine Beach, New Jersey

Q, A, or Comment on THIS thread -or- Start a NEW Thread