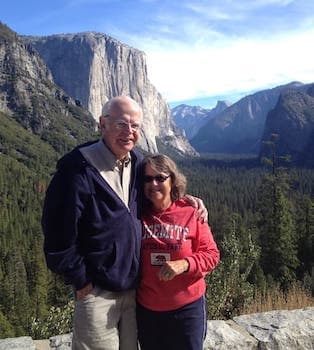
Curated with aloha by
Ted Mooney, P.E. RET
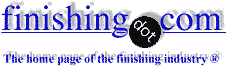
The authoritative public forum
for Metal Finishing 1989-2025
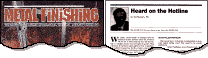
-----
Anodizing ampere-time calculations, surface testing and general questions

Q. Hi!,
I am Tobby; I have read about the 720 rule in Anodizing but no one has ever mentioned the sulphuric acid concentration to be put into consideration. I will appreciate if anyone could share more light on this.
1. I operate a Sulphuric Acid anodizing bath
2. My concentration is within 180-200g/l
3. I operate the 60XX series alloy of aluminium.
4. My target is to get coating thickness of 7-11 microns.
- Lagos, Nigeria
July 15, 2024
A. Hi Tobby. Robert Probert suggests 165 g/l to 180 g/l in his "Aluminum How To" ... your range sounds far too permissive. But in terms of calculations, the concentration doesn't control the thickness -- the ampere-hours does.
The thickness you seek is quite conventional but you really need a hall-effect thickness meter rather than trying to guess at thicknesses based on ampere-hours because things can go wrong like uneven thickness, broken contacts to the whole rack or just some objects on it, mistakes in logging anodizing time, etc.
(True that this particular thread didn't formerly concern itself with sulphuric acid concentration; it focused more on the 720 rule, but it's only one of 60,000 threads in this forum. Please search the site for any subjects that interest you :-)
Luck & Regards,
Ted Mooney, P.E. RET
Striving to live Aloha
finishing.com - Pine Beach, New Jersey
⇩ Related postings, oldest first ⇩
Q. I have been dabbling within the realm of type II anodizing for some time now and have been producing what appears to be a good solid anodized surface on small parts which I have machined from 6061 aluminum. I have some parts which are just anodized and some parts which have been anodized and dyed. All of these sample pieces appear to have a good solid finish on them (strictly a visual assessment & scratch test).
My current anodizing tank is setup as follows :
- 5 gallon plastic tank
- 25% sulfuric acid 75% distilled water solution
- (2) 1/8" x 2.5" x 14" aluminum strips as cathodes
- 12 volt manual
battery charger
⇦ this on
eBay or
Amazon [affil links]
(2 amp - 10 amp - 50 amp settings)
by S. Kawai
on AbeBooks (rarely avail.)
or eBay
(rarely avail.)
or Amazon
(rarely avail.)
Wasn't available from any of these sources last time we checked, but we'll maintain the links in case a copy turns up :-)
(affil links)
I have shown some of my anodized work to my brother who operates his own custom machine shop. Out of pure coincidence he told me that he is looking for a shop to contract out an anodizing job which will consist of approximately 250,000 pieces/year (4" diameter by 3/4" thick plates). He grew extremely interested in my ability to anodize while my interest grew with the thought of setting up my own anodizing shop. Though I would in NO way consider taking a job as large as 250,000 parts/year to begin with, my brother has stated that he could have his parts anodized at a larger shop while I anodize a small percentage of his 250,000 piece contract.
My father, two uncles, my younger brother and myself are all Journeyman Tool & Die Makers/Machinist. My father is the foreman of the Tool Room, foreman of the Maintenance Department and the sole machine purchaser for the multi-million dollar company in which he has been employed for nearly 40 years. I have two uncles who are both Journeyman Tool & Die Makers/Machinists and foremen in the companies for which they are employed. My brother has been running his own CNC equipped machine shop for over a year now while turning a splendid profit and I have been a Journeyman Tool & Die Maker for several years. As you can see we are a family who is dedicated to the metal fabrication business, who understands the complexity of running a shop, has an excellent understanding of machinery, tolerances and equipment. As an added bonus we all have some excellent contacts from where we can purchase new and used machinery and equipment for reasonable prices.
