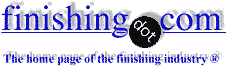
-----
Hot dip galvanizing temperature control
Q. Hi Technical members!
I need to know a suitable way to control temperature of my zinc pot during galvanizing. Could anyone suggest a method of doing so. I will really appreciate your advice in this regard.
Best wishes
Anand
Anand KSriram Hot Dip Galvanizers - Bangalore, Karnataka, India
2004
by NACE
[only rarely available]
on eBay or Amazon
or AbeBooks
(affil link)
A. Dear Mr. Anand
Please be specific about you problem. Let us know about Zinc bath capacity, details of Process like continuous or batch type galvanizing Process. You may use Diesel or Gas fired heating systems / Resistance heaters with controlled devices or Induction Heating system, It all depends upon system requirement and suitability of Process for economical reasons.
Regards,
Aditya Chaturvedi- Surat, Gujrat, India
2004
Q. We have a port for hot dip galvanizing but we have a need to control the temperature of zinc port whereas between 440 and 450 °C and the hot air temperature (burners) between 550 to 560 °C, currently we have the PID system in which when the hot air temperature reaches 555 °C it will then close the motor Modutrol valve thus preventing air supply to the burners and when the temperature goes down to 553 °C it will then opens the valve and allowing air to go in and the temperature will shoot up. By controlling the hot air temperature we can control the zinc temperature as well but the problems are often the temperature for zinc port and hot air goes up and down exceeding the limits sometimes ± 20 to 30 °C.
So what I can do to control the temperatures as desired as I wanted or maybe designing another system to do this but how to achieve it? Please advice?
Many thanks,
Hamish [last name deleted for privacy by Editor]mast pole manufacturer - Ipoh, Perak, Malaysia
2004
![]() |
A. If I understand correctly, your system senses the Hot Air temperature then opens or closes the fresh air supply to the burner. First, the control should vary the air supply smoothly between open and closed, maintaining the air valve in a partially open condition. Perhaps the air valve is sticking and not following the control commands. Another possibility is that there is draft of cold air getting to the temperature sensor. I've also seen temperature sensors become intermittent with age; or there may just be a loose connection to the sensor or to the Modutrol. Or maybe the PID controller has a problem. Tom Gallant- Long Beach, California USA 2004 A. PID stands for proportional-integral-derivative control, which is a control algorithm designed to allow you to solve such problems. It is intended to be fine-tunable so that air feed is proportional to the error, while monitoring the total error over time to integrally close in on perfect conditions, while derivatively responding instantly to quick changes in conditions. Sometimes these systems are self-learning, sometimes you have to adjust the proportional, integral, and derivative components. While there is clearly the possibility of maintenance issues as Tom notes, it may be that you need an instrument technician to adjust the PID parameters. ![]() Ted Mooney, P.E. Striving to live Aloha finishing.com - Pine Beach, New Jersey 2004 |
A. Your problem is not too complex. You are trying to control the temperature in the galvanizing bath by controlling the temperature in the heating chamber that is around the kettle that holds the molten zinc. There are some basic issues to understand, the first being that you need to know the zinc temperature and control the burners by that temperature, not the furnace. Controlling the air flow is common practice for powered burners, and the gas usually is controlled proportionately by by sensing changes in air pressure. Controllers should be proportionate, and can be adjusted to suit your needs very easily. Any good system may see temperature fluctuations as mush as 6-8 °F. Any more than that should not be acceptable.
David JayeHouston, Texas
2004

Q, A, or Comment on THIS thread -or- Start a NEW Thread