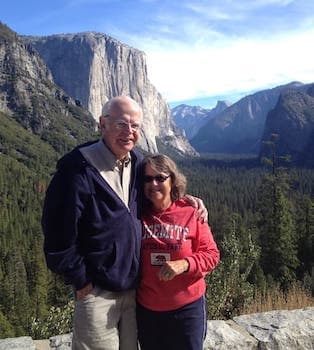
Curated with aloha by
Ted Mooney, P.E. RET
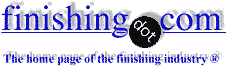
The authoritative public forum
for Metal Finishing 1989-2025
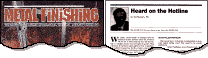
-----
Expired Zinc Chromate Polyurethane Coating
Q. I am the Engineering manager of a small aerospace manufacture. We currently have a requirement to paint a magnesium casting with Zinc Chromate Polyurethane Coating Paint to Consist of Miller Protective Coating Inc. Of Bridgeport CT. NO. P-2534 Resin No. E-2477 Catalyst & No. T78A Reducer according to the following proportions 1 part by volume resin & 1 part by volume catalyst then mix approx. 3 parts by volume with 1 part by volume reducer. Apply coating to THD of casting & insert. Air dry 2-3 minutes prior to assembly with seal. After assembly air dry 72 hours min or bake at 180-200 °F for 1 hour min.
The problem we have is that the manufacturer, Miller Protective Coating Inc. of Bridgeport CT., is out of business. I would like to know what specification or industry coating would meet the intent of this Zinc Chromate Polyurethane Coating.
William GanoeManufacturing/ Process Engineer - Vernon, Connecticut, USA
2004
A. First of all, We are an NADCAP controlled aerospace painting facility and use many products for many customers.
Your problem: The primary intent is "corrosion control" as applied to threads and inserts, which we do here also. Zinc Chromate has proven itself as a very effective "wash primer" for decades now. The phosphoric acid in the mix etches itself into the metal while the zinc reacts with moisture and combats it whenever it is present.
We also use strontium zinc primers that work very well indeed, however some people and organizations do not wish to use it. If it is misused, there are some effects that are not welcome to the environment.
It sounds like the requirement for the Miller coating wanted a corrosion preventative but with more resiliency due to the polyurethane vehicle. Polyurethane is tough and withstands ultraviolet rays very well--better than epoxy. You should not exceed .0005 dry film thickness for corrosion prevention. MIL-C-8514 [from DLA] post treatment (like wash primer) works well. Use it with epoxy primers made to MIL-PRF-23377 [⇦ this spec on DLA] H. These two together will resist most everything. MIL-PRF-23377H provides for an epoxy primer we use for corrosion prevention--type II class c, high solids--bad stuff, but well worth it! Also check out TT-P-1757 [⇦ this spec on DLA] Alkyd primer, type II class C--chromate based inhibitors. This would be more to polyurethane than the epoxy would, but believe me ... all of the above will do the trick.
Good luck
Bill Workman- Phoenix, Arizona, USA
Re-qualify expired paint catalyst
Q. My catalyst is beyond the expiration but my can has never been opened. Is there a way I can do a test to re-qualify it for a longer period of time?
nek platosshop employee - Los Angeles, California
February 12, 2019
![]() |
A. Hi Nek, Aerospace - Yeovil, Somerset, UK A. Hi Nek, ![]() Rachel Mackintosh lab rat - Greenfield, Vermont |
Q, A, or Comment on THIS thread -or- Start a NEW Thread