Having said that I do have some questions which follow :
Question #1 : In order to organize some kind of Quality Control department, what equipment would best suite a small, industrial anodizing shop in regards to testing for abrasive resistance and the depth of anodizing?
Question #2 : What other characteristics of the anodizing would most commonly be tested? I do realize that this can be directly related to the function of the part.
Question #3 : I am currently anodizing small parts using a manual 12 volt battery charger ⇦ this on eBay or Amazon [affil links] . I intend on upgrading to a rectifier should I pursue and expand this shop idea. What size of rectifier or would a rectifier even be recommended in order to anodize 50 piece batches with each piece producing 40 square inches each (2000 square inches or 13.88 square feet in total per batch)?
Question #4 : Currently I am simply running my anodizing tank for a single batch once a night or so and temperature has not yet been a factor. Should I move onto a larger scale, I will want to maintain a certain temperature range in my tank in order to produce consistent results. What is the most cost effective way to cool the solution in the tank? I have considered pumping water through a radiator and circulating it through plastic pipes running throughout the tank. Would this be advisable?
Question #5 : I have come across calculations on the internet in regards to the anodizing duration. Though these calculations have proven to work for my small parts on a small scale I am unsure if such mathematics will be sufficient on an industrial level. Currently I am using the following formula (the 720 rule as best as I understand it): (Constants) Current Density = 4-12 AMPS per 1 sq foot of surface area Amp Minutes = 720 Amp Minutes per 1 sq foot of surface area (Formula) Duration Required = 720 * Desired Thickness / (number of AMPS per square foot utilized) For example : A part utilizing a Current Density of 12 AMPS per 1 square foot with a desired anodizing thickness of .0002" (2 ten thousandths of an inch) would require the following duration : Duration = (720 * 2 ten thousandths of an inch / 12 AMPS per square foot) Duration = (1440 minutes / 12) Duration = 120 minutes or 2 hours
Question #6 : In my previous question, the current Density from which I make my current calculations is anywhere from 4-12 AMPS per square foot of surface area (I simply choose a number in that range - there is no science involved). I have read of people utilizing 30-40 AMPS per square foot. Is there a general rule of thumb in regards to this or is the sky the limit?
Question #7 : What sort of environmental precautions should be considered when operating an anodizing shop? If I choose to proceed with this venture, ecological and environmental concerns and correct procedures will be taken very seriously!
I realize that I have bombarded you people with some intense literature here. For that I apologize, however, through reading many of the threads posted on your forum I have come to realize that you can NEVER provide the teacher with enough information when attempting to have a question answered. I thank each and everyone of you who respond. If I seem somewhat ignorant to the world of anodizing I must apologize. Everything I know about the subject has been self taught.
Another note. If I have given the impression that I expect to wake up one day and just have an anodizing shop in my back yard capable of kicking out 250,000 pieces per year - again I must apologize. I in no way expect this to happen overnight and I realize that there is certainly going to be a cost involved. Furthering my education on the subject is a must and I realize that. This is part of the reason why I am here.
Thanks so much for your help and expect me to post back with follow up questions and comments. Also please feel free to respond directly to me.
Cheers!
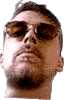
Daniel DeGueldre
anodizing shop entrepreneur - Ste. Anne, Manitoba, Canada
2004
Treatment &
Finishing of
Aluminium and
Its Alloys"
by Wernick, Pinner
& Sheasby
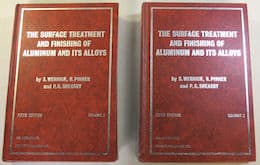
(note: this book is two volumes)
on eBay or
AbeBooks
or Amazon
(affil links)
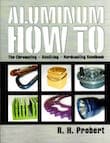
Aluminum How-To
"Chromating - Anodizing - Hardcoating"
by Robert Probert
Also available in Spanish
You'll love this book. Finishing.com has sold almost a thousand copies without a single return request :-)
A. Hi Daniel. The biggest area of expertise that people are usually lacking is experience with government regulations on the operation of anodizing shops (which you reference in question 7). Look into that before you go much further. Another key area is that you have to acquire an anodizing library; and anodizing training if you are serious should come next.
