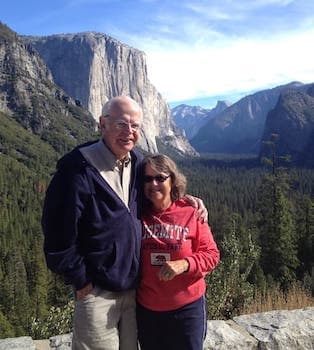
Curated with aloha by
Ted Mooney, P.E. RET
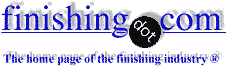
The authoritative public forum
for Metal Finishing 1989-2025
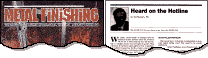
-----
PP Tank for stainless steel pickling
I work at a company that renders plastic welding services and I am trying to help a customer. I have a problem and I don't get answers, no matter how much I research! I would like to know if somebody can me help me. I have a customer who has a tank operating with nitric + HF + water, for stainless steel picking. This tank measures 66 ' x 8 ' x 3 ' deep. (It's a big tank). This tank is manufactured form 1-1/4" thick PP sheet.
This tank has operated 7 years now, and it presents welds flaws. This useful life was foreseen when it was installed. Now, this customer intends to manufacture another tank to substitute for the damaged tank, however, they don't have the specifications of the production of the old tank where the material is discussed. Which would be the best PP for this application? Random? Homopolymeric ? Copolymeric ? Does anybody have experience with similar applications?
Franz RotterProject - São Paulo, Brasil
2004
First of two simultaneous responses --
Polypropylene is a poor choice since nitric acid oxidizes the plasticisers. The weld process has all ready burned out some of the plasticisers. I would look a polyethylene. It is harder to weld very well and requires an inert gas to prevent charring around the weld. Another thought, would a vinyl liner work? A lot cheaper, but it will not take a lot of physical abuse. I would look at one that is 3/16 thick.
James Watts- Navarre, Florida
2004
Second of two simultaneous responses -- 2004
Hi Franz,
Re your mega tank holding both nitric and HF, may I suggest another tack?
This is what is now called, as you may well know, a dual laminate. But WHY PP when nitric is involved as you'll eventually get stress cracking? Why not PVC (which is far better in nitric as PP)... but as a dual laminate in which case its operating temperature jumps from max. l40 to l50. See please the archives #
8169 as well as #
8691 and maybe #
9132 ^7132.
The dual laminates, ... or armoured thermoplastics, as I used to call them .... have a lower coefficient of thermal expansion than the straight thermoplastic and, due to the fibreglass reinforcement, a somewhat higher operating temperature.
I hope that this is of some help.
Cheers !
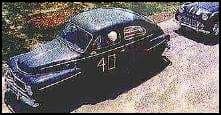
Freeman Newton [deceased]
(It is our sad duty to advise that Freeman passed away
April 21, 2012. R.I.P. old friend).
Hi Franz Ah, I made an error is saying have a gander at # 9132 ... that should have read # 7132. Viele Entschuldigungen, Mensch! By the way, both PP and Pe are from the olefin family ... and BOTH dislike oxidizers.
The idea of a plastic liner is an option BUT eventually the nitric will leach out the plasticizer, which I why I had suggested a dual laminate. Were you to go to a PVC liner, make damn sure that its thickness is as heavy as possible ... in order to retard the oxidizing attack.
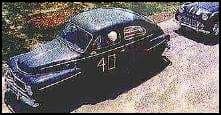
Freeman Newton [deceased]
(It is our sad duty to advise that Freeman passed away
April 21, 2012. R.I.P. old friend).
2004
Dear Freeman Newton
I would like to complete the information: The operation temperature is of 149 °F that surpasses the suitable temperature for PVC (140°F). Today the PP tank , with the used resin, presents oxidation of 0,06Ÿ / year. This PP is mattered and we don't know the composition. A similar tank was manufactured with material national PP copolymer and it presents an oxidation of 0,2Ÿ / year. We didn't get to discover what type of PP was used in the original tank.
Franz Rotterpart - São Paulo, SP, Brazil
2004
2004
Hi Franz,
As mentioned above, if you use a dual laminate, the operating temperature CAN BE INCREASED.
For PVC:FRP it's not 150 but l75 ... and there was a case history of using the Trovidur red PVC at 195 degrees F ... Wow! But that PVC is probably the top PVC in the world, more brittle than others and certainly has a higher resistance to sulfuric ... where all PVCs excel.
As a matter of interest, after the war, a UK inspector was going through a German chemical plant and saw this red piping which flummoxed him completely ... all the then conventional materials were alloys or lead or glass. Yes, Germany invented PVC.
If you wanted corroboration on the operating temperature of the PVC:FRP dual laminate, contact Enrique Ginoccio, P.Eng. of Prolite.
By the way, the world's first successful dual laminates were made by Alcore Fabricating in Ontario back in the early 60's.
I hope that that puts your mind at rest! By the way, but this is something I'm sure you'd know, it's the bond between the thermoplastic and the FRP that is critical. We used to use conductive tape at all welds in order that the finished product could be easily spark tested.
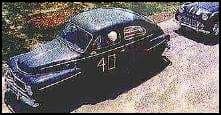
Freeman Newton [deceased]
(It is our sad duty to advise that Freeman passed away
April 21, 2012. R.I.P. old friend).
Q, A, or Comment on THIS thread -or- Start a NEW Thread