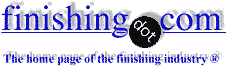
-----
Severe rusting of 15-5PH stainless America's Cup castings
We have had a severe problem with rusting of 15-5PH stainless investment castings. The parts are used in high performance yacht racing such as America's cup boats and the strength-to-weight ratio requirements require us to use a precipitation hardened alloy vs a 316 stainless. The rust problem has been a recent problem and the same alloy was used in the past with no problems. The castings come from a foundry and are double solution annealed and then heat treated to H1025 in a vacuum. They are then descaled using a wheelabrator. Once they arrive to us, this is our process:
1) We tumble the castings in a vibratory tumbler for 4 entire days until they are very smooth and all outside pits are removed.
2) We clean the parts in a boiling alkaline solution and then rinse them again in fresh water.
3) We electropolish the parts for about 15 minutes using a 50% sulfuric/50% phosphoric acid heated to 140 deg F.
4) We rinse the parts thoroughly in a series of 5 clean water rinse baths with the last bath heated to 130 F and then dry the parts immediately.
5) We have tried an intermediate bath using nitric so as to dissolve any salts but have had no real improvement.
6) The parts are next hand buffed using stainless buffing compound.
The resulting parts are mirror smooth and shiny and look like jewelry.
Recently, we have had severe rust staining occurring after exposure to sea water. We have verified this problem using a salt spray tester and such staining occurs within one day. Within a week the parts are so stained that you would think that they are steel. In the past, the parts would stay stain free for years. Something is terribly wrong. The staining can be removed with a wire brush and the underlying base is perfectly shiny. It seems that some iron contamination is bleeding drastically but it is hard to determine the exact spots.
(Click on pictures to enlarge them)
Here's what I have done:
1) Spectral Analysis showed that the alloy is indeed correct.
2) Passivation in 140 °F 50% nitric acid for 20 minutes. Rust disappears, but then parts still stain just as fast when put in salt water.
3) Passivation again for 2 hours and then tried another time for 24 hours. Parts still stain just as fast.
4) Re electropolish the parts. Still stain
5) Electropolish the parts for 10 times the normal rate. Staining is finally reduced but the parts are so electropolished that the dimensional tolerances are way, way out of spec and the part is useless other than for running this experiment.
Here's what I think may have happened:
Theory 1) When the foundry descaled the parts in their wheelabrator, they were supposed to use stainless steel blast shot. However, they also have a wheelabrator that contains steel shot. I think that they put our parts into the steel shot by mistake, and iron was impinged so deeply into the surface of the castings that it is impossible to get out. Seems like the staining comes from everywhere just like water coming out of a sponge.
Theory 2) There is some residual ceramic left over from the investment casting shell and it fused into the surface from what the foundry calls a mold/metal reaction. This microscopic ceramic coats the underlying stainless like 3 dimensional "paint" and the electropolish only seeps under the edges and not underneath. As a result, bleeding is occurring from deep under this ceramic. Looking at the microstructure under my Zeiss scope I can see what looks like maybe ceramic, but it is hard to determine if this is the case or if it may be some form of delta ferrite. Can't make any conclusions
Theory 3) May be something completely different. We have changed the electropolishing solution, changed the buffing, and tried to run experiments changing all parameters one at a time. Nothing is conclusive here. Maybe there is something we overlooked?
Any ideas or suggestions as to how we could stop this staining without ruining the parts would be greatly appreciated. Also, any suggestions of how we might identify the potential for such problems beforehand in the future. Thanks.
marine hardware/america's cup fittings - Mystic, Connecticut, USA
2004
Wow, quite an interesting problem. I bet this will receive a lot of responses. From my perspective, I agree that your two theories have identified a likely source (or sources) of the problem. First, was the solution annealing performed in a vacuum, or was it only for the aging treatment? Does the casting company do anything to remove the metal-mold surface layer prior to heat treating, or is the descaling after aging the only process used? Either way, it sounds like a strong pickling step would be better than the mechanical shot blasting.
With regards to contamination, you definitely need to rule this out. Does the casting/heat treating supplier perform a contamination test after the descaling operation? They should, and use one of the methods described in ASTM A380
(copper sulphate, ferroxyl, etc.). Also remember that even if the parts were processed in the "right" wheelabrator, the shot media can become contaminated and deposit iron on the parts if non-stainless steel or iron parts are processed in it.
Can you find out if your previous casting vendor used pickling instead of mechanical descaling? I would work with your current vendor to rule out contamination, and work eliminating the metal-mold reaction surface layer, as this will allow for proper passivation. ASTM A380
is a good reference for proper guidelines on cleaning and descaling. ASTM A967 has information on passivation techniques.
Automotive module supplier - Michigan
2004
Every alloy has a certain limiting corrosion resistance. You can't select an alloy that has inadequate inherent corrosion resistance for the service environment, then "wish" it into having better resistance.
See replies to thread 16305 in the archives.
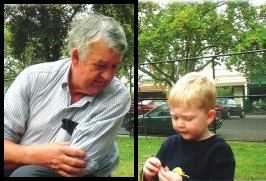
Bill Reynolds [deceased]
consultant metallurgist - Ballarat, Victoria, Australia
We sadly relate the news that Bill passed away on Jan. 29, 2010.
2004
After submitting a response, I re-read your posting more carefully, and this time I saw the bit about your having found the alloy to be OK in the past. I'm surprised it was OK before, as 15-5PH and 17-4PH usually don't stand up well at all in sea water. Nevertheless, your previous experience is clear, and suggests that I need to retract much of the message in my previous submission, and pay more attention to the difference that electropolishing can make!