1, 2. Abrasion resistance can be tested with Taber abraders or other methods, but that is something you can probably farm out. A simple hall effect thickness tester is probably the tool you most need. After that, lab glassware and supplies for chemical analysis, seal quality tests, etc. Then cross sectioning equipment and a microscope. Others may give you a different list. Corrosion resistance is critical, and it's tested with a salt spray cabinet, but this can also be farmed out initially.
3. You can make a table and chairs for your shop by slinging a piece of plywood across sawhorses, and sitting on inverted plastic buckets, but you know you shouldn't. Similarly, a battery charger should not be used as an anodizing rectifier no matter how small your operation. As for the sizing, please see question 5.
4. Either cool the anodizing tank right or don't cool it at all. Right means a chiller, temperature regulators, and Teflon or titanium cooling coils -- an expensive proposition.
5, 6. Four ASF is way too low, 12 ASF is somewhat low. 40 ASF is way too high. I'd figure 15-20 ASF. The anodizing thickness vs. time depends on the alloy, but it shouldn't take 2 hours to anodize your parts. I'm not accustomed to using that 720 rule and I apologize that I can't run the thickness calculation for you right now, but my gut feel is about a half hour to forty five minutes will do it.
7. Manitoba is different than the USA, and I can't quote your regulations, but there will be wastewater limitations which require wastewater treatment.
Good luck.
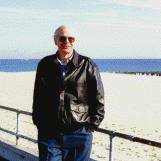
Ted Mooney, P.E.
Striving to live Aloha
finishing.com - Pine Beach, New Jersey
Q. I have some questions in regards to Type II Aluminum Anodizing. I am currently working with an electrolyte solution of 20% Sulfuric Acid and 80% distilled water and working with 6061 aluminum. Assuming my solution maintains a steady 70 °F, my questions are as follows :
1. What is the formula utilized when calculating the duration of the anodizing process. I understand that certain work condition variables are granted. Variables including the total surface area of the work piece, volts utilized and amperage utilized but there must be a basic formula from which one can conclude the duration that the workpiece must be anodized in order to obtain maximum thickness. I have read about the "720 rule" which goes as follows, 720 / ASF = Y, then Y x the thickness required. Unfortunately, this formula confuses me when it asks for a thickness value. Is this microns or inches? Simply for the sake of example, could somebody show me how to calculate the duration of the anodizing process for the following variables : Amps Per Square Foot = 20, Work Piece Surface Area = 1.75 square feet, Volts = 12, Oxide Thickness = 0.0005".
2. In regards to Amps and Volts, can somebody explain what the function of the Volts are? I have heard of people using much higher voltages and relatively low amperages and vice versa. What is the function of the Volts and what would the difference in outcome be if one utilized 12 volts opposed to 18 volts on the same piece in the same working conditions.
3. In regards to Amps, can somebody explain to me what the function of the Amps are. How is it different from Volts? What would the difference in outcome be if one utilized 25 Amps Per Square Foot opposed to 25 Amps Per Square Foot on the same piece in the same working conditions.
I thank everyone so much for their time, their guidance, their patience and most of all their help. www.finishing.com has been by far my greatest source for information to date.
Thanks again!
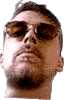
Daniel DeGueldre
anodizing shop entrepreneur - Ste. Anne, Manitoba, Canada
A. Dear Mr Daniel.
I'll try to clear some points, with my poor English, and I hope that I can.
1 - anodizing creates heat so you have to cool your solution, less than 22 °C, and the cooler the better. You can use lead cathodes and lead cooling coils.
2 - anodizing --oxygen sticks to aluminum, and the product of Al+O is Al2O3 WHICH IS ALUMINIUM OXIDE which is very hard, as hard as chrome, not conductive, and porous. That is why you need to increase the voltage slowly, whenever the current goes down, to keep current steady (the current can reach the aluminum surface only through the porosity). To get up to 35 microns you may need 12-15 ASF, voltage can go from 22 volts up to 40 and more volts (depending on thickness required), and up to 45 minutes. After anodizing, if you deform your part you'll notice cracks all over the deformed surface.
