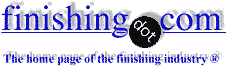
-----
Electroplating effect on tensile strength
I manufacture loops in steel grade 42Mn6. Now after heat treatment and tampering the tensile strength is OK but after electroplating the tensile strength falls marginally. The HRC is constant after tampering on 43-45 HRC but load falls from 5550 kgs to 4950 kgs. Now can electroplating effect on tensile strength or degreasing the metal in HCl acid effects the tensile strength.
Saurabh KhnadelwalResearch - Delhi, India
2004
Too little information. However, as a generalization, electroplating can cause hydrogen embrittlement, especially if the deposition is not 100% efficient. Using hydrochloric acid with ferrous based systems can also cause weakening because of chloride induced corrosion as well as hydrogen embrittlement.
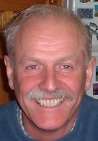
Trevor Crichton
R&D practical scientist
Chesham, Bucks, UK
2004
Thanks for your reply. I'll elaborate the problem. We have wire rod grade SAE 1541 with composition: C 0.39-0.46, Mn 1.30-1.65, Si 0.10-0.40 and P & S are <= 0.035. Now on making wire loops of them we are hardening the material at 780 °C for 35 minutes soaking. Then we quench it in polymer solution water based to avoid cracks.We achieve a quench hardness of 49-55 HRC. Now on tampering the material at 450 degrees for 10 minutes it gets a hardness of 39-45 HRC. Till here we achieve our results for 5000+ B/s tensile load. But just when we try to electroplate the material the tensile strength deteriorates drastically. The load becomes erratic and varies from 4500-6000 kgs whereas we need 5000+. Now does immersing in HCl for cleaning or cleaning in caustic soda ⇦liquid caustic soda in bulk on Amazon [affil link] solution or H2So4 is the problem? Or if anyone can suggest me any other hardening process.Really in Fix
Saurabh Khnadelwal- Noida, India
2004
HCl as an etch is not a good idea with ferrous metals. If you want to use an acid pretreatment, I would suggest anodic sulfuric acid. this eliminates the risk of chloride corrosion and hydrogen embrittlement. One problem with all electroplating is the risk of reducing the "engineering shock properties" of the substrate by the increased problems associated with crack propagation in the coating material. You do not say what you are plating with, so we can only speculate.
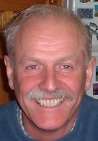
Trevor Crichton
R&D practical scientist
Chesham, Bucks, UK
2004
2004
As informed I would like to give you following details:
1. We are using 8mm-14mm wire rod to manufacture wire loops.
2. While formation the hardness of wire rod is already 22 HRC to 29 HRC and chances of microcracks is there.
3. After hardening the variation in hardness is 49-52 HRC generally but at times in some pieces say less than 0.5% we get 42 HRC and even 52 HRC.
4. After tampering we get hardness HRC 39-42 and in less than 0.5% we get even 32 HRC as well 46 HRC.
5. After tampering we are doing Zn i.e. zinc electroplating with yellow passivation done with chromic acid.
6. For cleaning we dip the product in weak HCl solution in water for 5-8 minutes and then barrel it in caustic solution without current for half an hour. after that we dip it again in HCl for 20 seconds and rinse it and electroplate in the barrel.
7. We are using both the acidic bath as well as cyanide having following details: Acidic bath: Zinc chloride, Zinc metal (Liquid) and boric acid. Cyanide bath: Zinc oxide, Sodium cyanide, caustic soda ⇦liquid caustic soda in bulk on
Amazon [affil link]
8. We tried to clean the pieces in alkaline solution but the pieces do not get cleaned and is not possible to plate the material. But the tensile strength is not reduced to that extent which was in HCl acid.
Now I wanna ask that can HCl dipping make the pieces so brittle that they fail even before reaching their required load? Does hydrogen embrittlement takes place and in which process? Yellow passivation gets destroyed when we bake the material to remove hydrogen. Please suggest.
Saurabh Khandelwal- Noida
2004
Mr. Khandelwal,
Hardened steel parts (core > 320 HV or surface > 350 HV) are susceptible to hydrogen embrittlement when subjected to acid cleaning, acid pickling, or electroplating, due to the generation of nascent hydrogen. The standard practice is to bake these components shortly after the plating process but BEFORE the chromating process. SAE USCAR 5 requires the interval to be 1 hour maximum. At the hardness that you indicated after tempering (39-42 HRC), SAE/USCAR-5 requires that the parts be baked for a minimum of 8 hours at 200 ± 5 C. I strongly suggest you purchase a copy of SAE USCAR 5 and SAE USCAR7 if you intend to electroplate hardened steel components.
Toby PadfieldAutomotive module supplier - Michigan
Q, A, or Comment on THIS thread -or- Start a NEW Thread