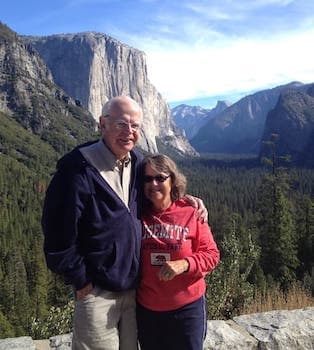
Curated with aloha by
Ted Mooney, P.E. RET
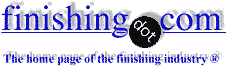
The authoritative public forum
for Metal Finishing 1989-2025
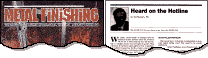
-----
Surface treatment of stainless steel garden furniture
2004
We are a distributor of garden furniture, primarily selling our products in Scandinavia. We design the products in Denmark but have them produced with sub-suppliers in Thailand. Until a few years ago our products were produced in teak only, but in the later years the demand has shifted more towards hybrid materials such as teak and stainless steel.
Consequently we have launched 3 new ranges of furniture where the frame is made of stainless steel, and the parts getting in contact with the body are made in stainless steel. Now and then we experience complaints from customers who have corrosion on the surface of the furniture. We have now included a removing/scrubbing paste with all steel furniture, and it works, but it is an irritation for people buying costly furniture.
The process we use today is 304 stainless steel that are glass blasted, passivated with nitric acid and finally treated with oil.
What I would like to know is, whether there is a surface treatment which is economically viable but offers a better corrosion resistance than glass blasting.
Jørgen Purupstainless steel garden furniture - Hadsund, Hadsund, Denmark
Glass beads would be a very expensive option to blast stainless steel material and is only used to blast high safety of precision stainless steel fabrications.
You could try and use SILVER SAND to blast stainless steel. It should be a much cheaper option and I think it should be the most appropriate option for you to adopt as my guess is your blasting quantum should be relatively large.
Regards,
Shantanu NewarMETALLIZING. - Calcutta, W.B., India
2004
First of two simultaneous responses --
Hi Jørgen,
I think your problem is in the passivation rather than glass blasting. Have you tested your products for free iron after passivation ?
Bo KönigFood industry - Odense, Denmark
2004
Second of two simultaneous responses --
Passivation will give you temporary corrosion protection; but the long lasting solution would be to chrome plate directly on Stainless steel, which would last 25 years out in the sun.
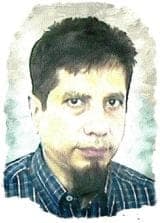
Khozem Vahaanwala
Saify Ind

Bengaluru, Karnataka, India
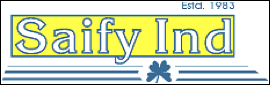
2004
2004
Not sure if you can get the strength you need, but 316ss would be excellent for this application, even if near the seashore. Good passivation is necessary, of course. Independent test data shows that the best passive layers are obtained by citric acid formulations. These are available in Thailand. The passivation must occur soon after parts are made, not after shipping across the ocean.
Let us know if you need references there.
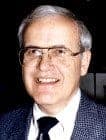

Lee Kremer
Stellar Solutions, Inc.

McHenry, Illinois
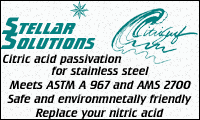
I want to know the citric acid formulation for passivation of stainless steel.
D.Kanagaraj- Chennai, Tamil Nadu, India
2007
September 17, 2009
Jorgen,
If you can, use 316 s/s as it is more resistant to corrosion than
304. Also make sure the glass beads used to blast the stainless is not contaminated with iron from other beading processes.
To increase corrosion resistance of 304 and 316 s/s try electropolishing as the last step in your manufacturing. Beware though the electropolishing will brighten the surface finish to a higher luster than passivating.
electropolishing shop - North Vancouver, British Columbia, Canada

this text gets replaced with bannerText
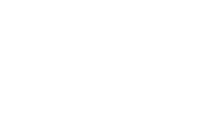
Q, A, or Comment on THIS thread -or- Start a NEW Thread