3 - after anodizing a proper deionized, or good quality water wash is very important
4 - NOW if you seal the porosity by boiling in hot water for 10 minutes or so, or sealing in other solutions, or dipping in some coloring, you'll have colored or plain corrosion resisting alum surface. But if you kept the part after anodizing without sealing at room temp for a day or more, or you heated in an oven, you'll have a very hard coat.
5 - regarding thickness control and the formula you mentioned, I'm not familiar with it, but I think that would be tricky because the current goes down and increasing or if the surface of the part gets hot you may dissolve your anodizing -- and that's why cooling and agitation is very important. Mr Daniel I liked the way you explained your situation and and I'll be glad if this helped.
Good luck and GOD BLESS
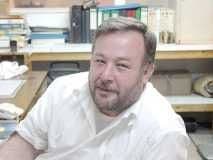
Khair Shishani
aircraft maintenance - Al Ain, UAE
A. The 720 Rule is: 720=ASF x minutes / mils. Where; ASF is Amps per square foot, mils is the desired coating thickness (1 mil = 0.001").
Rearranging to solve for time: 720 /ASF x mils = minutes
For a current density of 20 ASF, and a thickness of 0.0005" (0.5 mils); 720 / 20 x 0.5 = 18 minutes.
(I'm surprised that Ted isn't familiar with it; it has a solid basis in electrochemistry, being based on the Tafel equation. Its been around for decades).
The actual current you would apply is 1.75 sq,ft. x 20 ASF = 35 Amps. The required peak voltage is 0.95 Ohms per sq.ft / 1.75 sq.ft. = .54 Ohms. .54 Ohms x 35 Amps = 18.9 Volts. This assumes no voltage drops due to bad connections, and you haven't increased the actual surface area with racking.
Regarding Amps and Volts. Confusion occurs when the third entity is ignored, which is Ohms. Ohm's Law states that Amps = Volts / Ohms. (I=E/R) An anodizing setup is an electric circuit, as such it obeys Ohm's Law. In all things electrical; current (Amps) does the work, potential (Volts) serves to overcome the resistance (Ohms). Anodic coatings are formed by current, not voltage.
Relating this to anodizing. An electrical resistance exists when the anodic coating is forming, it is caused by the electrolyte being restricted by the porous anodic coating from reaching the base metal. As the coating grows, this resistance increases. his resistance sets the voltage when a given current is flowing. For 20 ASF, 9.4% electrolyte concentration by volume, and 70 °F., this resistance is about 0.95 Ohms per square foot. Its value is inversely proportional to surface area (2 sq.ft. = 0.475 Ohms). It varies a little with alloy as well.
BTW, "standard electrolyte" is 165 g/l by weight, which is 9.4% by volume. Your electrolyte concentration should be lowered, you are courting dissolution problems.
- Columbia, Maryland, USA
Ed. note: it is our sad duty to advise of the passing of Paul Yursis in August 2005.
Here is a brief obituary by Mike Caswell.
Thanks, Paul. Actually I think you mean Faraday's Law of Electrolysis rather than the Tafel Equation though :-)
Yes, I am familiar with this law, which says that 96,485 amp-seconds converts one gram equivalent weight of metal to or from ions. I know that you can tack the density conversion factor onto it, and end up with "1140 amp-minutes/sq. foot to deposit a thousandth of an inch of nickel" for example. The Metal Finishing Guidebook has a chart with those Faradays vs. thickness numbers for each different metal, but I don't do anodizing, didn't have the factor "720" for anodizing committed to memory, and didn't realize that it had a name. Thanks for letting me know of this practice!
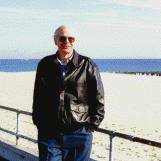
Ted Mooney, P.E.
Striving to live Aloha
finishing.com - Pine Beach, New Jersey
Thanks so very much for all the information provided in this forum post! It has been extremely helpful and has aided a great deal in setting me straight with some issues I've had for some time now. To everyone who has participated and those who may participate...Thank you!
