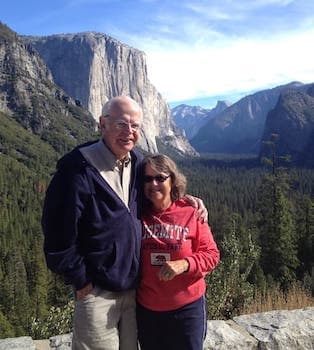
Curated with aloha by
Ted Mooney, P.E. RET
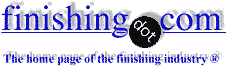
The authoritative public forum
for Metal Finishing 1989-2025
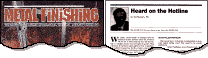
-----
Nickel Oxidation, Zinc Oxide, Oxidation Removal and Reference
2004
Hello everyone,
I thought that I might post a few questions over this listserv to see if anyone might be able to help me out with some info I've been searching for in regards to metallic oxidation. I'm currently a graduate student at the University of California Berkeley doing research in Microelectromechanical Systems (MEMS). In particular, I'm working on the bonding of silicon MEMS devices to non-silicon based materials...like metals. My questions relate to the finish of the metal (and have not, to my knowledge, been posted on this site), so I felt as though this was an appropriate site to which to post. If my questions seem rudimentary, however, please bear with me...here goes:
1) I've been looking for some data on the oxidation rates of nickel and zinc. In particular, I was wondering if anyone knows how fast oxidation will occur on pure nickel and pure zinc. Obviously, when the oxide is stripped, these two metals will form a native oxide quickly, but I was wondering how thick that oxide is, and perhaps how fast the oxide will continue to grow. Is the native oxide on the order of tens of angstroms at room temperature, or will it grow to maybe 100's of nanometers within seconds? I would imagine that they are both self-limiting oxides at room temperature, so what kind of thickness are we dealing with at room temp, and how quickly does it take to reach that thickness? Essentially, is the oxidation growth at room temperature similar to aluminum, which grows a thick, stable oxide VERY quickly, or do these metals allow a small window where you have basically pure metal exposed (with an angstrom level oxide present for a period of minutes) after stripping the oxide?
2) Are there any good chemicals to remove oxides without forming some kind of reactive product on the surface of the metal? For example, I've been thinking about using diluted HCl (which I believe is the active ingredient in basic flux) to remove something like copper oxide, but I've been concerned about depositing a metal chloride on the surface of the metal. Copper aside, any suggestions for removing nickel oxide or zinc oxide without depositing an unwanted reaction product on the surface of the metal would be greatly appreciated.
3) Are there any good references that anyone can think of that go into the oxidation growth profiles for various metals at different temperatures? I know that it's all case dependent, and I'm not expecting a single graph or equation (as oxidation is a complicated process depending on temperature, time, composition, configuration, pressure, etc), but any reference that anyone could suggest would be very helpful in me answering my own questions about oxidation.
Thanks in advance,
Brian
student - Berkeley, California, USA
I have similar questions. Technical information on cleaning NiO from NI can be obtained at www.alconox.com They have recommended that I use a product called Citranox Citranox [affil links] to remove NiO from Ni. I believe that at room temperature, the oxidation process is slow. Obviously tests could be performed by sputter etching an oxidized surface while measuring oxygen count in an EDAX. I don't happen to have this equipment. If you find out more, please let me know.
Thomas E. Salzer- Bedford, Massachusetts
2004
Hello, please check the following address for Peraldi paper on "high temperature oxidation of high purity nickel :oxide scale morphology and growth kinetics" in on line material paper at journal of "materials at high temperature" 20(4) 649-655 www.scilet.com/
S-Kiani- U.A.Emarate
2005
We have performed similar tests using an ellipsometer to measure oxide thickness on smooth metal and semiconductor surfaces. If you can clean insitu on the measurement tool (usually with dilute acids), you can measure oxide growth versus time pretty easily.
Marvin Bernt- Kalispell, Montana, USA
2005
If you want to get a nice surface for silicon bonding to Nickel try using a peroxide bath at 10 percent by weight and reacting some nickel powder. The evolution of H2 gas lets you know it is working. Take the nickel out and bond the silicon. Supposed to leave a nice finish on the nickel for silicon binding.
William Haskins- spring, Texas
July 27, 2009
Q, A, or Comment on THIS thread -or- Start a NEW Thread