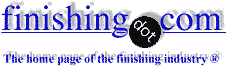
-----
Preventing aluminum from anodizing itself?
Q. Hi, Hope someone can help.
I am a small company and have invented and patented a small water softener for the food service industry. The unit is made of aluminum, and is cast using the lost foam investment casting method. There are 2 main components. The top measures H. 17" x W. 13" x D. 3.5". This component is made up of 4 equal square chambers that run the length. Chamber 4 is used for the salt regeneration chamber. Every couple of months 2.5 lbs of water softener salt is added to this chamber and the unit is regenerated. This process takes about 30 minutes. The rest of the time soft water is flowing thru it. The remaining chambers 3,2, and 1 contain water softener ion exchange resin.
Thanks in advance for any input. Alex P [surname deleted for privacy by Editor]
Water treatment - Sammamish, Washington, U.S.A.
2004
A. Chloride is the worst ion you get anywhere near aluminum or aluminum oxide. Electroless Nickel or Powder Coat are my best suggestions.
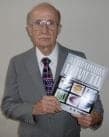
Robert H Probert
Robert H Probert Technical Services

Garner, North Carolina
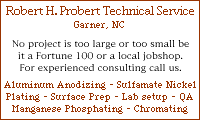
2004
A. Dear Sir,
what you have is aluminium corrosion, and for the best of my knowledge it will be difficult to protect by a traditional means, and I'm concerned if regarding the D.I water, it may contain particles of the disintegrated resin. Just thinking why not make it out of plastic, sorry! good luck
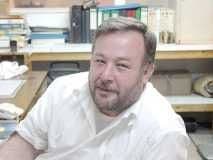
Khair Shishani
aircraft maintenance - Al Ain, UAE
2004
A. Good afternoon,
It's hard to picture this in my head, but if I'm close I would suggest...
1.Extrude hone the casting and then hard anodize.
2.Sleeve it like an engine block.
3.Have it made out of an extrusion instead of a casting.
Sorry if I'm too far off of the mark, it's all I can think of. I can't imagine a coating that will hold up for very long under those condition.
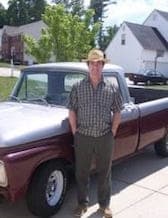
Sheldon Taylor
supply chain electronics
Wake Forest, North Carolina
2004
A. Good Afternoon,
I believe the combination of harshness of liquids and porosity of the casting are contributing factors. Have you given consideration to a Forging?
Good Luck,
- PLATTSVILLE, ONTARIO, CANADA
2004
A. Electroless nickel would be a good option for you. If you find a plating shop, make sure you use one that has a mid phosphorus or high phosphorus bath. These are better for corrosion resistance. Make sure the coater knows your application. Also let them know if the piece has been welded, and what has been used.
Shane Stephens- Keene, New Hampshire
2005
Q, A, or Comment on THIS thread -or- Start a NEW Thread