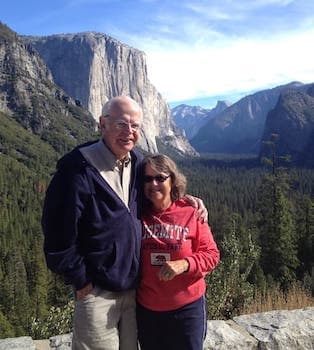
Curated with aloha by
Ted Mooney, P.E. RET
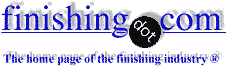
The authoritative public forum
for Metal Finishing 1989-2025
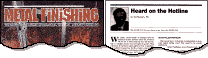
-----
Removing compressed metal powder from an internal cavity
2004
Dear,
I would like to introduce myself; I am Kailesh Raja Chelladurai a Master's Student doing my MSc. in Manufacturing System's Engineering at University of Warwick. As a part of my course I have to do a project work for the degree completion.
The project I am working right now is about Rapid Manufacturing (RM). The unique feature of this RM is that it can produce any component or any complex shapes from the CAD data to the Solid model by melting the H13 Metal Powder using the Electron Beam. This state of art has an advantage over the others by being 100% density over the product or part produced. And I am working on this machine to bring out its capabilities and limitation of the design that it can work in. I am trying to build a unique shape that is internally built in the model.
Basically the model that I am trying to build in this system is a tool insert for a plastic injection-moulding component. The insert has an internal cooling system that is shaped like a spring coil. The problem now I am coming up with is that I need to get out the compressed powder or the slightly sintered powder from those internal cooling channels. The technology behind this system is that the powder is melted layer by layer using an electron beam and then the powder is shredded over the next layer and then it is again melted and thus obtaining the entire part. When they do this melting process they leave out the areas were we are not having materials to fill (were we are having a cavity), and melt the rest of the areas around. But due to the heat transferred from the molten metal powders the un-melted powders gets compressed. And stay in those cavities. Now we are facing few problems in removing those metal powders, basically it's a compressed powder, way form those complex shape cavities. We have tried with the compressed air, and compressed water jetter even, but the results are not so good. Then we came up with an idea of using an ultrasonic cleaning and we tried to use the machine that we have in our University which is a table top model with a low frequency and power, but we could see some good difference in the removal rate of the powders form the cavity (very small amount was removed which is not worth mentioning). I would like your suggestions on this problem. This information would really help me out in further progress in my project.
Thanking you With regards
Kailesh Raja Chelladuraistudent - Coventry, Westmidlands, U.K.
2004
You are asking some very complex questions that may not be answerable. Furthermore, you are studying at a very reputable university, where part of your education is to learn to think for yourself and solve your own problems. Without this fundamental training in problem solving you will always be dependent on others to solve your problems and this will not be any good when you reach the stage at which you can consider yourself to be "technically competent".
Saying all that, I think you have numerous issues that you may want to address in solving your problem. Firstly, it sounds as if one of your problems is that you are partially sintering the metal powder with the electron beam in areas you do not want to sinter it. You may be able to resolve this by better control of the electron beam power/pulse/speed etc. You may be able to prevent the problem by using larger and more uniform sinter particles. If you have a wide spread of particle sizes you will inevitably get interstitial filling by the smaller particles and this will lead to agglomeration of the larger particle matrix by preferential partial sintering. If you are indeed getting this problem, you will have to find a way of machining the rogue sinter off the walls. I am not sure that even high powered ultrasonics will be of any good, unless you can use the technique to generate localized ultrasonic cavitation and preferential erosion. The simplest solution is to find a way of preventing the problem in the first place, not a way of rectifying the problem once it has arisen. Also, since the part is for a mould tool remember your basic mould tool design requirements.....
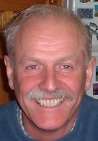
Trevor Crichton
R&D practical scientist
Chesham, Bucks, UK
Q, A, or Comment on THIS thread -or- Start a NEW Thread