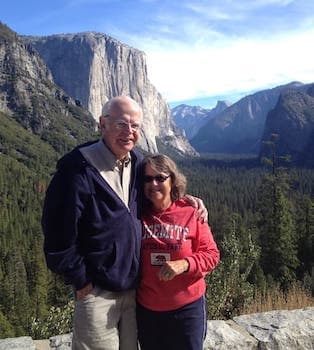
Curated with aloha by
Ted Mooney, P.E. RET
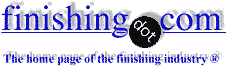
The authoritative public forum
for Metal Finishing 1989-2025
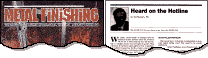
-----
Plating failing in salt spray although thickness is maintained
I am a design engineer designing automobile components for all leading OEMs in India .
For withstanding 120 hours of salt spray testing , I have given a plating thickness of 13 microns for Zinc Chromate passivation .
But now,although the coating thickness is measuring 13 microns , it is failing at around 75 hours in the salt spray test .
I am puzzled and don't know what might have gone wrong.
Require some guidance on this issue.
Automobile component manufacturer - Bangalore, Karnataka, India
2004
First of two simultaneous responses --
Dear Sir,
You have not mentioned the type of plating whether Acid Chloride system or Cyanide plating. However, I suggest alkaline cyanide free zinc plating process with Tri / Hexavalent chromate on top with sealant will give 120 hrs Salt spray life to white rust. Also, 250 ~
300 hrs SST Life for white rust process available with Alkaline cyanide free system with yellow chromate (Hex / Tri) with top coat sealant. This process is already available in south India on production line.
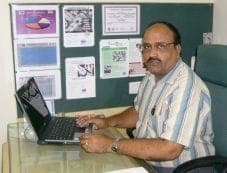
P. Gurumoorthi
electroplating process chemicals - Chennai, Tamilnadu, India
2004
Second of two simultaneous responses --
HAVE CHECKED THICKNESS AFTER CHROMATING , LONG SOAK MAY DISSOLVE SOME ZINC.
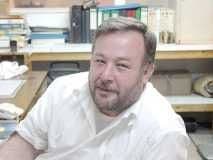
Khair Shishani
aircraft maintenance - Al Ain, UAE
2004
Salt spray protection - with 13 microns of plate parts should not have failed ss. Did the parts fail red at 75 hrs.? or was this white? My company currently produces very high volume automotive components and has been able to achieve 120 to white and 240 and beyond to red. The results were achieved with only 12 microns and no sealer. In some cases were the parts are not left in the chromate for the appropriate amount of time, the sealer can actually harm the layer of chromate protection causing ss failure.
John
- North providence, rA. USA
2004
POOR SALT SPRAY:- DIP PH LOW, CONTAMINATED DIP, DRYING TEMP HIGH, CHROMATE CONTENT OF DIP LOW, CHROMATE BURNISHED IN RINSING/DRYING. SO ASK GUIDE LINES FROM YOUR SUPPLIER.
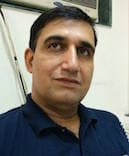
Ajay Raina
Ludhiana, Punjab, India
2004
With regards to the response of Mr.John.M.Langello, can he please tell us the following:
-- Any special process related do's & don'ts by which 120 hours of SS resistance was achieved before white rust with 12 microns and no sealant.
--- Was the above achieved with blue passivation or yellow ?
--- What is the ideal time to cure after chromate bath ?
Automotive component supplier - Bangalore, Karnataka, India
2004
Hello...
If you exactly sure for zinc plating thickness about 13 micron, it's impossible getting rust around 75 hour.Then we must think different reasons.For example your salt spray testing specification incompatible with current specification. So, Maybe your salt concentration high level or your test water has high chlorine,not distilled water.So in my opinion check your salt spray specification.And you can send these parts to different laboratories for comparing and measure thickness as a diagonal test.
Good Luck....
May it be easy...
- Turkey,Istanbul
2004
June 20, 2009
Hello Mr. Chaterjee,
All this mainly depends on chemical source used .
1. Use chemicals from
SurTec, Chemetall or Atotech.
2. Passivation bath needs to be maintained at 60 °C
3. pH maintain around 1.9
4. Passivation dip time 45-60 sec.
5. Use sealer.
If you follow these things, the Salt spray test 120 hrs minimum guaranteed.
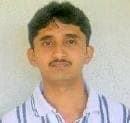
Sandeep S V
- Bangalore, India
Q, A, or Comment on THIS thread -or- Start a NEW Thread