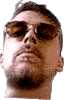
Daniel DeGueldre
anodizing shop entrepreneur - Ste. Anne, Manitoba, Canada
Q. Hey, I'm 16 years old and working in electronics while in high school. I thought a neat idea would be anodizing aluminum, titanium or color finishing steel. Right now I have access to Aluminum and sulfuric acid and distilled water. I am looking at doing several 2" x 2" to 4" x 4" samples and experiment with different lengths of time. I was wondering if anyone could give me some ideas of what amount acid I need and water. I am trying to use just enough, so a ratio would be best. Also, to get the acid I need to know what molarity is best. Any help at all is helpful. I know about titanium and steel I am clueless on but I heard of "color finishing" (not anodizing). Thanks,
Ryan G. [last name deleted for privacy by Editor]- Saskatoon, SK, Canada
2005
Q. I'm trying to change from Hard Anodizing by voltage to anodizing by current.
I understand the 720 rule, but don't understand where you get the ASF in the equation from.
What I know:
- I know how many mils I want.
- I know how to figure out the square footage of the part.
What I DON'T KNOW:
- What ASF I need to use on any given part.
Chris
Anodizing shop employee - California
June 3, 2010
by Runge & Kaufman
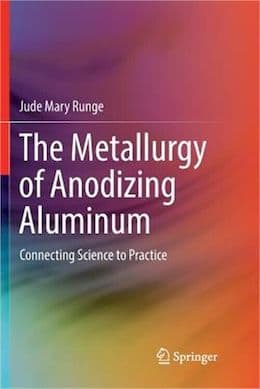
on AbeBooks
or eBay or
Amazon
(affil links)
A. Hi, Maurice. Some things we know from 'first principles', the rules of electrochemical science. The "720 Rule" (at least as an approximation) is one of those things because it's simply Faraday's Law of Electrolysis multiplied by some conversion factors. That is, you multiply the current density in ASF (amps-per-square-foot) times the anodizing time and divide by a factor to get the anodizing thickness. Specifically, you multiply your ASF times your anodizing time in minutes, and divide by 720 and you will get the approximate thickness in mils.
But in some other areas, including what ASF range will generate satisfactory anodizing, our science isn't advanced enough to give us a number based on first principles; rather we still rely on empirical knowledge -- what we have found will probably work and what probably won't. ASF is empirical information rather than something we can calculate.
36 ASF is usually considered the maximum practical current density, with many experienced practitioners feeling that 12-24 ASF is the number you should use in production to keep out of trouble. You can search the site with the term "hardcoat current density" for many interesting discussions on that topic. Good luck!
Regards,
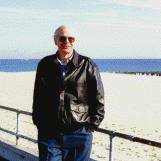
Ted Mooney, P.E.
Striving to live Aloha
finishing.com - Pine Beach, New Jersey
Q. Hi, salam to all of you,
I read the conversation. I don't know the 720 formula -- but in fact I have another formula to check thickness of anodizing film, thats is...
Thickness in micron = 0.3* current density in A/dm2 * time
In this formula there are three parameters which you can change or fix:
If you want to check thickness of anodize layer then you can fix current density and time,
for example: you fix current density 1.5A/dm2 with 30 minutes of time then:
microns = 0.3 * 1.5 * 30 = 13.5 microns
- Pakistan
September 16, 2012
on AbeBooks
(rarely avail.)
or Amazon
(rarely avail.)
(affil links)
A. Thanks Azeem.
Let's see then --
According to your 0.3 rule,
A/dm2 x minutes * 0.3 = microns
And according to the 720 rule,
A/ft2 x minutes / 720 = mils
So let's try plugging your numbers into their 720 rule:
1 A/dm2= 9.29 A/ft2, so ...
1.5*9.29 x 30 / 720 = 0.5806 mils, which is 0.0005806 inches = 14.7 microns
We're pretty close, thanks :-)
Regards,
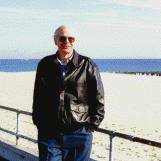
Ted Mooney, P.E.
Striving to live Aloha
finishing.com - Pine Beach, New Jersey
Q. I'm using the 312 Rule instead of the 720 Rule cause I'm using metric units.
So I created an Excel sheet to facilitate the calculations of the time, current, and voltage required for anodization.
