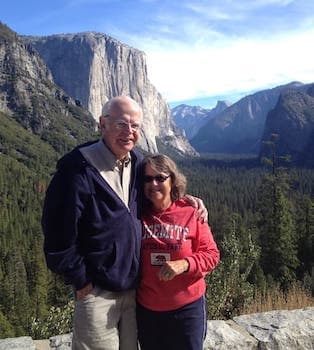
Curated with aloha by
Ted Mooney, P.E. RET
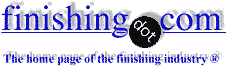
The authoritative public forum
for Metal Finishing 1989-2025
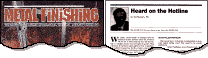
-----
Magnesium builds up in our closed loop ion exchange system
2004
I run a metal finishing jobing shop (30 staff)which is one of the largest in Queensland.We powder coat,thermal spray,chromate finish etc. We have 3 different coating booths with one being a semi auto line. We used to run an effluent plant and batch treat our waste water but came across DI system for our final rinse water (approx. 2 years ago)closed loop system. Upon advise we thought we could get away from batch treating our waste and set up a 2nd closed loop system and just replace the cylinders when required. This has produced a high amount of magnesium in the rinse water that the cylinders can not handle.
My question is can a DI system be made to handle what I'm trying to achieve or is there such an animal (system) on the market (I'm unable to find the answer out here I keep getting different opinions) NO hard facts to base a decision on. Any assistance would be greatly appreciated.
Thank you,
Trevor SwanssonPowder coating shop - Brisbane, Queensland, Australia
It is difficult to understand why there is an excess of magnesium in the recirculated water. This means that either the cation exchange resin is exhausted or that the anion resin is fouled with magnesium. However, if the cation resin was exhausted, before magnesium was released, the cation exchange resin would first release all of the sodium and potassium that it held.
If these are exchange tanks that are regenerated off-site, then it is possible that they are not regenerated fully,or that the anion exchange resin is fouled with magnesium.
It would be easier to give some advice if you could report the pH, conductivity and the magnesium concentration that is of concern.
Lyle Kirmanconsultant - Cleveland Heights, Ohio
2004
Q, A, or Comment on THIS thread -or- Start a NEW Thread