Have the minor elements in the alloy changed? For instance, normally, if H1025 is to be done, there would be a deliberate addition of around 0.25 percent niobium to the steel which precipitates the residual carbon as niobium carbide. If that is omitted, there will be a reduction in the effective chromium content after heat treatment, as some of the chromium will be removed from solution in the form of chromium carbide.
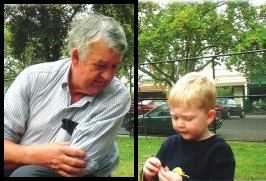
Bill Reynolds [deceased]
consultant metallurgist - Ballarat, Victoria, Australia
We sadly relate the news that Bill passed away on Jan. 29, 2010.
2004
15-5PH is not suitable for use in sea water service but it should be enough for marine atmosphere as corrosion resistance.
Just to give you an idea, our Aquamet 17(17-4PH cond. H1150) used as boat propellers shafting bar, suffers of corrosion problems in sea water service, but works quite well in marine atmosphere.
Apart that, we have to consider the production process. Cast pieces never offer the same corrosion resistance of rolled or forged bar produced by a mill for different reasons, not easy to discover. We suggest to evaluate different grades, like PH13-8Mo or Nitronic 50 HS.
PH13-8Mo offers a moderate better corrosion resistance but it's better as mechanical properties. Nitronic 50, is totally safe as corrosion resistance, offers lower mechanical properties but much higher than tp. 316
- Genoa, Italy
2004
I am interested in any successful non-acidic methods of descaling 17-4 PH and 15-5PH in the hot rolled condition, without any subsequent rusting or discoloration.
Gary W. Meaderspecialty metals - Syracuse, New York, U.S.A.
2006
I have recently de-scaled old cast iron using electrolysis and the electrolyte is a sodium carbonate
⇦ on
eBay or
Amazon]
solution.
The positive is connected to a piece of iron that is clear of rust, grease and dirt. Use lye to clean it (the metal will not be harmed). All the red iron oxide will cover the piece of iron.
The negative is connected to the work piece that is clear of grease and dirt. Use lye to clean it (the metal will not be harmed). For small items such as you have a small conducting basket can be used.
A 12 volt battery charger
⇦ on
eBay or
Amazon [affil links]
or other 12 volt DC supply is required. An ammeter should be present scaled to twenty amps. The process takes a while (overnight is good) but produces excellent results. On oxidized iron the part will come out dark grey or nearly black, this is a plating layer of black iron oxide. The original part will not be harmed whatsoever by this process and obviates the use of strong acids or 'pickling.'
The startup will show a low current, after some time the ammeter will show 9 or 10 amperes and should remain at this value. After the process is finished or close to being finished the current will rise and even slam against the stop.
This means the process is finished. You can apply light mineral oil to maintain the black oxide plating or you can pickle in acid to remove it.
- Surrey B.C., Canada
June 12, 2010
Hello,
For many years I used casting products 17-4PH made in China. I used it for product in the open air. More than a year ago new casting parts started rusting after about two weeks like steel. I cleaned it with several products, and after cleaning the parts look like new, but two weeks later they were brown again. So I asked a laboratory to investigate this problem. They found contamination in the melt. So the CrO2 was not 100% available because of the contamination. There were very small holes in the CrO2 layer so water could reach the iron. Now I use stainless steel 1.4410. This material I can clean before blasting in an acid bath which with 17-4PH is not possible. You will get pitting and the material becomes black. So probably the melt was contaminated; perhaps also in the cases mentioned before. It is a pity I cannot use or cannot trust 17-4PH because it is a strong material.
stainless steel - Leeuwarden, Netherlands
November 5, 2011
March 9, 2012
Let me introduce myself, before to go on.
I had the pleasure to be the Technical and Quality manager for 20 years of the most famous mill that invented PH and Nitronic grades, responsible of contacts with the production mill in Italy and technical support for all our Subsidiaries Commercial service in Europe.
Now I'm in pension and I spend a little time as a free consultant.
Concerning problems of rust on PH grades, 15-5PH or 17-4PH in marine atmosphere service, as a I answered a few years ago,it is my opinion that the main problems are connected with the production process and the poor quality of obtained pieces.
Cast PH grades cannot be compared with the true 15-5 or 17-4PH produce by a good mill. In my opinion not even to define these parts made PH grades is correct.
PH grades need a very special and accurate process and transformation cycle, differently we never find the real properties of these grades in the final product.
In the described parts we had a production by cast and parts made in China !!
Do you have any idea of the number of severe controls made in good mill before to release the product?
Which controls do they made on these pieces ?
Concluding: In 20 years of direct experiences in European market I never met corrosion problems on pieces obtained by
rolled or forged bars made by a good mill, fully certificate according to ASTM / AMS specs, for marine-atmosphere services, used in similar parts.
Also today the most famous producers in the world of these marine fittings, for sailing boats and general marine service continue to use mainly 17-4PH with good results.
Also important parts of marine-winches are made in 17-4PH from more than 20 years!
Totally the opposite for cast parts. Many different problems from people using molten or cast parts in PH grades. In these cases, is not really easy to help them, due to the total missing of clear and safe information on the production process.
- Genoa, Italy
March 18, 2012
After an accurate evaluation of your detailed description, I confirm my previous opinion.
I think your stain problem is really connected to the production process.
Possible reasons:
1)The melting process is not totally correct or it contains impurities that remain inside the structure.
2)Iron impurities are added to the pieces during the descaling or cleaning process.
Suggestions:
For case 1) no suggestion available.
For case 2) If the problem is due to the case 2, try to use a strong chemical pitting before polishing.
Hope this can help.
Ciao,
Pier Luigi
- Genoa, Italy
Q, A, or Comment on THIS thread -or- Start a NEW Thread