This calculation is based on the procedure in Paul Yursis' article.
When I compare the result from this sheet with the results from the 720 calculators available online, I get the same time and current but the voltage is not the same. That is due to the value of the resistance.
So when I go to my anodization process all I do is to try to adjust the voltage to reach the required current value which is not stable and needs to be adjusted from time to time to avoid current drop.
So I have 2 questions:
1 - how to calculate the resistance of the electrolyte?
2 - how to fix the non-stable current value?
Note that the sulfuric acid concentration is 11.5 % by volume, and I'm using titanium racking.
- Cairo, Egypt
April 23, 2014
A. Hi Abdel-Moniem, I think there is a misunderstanding here. The resistance of the solution is not changing significantly; rather, the resistance of the part is changing because the anodized film which you are building on it is highly resistive/insulative, and gets ever higher in resistance as it builds in thickness.
That is why people recommend anodizing by current, rather than by voltage. Set your rectifier current to 12 or 18 amps/sq. foot, or whatever you find that you can succeed with, and then let the voltage vary as necessary to achieve it. Good luck.
Regards,
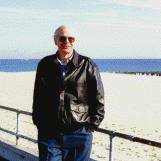
Ted Mooney, P.E.
Striving to live Aloha
finishing.com - Pine Beach, New Jersey
Q. Dear sir,
Please provide me how much current and voltage needed in anodizing for 180*2*1 long hollow aluminium profile.
student - gorakhpur, uttarpradesh, India
July 9, 2014
A. Hi Deepak.
Voltage will be a bit over 12 V depending on the alloy and the distance from workpiece to cathodes, but an 18 volt rectifier is a better bet. As mentioned, the current will be about 12-18 Amps per square foot (the lower end for hobbyist LCD approach). You need to calculate the surface area of the profile you will be anodizing, and recognize that 12 V or 15 V is the terminal or ending voltage. You need to start much lower to not exceed the 12-18 ASF when there is no anodizing on the part yet, such that it's still highly conductive. You gradually up the voltage. That's why it's generally better to use a rectifier with current control than voltage control.
Regards,
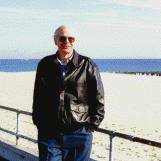
Ted Mooney, P.E.
Striving to live Aloha
finishing.com - Pine Beach, New Jersey
Q.
Dear All,
Please explain to me the 720 rule, with example.
- Mumbai, Maharashtra & India
November 14, 2014
A. Hi Rahul. Paul Yursis did that for us already. Look above for his name. If you can't follow it, please quote something he said and explain what the difficulty is. Also, note that others, like Azeem Khan have expressed the same rule in metric units if you are more comfortable with that. Good luck.
Regards,
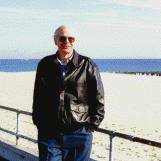
Ted Mooney, P.E.
Striving to live Aloha
finishing.com - Pine Beach, New Jersey
Q. I have a product having Surface area 2.334 x 10 ^-5 foot square. I want to do soft anodizing and I want to know what should be the rectifier rating (above surface are is of one component).
Rishi Sharma- ghaziabad , India
May 11, 2017
A. Hi Rishi. Although 2.334 x 10 ^-5 foot square X 15 ASF = 3.501 x 10 ^-4 Amps, I suspect that we're losing something in the translation :-(
Regards,
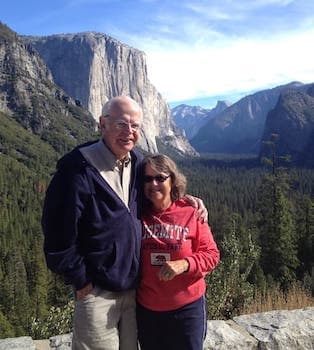
Ted Mooney, P.E. RET
Striving to live Aloha
finishing.com - Pine Beach, New Jersey
⇦ Tip: Readers want to learn from Your Situation 🙂
many readers skip abstract questions.
Q. Calculations using 720 rule, Do I need to calculate racks area as well?
H Patel- Jackson, Mississippi, US
October 15, 2019
A. Hi H. Please try to get back to us with the details of your situation rather than an abstract question. Titanium racks or aluminum racks? What type of work? Are the parts alkaline etched?
Anodizing of architectural extrusions, as one example, is sometimes done on aluminum racks with no rack stripping at all, just fresh aluminum screws each cycle (which adds virtually no surface area to the calculation); although the area of the racks is large it doesn't count because it all stays anodized. But if you are anodizing the rack or rack tips as you anodize the parts, yes, whatever area you are actually anodizing is what counts in your 720 rule. Then too if you are doing a heavy etch it can strip the anodizing from the racks.
I think the bottom line is that the 720 rule can help you plan, but you can't use it with such careful nuance that actual thickness measurements become unnecessary :-)
Regards,
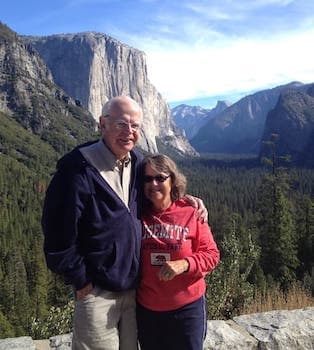
Ted Mooney, P.E. RET
Striving to live Aloha
finishing.com - Pine Beach, New Jersey
A. As Ted Says, "careful nuance". the 720 "rule" is practically approximate in a small range of parameters, but since the anodic film builds exponentially with time and thickness, it is not arithmetically accurate. Use nuance.
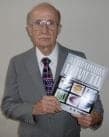
Robert H Probert
Robert H Probert Technical Services

Garner, North Carolina
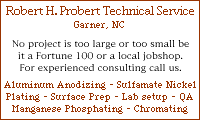
Q. Hi, I've to setup and start up a new sulfuric acid anodizing line for aluminium. Can you guide me where to start first? What I should do?
This anodizing line is for Type II and Type III.
The control parameter or the specification limit is standard or varies? How to know the temperature, pH for each anodizing process?
- Malaysia
March 10, 2022
A. Hi Nas. If you are a hobbyist trying to familiarize yourself with anodizing, you'll find many of your answers on this thread, and all of them by searching this site (although bouncing between simple things you've heard a hundred times and things too complicated for you to study until you've picked up some intermediate knowledge isn't very efficient). Books are better for tutorial learning, if your library has any, because the author has spent months or years arranging it all in that you can learn in a proper sequence/progression.
But if you are planning on building a production facility you honestly should retain a consultant or at least someone with a good deal of experience. Although I stopped consulting a decade ago I did it for 25 years and must emphasize that it is the early decisions that really matter, not the ones made when it is too late for anything but a Hobsen's choice :-(
It sucks to be left with only enough room for 8 tanks if you ought to have 9, or to have wide shallow tanks when narrow deep tanks would have been better or vice versa. But early decisions include whether you'll run 40-hours / 1-shift vs. more shifts, what size range parts you will accept, whether you want to primarily serve architectural, automotive, aerospace, medical, or consumer markets, whether you'll take low markup commodity work or only the tough stuff, what ancillary services you want to offer such as precision masking, bright dipping, 2-step coloring, etc.
Luck & Regards,
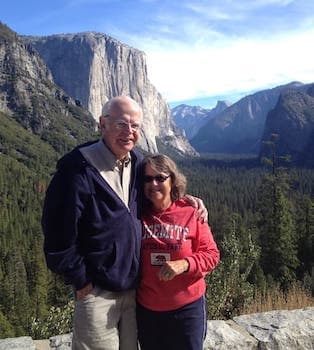
Ted Mooney, P.E. RET
Striving to live Aloha
finishing.com - Pine Beach, New Jersey
A. There are several consultants on Finishing.com who can walk you through setup. If you send me an email I can at least send over initial information on what you will need.
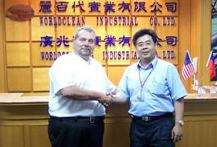
Drew Nosti, CEF
Anodize USA

Ladson, South Carolina
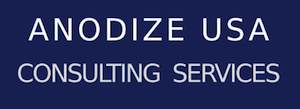
Q, A, or Comment on THIS thread -or- Start a NEW Thread